Top Flite Holy Smoke User Manual
Page 5
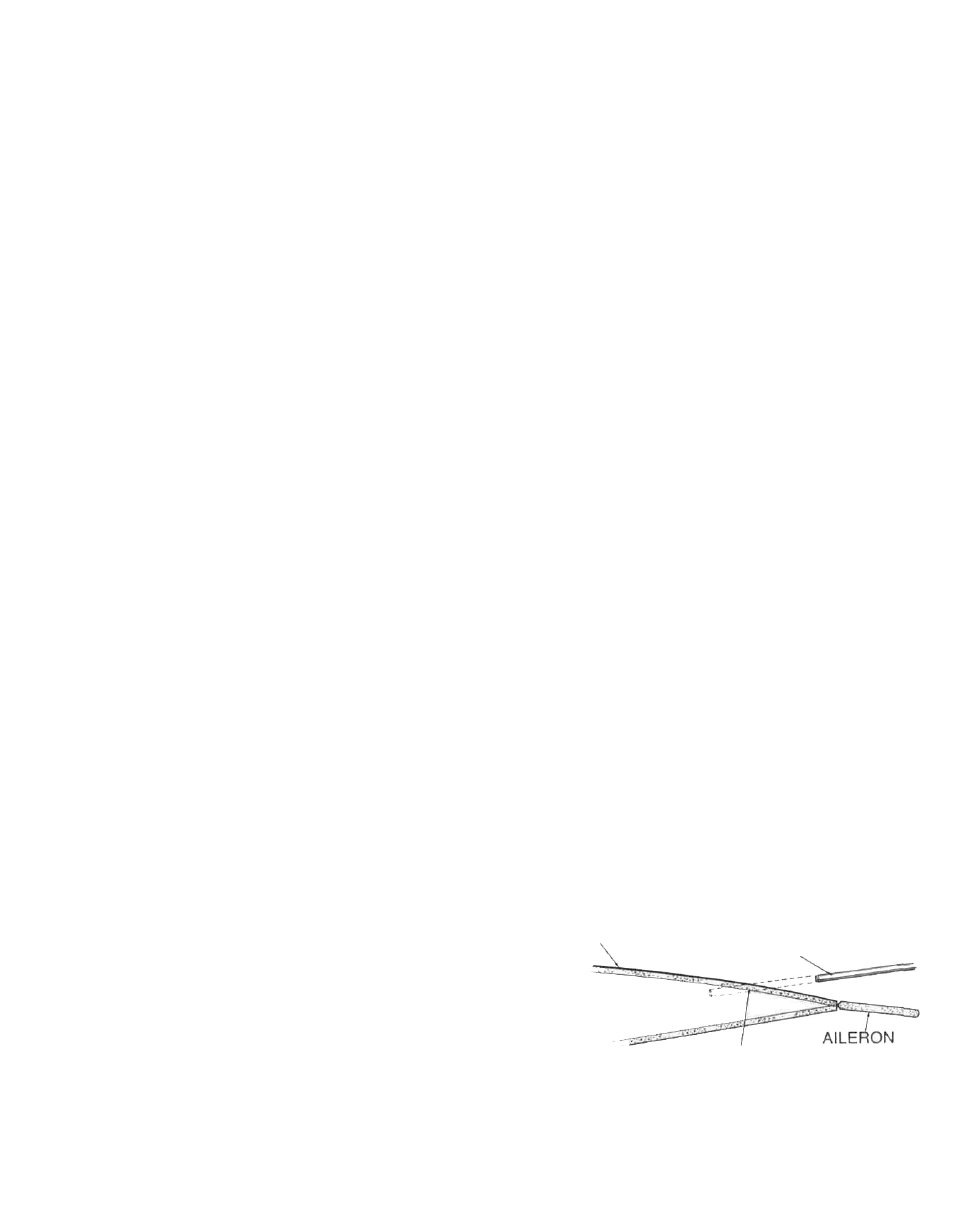
planking in place and allow to dry.
16. Again using the X-acto knife, remove all remaining
building tabs from the bottoms of all of the ribs. Ac-
curately bevel cut the ends of the two remaining bot-
tom spars and glue in place.
17. From your parts bag locate two 5-1/4 " long slotted
hardwood landing skid mounts and two slotted lan-
ding gear uprights. Epoxy the two 5-1/4" long skid
mounts in place in the cutouts provided in ribs W-2
and W-3 as shown on the plans. Be sure the slotted
side is exposed! Use a 3/32" dia. drill bit to drill a hole
through each block, in the slot, at the outboard face
of W-2. Temporarily install the two formed 3/32" dia.
M.W. skids in place in the slotted blocks. Apply
epoxy to the two short slotted blocks—on the slot-
ted side and bottom edge—and glue these in place
over the stub ends of the wire skids and against W-2.
Carefully remove the wire skids and allow these
assemblies to cure.
18. While the bottom of the leading edge crutch
assembly and the ribs are still exposed, finish gluing
these pieces together as you did on the top. A bead
of slow set CA on each side of each rib will do nicely.
19. Cut, fit and glue the bottom leading edge planking
pieces in place. Note that like the top planking, the
rear edges are cut to fit halfway across the width of
the spar and that the inboard ends are cut to fit flush
with the inside faces of the W-1 ribs and the W-9
former (the exposed cavity described by the shape of
W-7 will be filled-in with balsa blocks and the hard-
wood nosegear mount). When dry, use your sanding
block to sand the outer faces of W-5 tip ribs flat. Us-
ing the two remaining pieces of the 1/2" x 1-1/8"
leading edge stock, glue these in place to the W-5's
as wingtips. Sand the leading and trailing edges of
these tips flush with those of the wing when viewed
from the top. Sand the tops and bottoms to match
the airfoil contours except for the leading edge; this
will be shaped later.
20. If so desired, now is a good time to lay in a strip of
light fiberglass along the inside centerline of the top
planking from W-9 back to W-10. Although there is no
real stress in this area, fiberglass does serve to stif-
fen and strengthen the wood. This is also a good
time to give the entire tank/radio compartment a
coat or two of polyester resin. While the resin is cur-
ing, take the time to make your fuel tank. An 8 ounce
DuBro tank is shown on the plans. We've also used a
Pylon SS-8 Slant tank which fits nicely in place on its
side thus giving you a bit more room in the nose, if
you need it. Set the tank aside; it will be installed in a
little while.
21. You now must install the servos on their respective
hardwood mounts (four pieces of 1/4" x 3/8" x 5"
basswood are supplied for this purpose). First cut
the length of these rails to fit snuggly between the
W-1 sides as shown. Start with the rearmost mount
and epoxy it in place at the lowest possible point
that still allows your servos to fit without contacting
the top planking. Using your servos as spacers, in-
stall and glue the next rail in place—remove the ser-
vos. The next rail to be installed is the rear aileron
servo mount. Note that in the cross-section we show
that the aileron servo is mounted lower than the two
rear elevator and throttle servos. This is done to
allow clearances of the various drive cables. Again
using your servo as a spacer, install and glue the for-
ward aileron servo rail in place and remove the servo.
Allow the epoxy to cure. Cut about 19" of white tub-
ing (two piece @ 36" supplied) and install it in the
left wing panel from just inside W-1 through all of the
wing ribs, exiting at the wing tip; this is the receiver
antenna tube. CA adhesive works well to secure this
tube, and the others, to each rib if you first lightly
sand the tube's surface. Using wood screws (not
supplied), position and install the three required ser-
vos.
22. The throttle pushrod, unlike the others is made up of
a plastic inner and outertubing (one piece of each @
12" supplied). Install and glue in place the outer
throttle pushrod tubing as shown on the plans. Next,
drill a small dia. hole, about 1/8", through W-10 where
the elevator pushrod (one piece @ 12", threaded
one-end, supplied) exits the elevator servo toward
the rear—see cross-section of radio compartment
on plans. Use an X-acto knife to now make a small ex-
it slot in the bottom planking to allow the free fore
and aft movement of the elevator pushrod. Note that
we are showing a "Z-bend" at the servo output arm.
Once you're satisfied you can remove and set aside
the elevator servo, its pushrod and the throttle servo,
they have served their purpose for now and will be in-
stalled after the airplane is finished.
23. From you parts bag, locate the small metal "ball-
link" (threaded), the small nut for it, the nylon dual
take-off aileron ball connector and three brass
threaded couplers. As shown on the plans, the ball-
link is mounted on your aileron servo's output arm
and secured with the nut. Now snap the nylon dual
take-off connector on the ball-link, positioned as
shown on the plans. Drill two 1/8" dia. holes, one
through each W-1 rib side at the exit points of the
aileron drive cables. From your kit box, locate the re-
maining 36" length of braided cable. Cut each of
these in two equal 18" lengths (a carbide cut-off
wheel will cut the cable nicely). Use a soldering iron
to solder a threaded brass coupler on one end of
each cable. Slip the white tubing over the cable.
1/8" DIAMETER SHARPENED
BRASS TUBING
UNDERSIDE OF
WING
AILERON TUBING
EXIT LOCATION
Working on top of the exposed ribs, visually line-up
the coupler end of the cable/tubing assembly with
the previously drilled hole in W-1 and either pin it in
position so that it does not move or have a friend
hold it for you. As shown on the plans, gently bend
5