Novak Tempest Max ESC (1760) User Manual
Introducing, Specifications, Tempest accessories
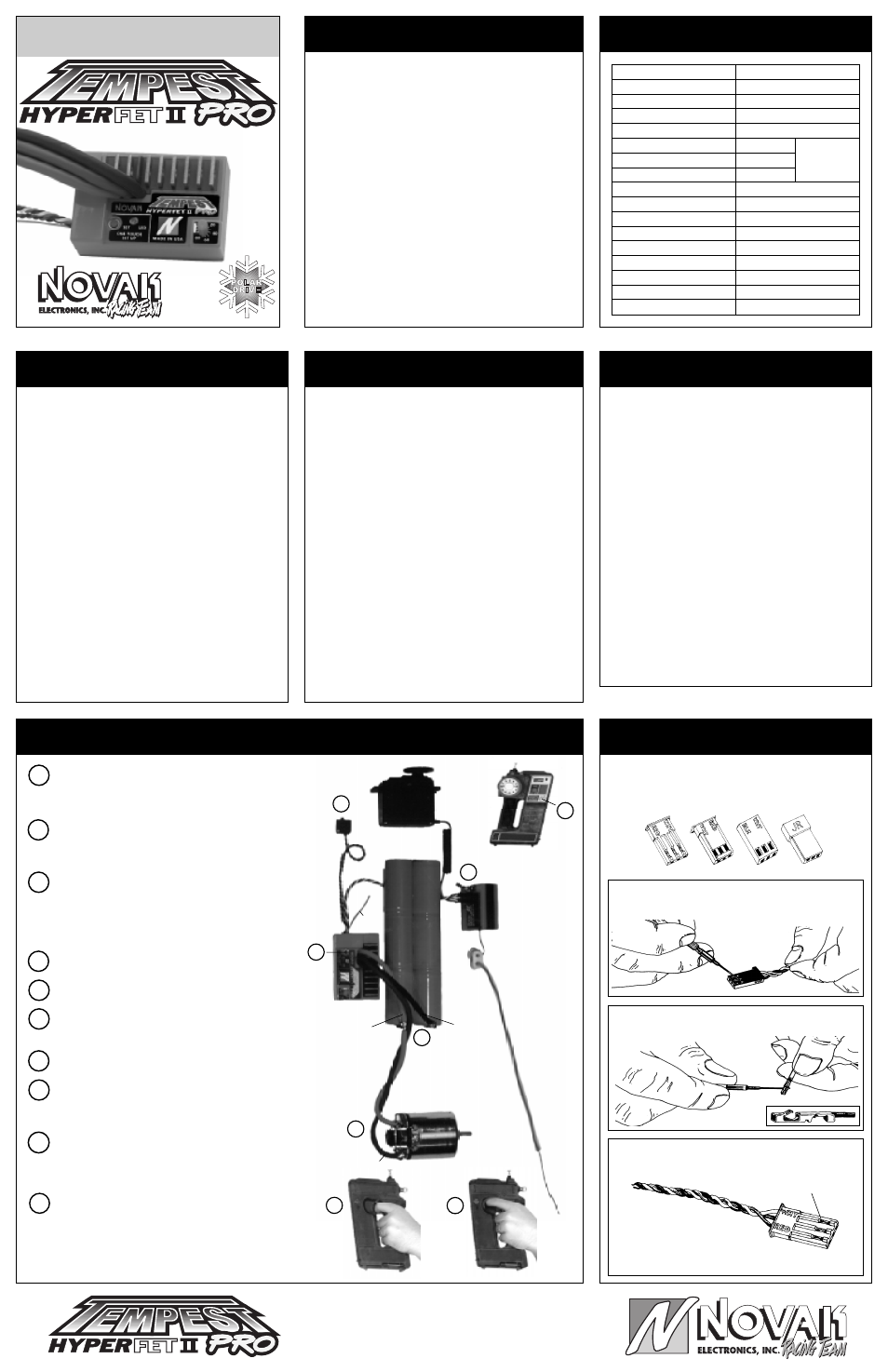
OPERATING INSTRUCTIONS
INTRODUCING
THE
TEMPEST
SPECIFICATIONS
Input Voltage
4-10 cells
(1.2 volts DC/cell)
Case Width
2.04 inches [51.82 mm]
Case Depth
1.35 inches [34.29 mm]
Case Height
0.73 inch
[18.54 mm]
Weight
(w/o heat sinks)
2.46 ounces [69.74 g]
On-Resistance
@ Transistors
1.167m
Ω
Rated Current
420 amps
Braking Current
210 amps
BEC Voltage
6.0 volts DC
BEC Current
5.0 amps
Wire Size
(Battery/Motor)
12 gauge
(Super-Flex 12™)
Wire Length
(Battery/Motor)
9 inches
[228 mm]
Signal Harness Length
8 inches
[203 mm]
Transistor Type
HYPERFET II™
Current Limiter Range
20 to 80 amps / OFF
PWM Frequency
2500 hertz
(fixed)
Part Number
1760
@ 25
°
C transistor
junction temp.
The Novak Tempest Pro combines the power of HYPERFET
II transistors with full-digital micro-computer control to give
you the smoothest, fastest, and coolest speed control the
racing industry has to offer. Team driver or not!
The Tempest Pro features Novak’s exclusive Polar Drive
Technology™ that gives increased power with operating
temperatures cool enough that heat sinks are not needed.
This means smoother throttle response along with quicker
acceleration, increased radio system range, and longer run
times than conventional ESC’s (Electronic Speed Controls).
All this and the ability to run the hottest modified motors.
SIX HYPERFET II drive transistors and new Super-Flex 12™
wire give demanding racers the lowest voltage drop and
highest current rating in the industry, while THREE more
HYPERFET II’s supply the braking circuit with more power
than any other racing speed control.
Other features include the original One-Touch Set-Up™,
Radio Priority & Digital Anti-Glitch Circuitry™, the Novak
Input Plug System™, CLC II™ current limiter with ‘OFF’
position, ultra-light case design, and a heavy-duty BEC with
the power to handle today’s high power servos.
TEMPEST ACCESSORIES
MOTOR CAPACITORS
To prevent radio interference problems, you must have
three 0.1
µ
F capacitors properly installed on every motor.
Included with the Tempest Pro speed control are three
0.1
µ
F (50v) capacitors for one motor. Additional 0.1
µ
F
(50V) capacitors are available in Novak kit #5620. Refer
to Step 3 for motor capacitor installation instructions.
SCHOTTKY DIODES
The Tempest Pro uses an external Schottky diode. For op-
timum performance, we suggest installing the Schottky
diode on the motor. One Schottky diode is included with
the Tempest and must be installed as described in Step 3.
If using a low turn modified motor, it may be necessary to
use two Schottky diodes on the motor. Install the second
Schottky diode as shown in Step 3. Additional Schottky
diodes are available in Novak kit #5640.
HEAT SINKS
Heat sinks are not required with the Tempest. However,
if transistors get excessively hot during operation, the
added cooling provided by heat sinks will result in a slight
increase in efficiency. An optional Heat Sink Set is avail-
able as Novak kit #5407. Heat sinks are recommended
for multi-motor/heavy load applications and set-ups with
limited air circulation.
PRECAUTIONS
• READ INSTRUCTIONS CAREFULLY BEFORE USING!
• WATER & ELECTRONICS DON’T MIX! Do not operate
model in or around water. Never allow water, moisture,
or other foreign materials to get inside the ESC.
• 4 to 10 CELLS ONLY Never use more than 10 cells (12
volts DC) in the main battery pack.
• MOTOR CAPACITORS REQUIRED Three 0.1
µ
F (50V)
ceramic capacitors must be properly installed on every
motor to prevent radio interference.
• NO REVERSE VOLTAGE! Reverse battery polarity can
damage speed control––Disconnect battery immediately.
• DON’T LET TRANSISTOR TABS TOUCH Never allow
the two transistor tab banks to touch each other or any
exposed metal, as this will create a short circuit and dam-
age the speed control.
• DISCONNECT THE BATTERIES Always disconnect the
battery pack from the speed control when not in use.
• TRANSMITTER ON FIRST Always turn on the power of
your transmitter first so that you will have control of the
radio equipment when you turn on the speed control.
• DON’T LET INPUT WIRES TOUCH! Never allow the input
harness’ black and red wires touch each other while the ESC
is on, as this will create a short circuit and damage the ESC.
• INSULATE WIRES Always insulate exposed wiring with
heat shrink tubing to prevent short circuits.
RADIO INTERFERENCE
The high frequency switching operation of electronic
speed controls can generate radio interference. Here are
some common causes of radio interference problems:
• CAPACITORS NOT INSTALLED ON MOTOR Electric
motors generate radio noise that can interfere with the
receiver. To prevent radio problems, every motor must
have three 0.1
µ
F (50V) ceramic capacitors installed on
it. Refer to Step 3 on back page for proper installation.
• RECEIVER/ANTENNA INCORRECTLY MOUNTED The
receiver and antenna should be mounted as far from
the motor, power wires, battery, and servo as possible,
as these components all emit radio noise. On graphite
or aluminum, place receiver on edge with the crystal
and antenna as far above the chassis as possible. Mount
the antenna close to receiver and trail any excess wire
off the top of antenna. Do not cut or coil excess wire!
• MOTOR BRUSHES WORN As motor brushes continue
to wear, excessive motor noise will be generated. To
avoid radio interference, worn motor brushes should
be replaced. The motor commutator may also need to
be cleaned or trued and can be machined to help the
motor run more efficiently.
TEMPEST QUICK SET-UP
FOR DETAILED INFORMATION REFER TO STEPS 1 THRU 5
B
C
D
E
F
G
H
I
J
INSTALL SPEED CONTROL
Use double-sided tape to mount ESC in model where the
power wires are neatly routed away from the receiver and
antenna. For more details refer to Step 2 on back.
CONNECT SPEED CONTROL TO RECEIVER
Plug the ESC input signal harness into the throttle channel
of receiver. Make sure the proper plug plastic is installed
on ESC signal harness. Refer to Step 1 for changing plug.
CONNECT SPEED CONTROL TO BATTERY
Solder the BLACK wire of ESC to negative of a completely
charged 4 to 10 cell battery pack (1.2 volts DC/cell).
Strip a short section of insulation off the RED wire of ESC
where it will attach to battery positive.
Solder stripped section of RED wire to battery positive.
TURN ON TRANSMITTER POWER
Refer to Step 4 on back for transmitter adjustments.
TURN ON SPEED CONTROL
Slide ON/OFF switch to ON position.
PRESS AND HOLD SPEED CONTROL SET BUTTON
With transmitter throttle in neutral position, press and hold
SET button until status LED turns solid red, then release.
PULL THROTTLE TO FULL-ON POSITION
Hold until status LED turns solid green.
PUSH THROTTLE TO FULL-BRAKE POSITION
Hold until status LED blinks green, then return throttle to
neutral position. LED will then turn solid red indicating
proper programming and throttle is in neutral position.
CONNECT SPEED CONTROL TO MOTOR
Turn off speed control and then transmitter.
Solder the BLUE wire of ESC to motor negative.
Solder the end of the RED wire of ESC to motor positive.
STORM THE TRACK & WIN!
Turn on transmitter and then speed control.
You are now prepared to experience the smoothest
motor control, lowest voltage drop, and highest
current rating available in racing speed controls!
NOVAK ELECTRONICS, INC.
18910 Teller Avenue
Irvine, CA 92715
DETAILED INFORMATION
Included with the Tempest Pro is the Novak Input Plug
System
TM
to convert the Futaba J style signal harness to
be compatible with Airtronics, KO, Kyosho, JR, and Hitec
radios. Refer to Figures 1 through 3 to convert plug.
Airtronics (A) KO Kyosho (KYO) JR/Hitec
FIGURE 1 With a small standard screwdriver, press on
each of the three metal prongs until the wires are easy to
remove. Remove wires.
FIGURE 2 With the screwdriver, carefully lift up each of
the metal locking tabs to the angle shown.
FIGURE 3 Insert each pin into the correct plug slot. Each
pin should "click" into place.
(Airtronics plug shown)
WHT = White wire terminal (signal)
BLK = Black wire terminal (negative)
RED = Red wire terminal (positive)
CAUTION Improper installation or shortening of these wires
may cause damage to the receiver, servo, and speed control.
STEP 1
CHANGING THE INPUT PLUG
The locking tab must not extend
outside the plastic plug housing.
B
C
D
E
F
G
H
I
Part #1760
red wire (+) (-) black wire
(+)
blue wire (-)
blue
wire
NOTE: The small
blue wire from the
ESC is for powering
a FET servo without
an external receiver
battery pack.
A