Top Flite Elder 40 User Manual
Page 10
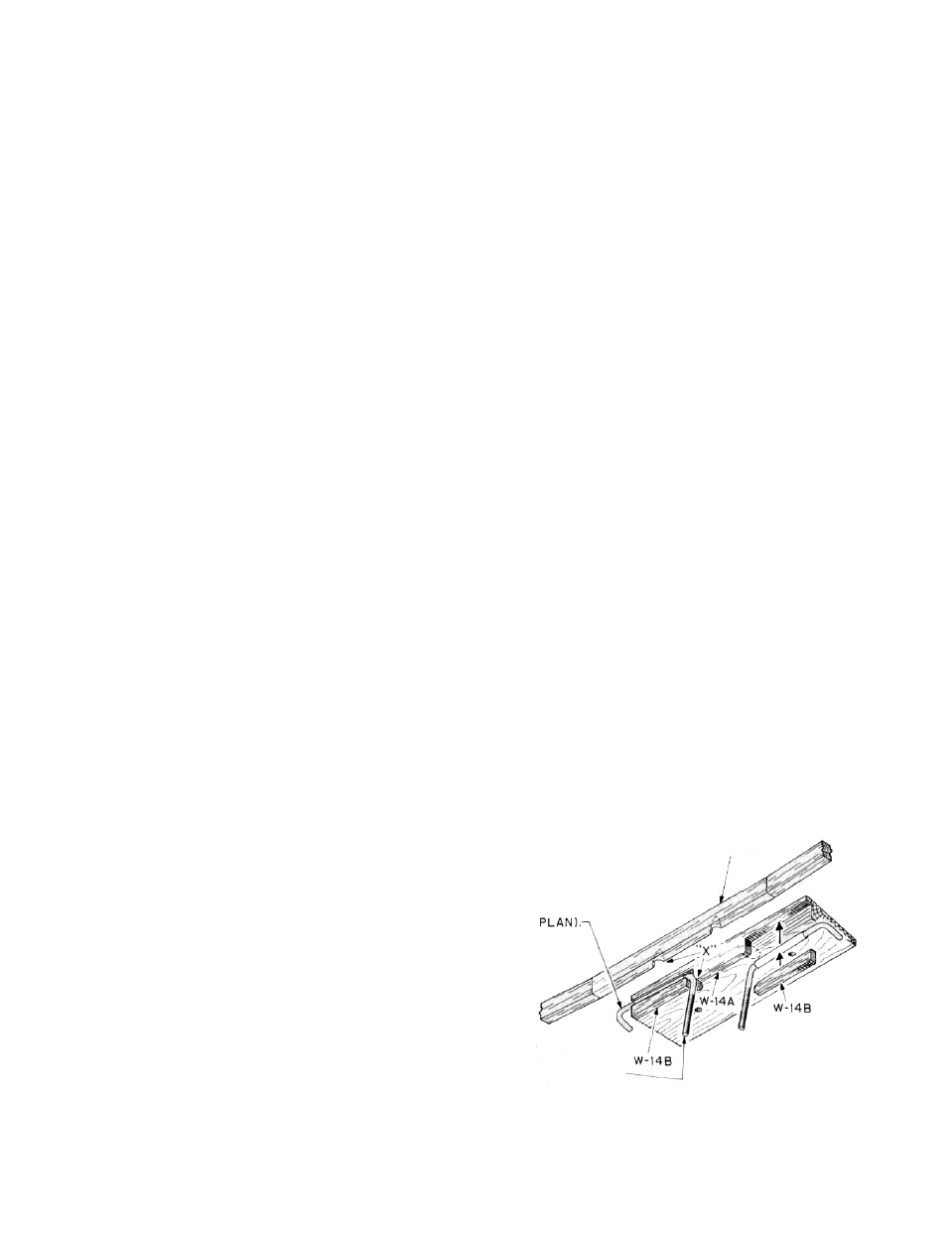
5. The same process is now used to make the rear
tailskid assembly. First bend the 1/16" dia. M.W. pro-
vided to the shape shown using pliers. Wrap the tip
of the skid with soft copper wire and solder. Now
tapethe main skid wire in place tothe bottom rear of
the fuselage. Locate the pre-bent tailskid support
wire and wrap it in place to the tailskid with soft wire.
Solder it in place to the skid. Remove the assembly
from the fuselage and again, clean the solder joints
completely.
6. Remove the main landing gear from the fuselage.
The landing gear and tailskid are now complete and
can be used as is or painted flat black or aluminum
(we use epoxy paints for this as well as other pain-
ting needs on this airplane). As we did on some of our
prototypes, you may wish to add wood backing to
the wires. Sand these to airfoil shape and paint them
a wood color—looks great! We used 1/8" x 1/4" hard
balsa with a 1/8" dia. "groove" sanded into one edge,
carefully fitting the piece in place. We glued the
wood to the metal with thick CA adhesive and sand-
ed the whole affair smooth. Then we used clear,
paintable Monokote to cover the "wooded" parts of
the landing gear to provide a one-piece look and air-
brushed wood-colored epoxy paint on the whole
thing.
FINAL ASSEMBLY
1. Locate one of the 1/4 " dia. x 36" dowels provided in
your kit and cut a 3" length, this to be used for the for-
wardwing hold-down. Insert this dowel intothewing
center-section, leaving 1/4"-3/8" of it exposed in front
of the leading edge to engage the F-6/F-7 former
assembly with the previously drilled hole. Now in-
stall the center section in place on the fuselage with
the dowel engaging the hole in F-6/F-7, again being
sure that it is squarely in place. Liberally apply epoxy
around and beneath this dowel, in the wing center
section area. Next, position and glue in place the
two remaining W-1A half ribs into position on each
side of the dowel. Fill the resulting cavity above the
dowel with more epoxy and allow the structure to
cure.
2. Remove the center section from the fuselage. Carve
and sand the short leading edge section to shape,
matching the two leading edges of the wing panels.
3. The two wing panels can now be permanently at-
tached to the wing center section. We recommend
that you use epoxy for this operation. With the
center section flat on your building surf ace, slide the
two panels in position onto the exposed arms of the
front, center and rear dihedral braces. The fit should
be accurate; the front brace fits against the back
face of the panel's leading edge, the center brace is
in contact with both the top and bottom spars and
the rear brace is inside of the top and bottom rear
trailing edge sheet strips. The panel's spars, leading
edges and trail ing edges should also be cleanly con-
tacting the outside surface of the center section's
sides. Take time here to ensure that this is the case
before committing to actual attachment. Locate or
make a couple of 3/4" high supports for the wingtips
to provide the required dihedral angle. Now epoxy
the panels in place to the center section—don't use
so much glue that it runs or drips but enough to pro-
vide a good glue joint. One-hour epoxy is best for this
step. Allow the structure to cure completely.
4. As shown on the plans, a forward and rear "cockpit"
former was made from 3/32" sheet, placed in-between
the two inboard W-1 B's, full-depth to these two ribs.
Be sure that the forward cockpit former is far enough
back to allow insertion of your aileron servo.
5. The two inboard panel rib bays (between W-2B and
W-1 B) and the center section can now be completely
sheeted, cross-grain, as shown. We have found that
it is helpful, when glueing this sheeting in place, to
"share" the width of the center section's outboard
W-1A and B ribs with both the wing panel and center
section's sheeting edges, thus providing a glueing
surface for both. When dry, use sandpaper to
smooth the wood and to match the sheeting with the
leading edges.
6. In this step you are going to assemble the hardwood
trailing edge and aileron torque tubes and wires to
the wing center section—please refer to the detail
drawing provided to understand the parts relation-
ship. Glue the two W-14B's in place to the forward
face of the hardwood trailing edge, their outboard
ends flush with the outboard ends of the trailing
edge. Note that there is a right and left aileron drive
assembly. As shown, the trailing edge must be
grooved a little to allow aft movement of the thread-
ed linkage arms. Do this now with either a rat-tail file
or a Moto-tool and router bit. Now glue W-14A in
place, thus providing a "nest" for each of the torque
rod assemblies. As shown, knock-off the corners of
W-14A to allow torque rod movement. Rough-up the
brass sleeves on each of the torque rod assemblies
and carefully glue them in place with one-hour epoxy
—do not get adhesive on the torque rod arms.
S H O R T B E N T LEG FITS H O L E
A N D T U B E I N ROOT E N D OF
S H A P E D A I L E R O N (SEE
W I N G
THIS LEG OF
A I L E R O N TORQUE
ROD C O N N E C T S TO
SERVO LINKAGE
SHAPED HARD WOOD WING
MOUNT (NOTE C L E A R A N C E
SLOTS " X " ) TO ALLOW FORE
A N D AFT MOVEMENT OF
A I L E R O N T O R Q U E ROD ARM
1/4" X 3/8'; T.E. (NOTE CLEARANCE
SLOTS FOR AILERON TORQUE
ROD MOVEMENT)
DETAIL OF WING CENTER SECTION
AT TRAILING EDGE
( A S SEEN FROM BELOW)
10