Proper gear selection, Voltage cut-off circuitry, Proper dig operation temperature monitoring – Novak Brushed Speed Control: M2 Dig Field Guide (55-1846P-1 Rev. 1.1) User Manual
Page 4: Trouble-shooting guide, Error codes
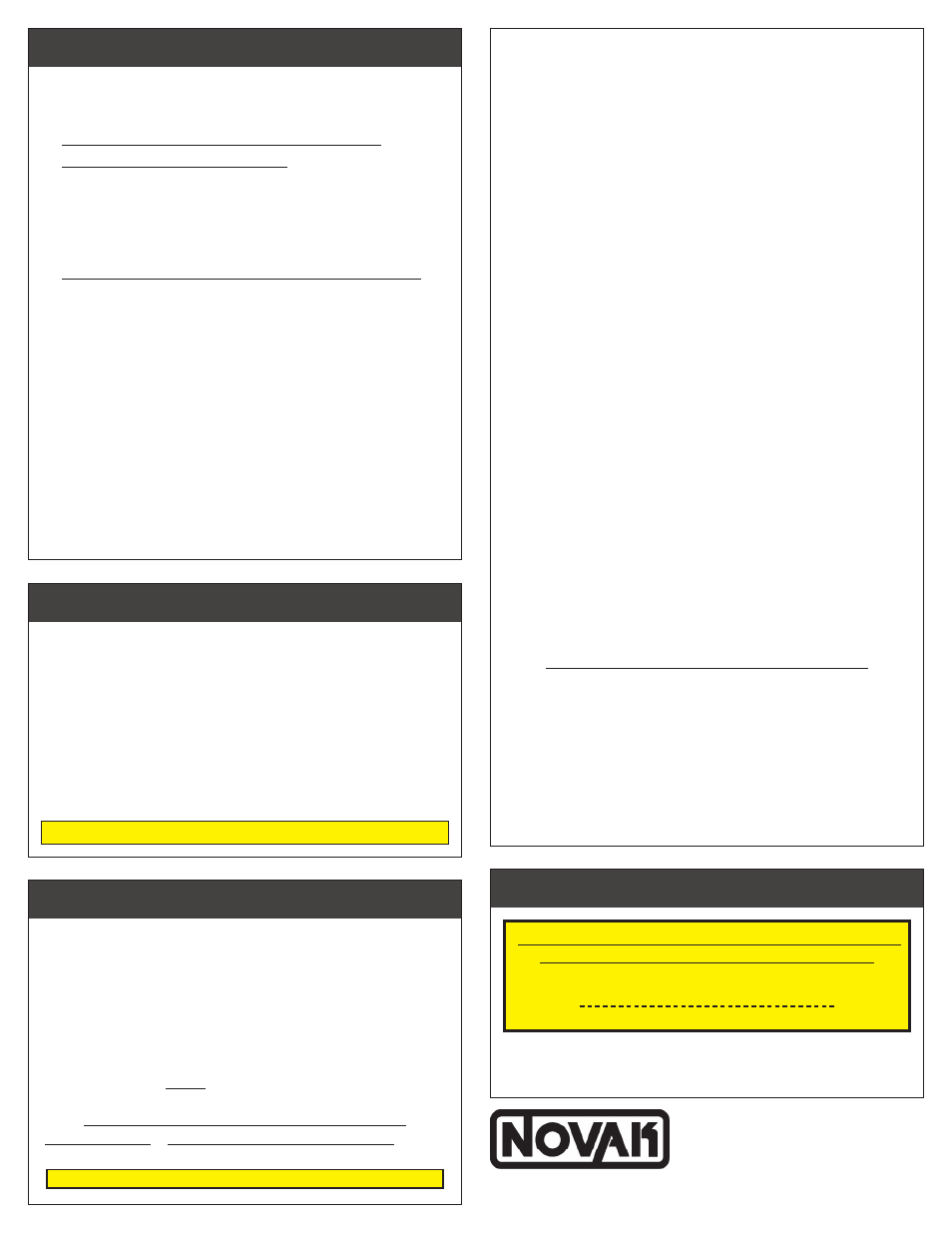
trouble-shooting guide
Steering Channel Works But motor Will Not Run
• Possible receiver damage––Check operation with a different receiver.
• Possible internal damage––Refer to ‘SERVICE PROCEDURES’ section.
• Check motor or motor connections.
• Make sure ESC is plugged into the throttle channel of receiver. Check wiring
color sequence of receiver signal harness (Refer to
STEP 1 in Basic Set-up guide).
Receiver Glitches/throttle Stutters during acceleration
• Receiver or antenna too close to ESC, power wires, battery, or motor.
• Low voltage to receiver––Try Novak Glitch Buster capacitor on receiver to help
retain power during high current draw situations (Novak accessory #5626).
• PowerCap damaged/missing––Replace PowerCap (Novak accessory #5682).
• Battery pack damaged or weak––Try a different battery pack.
• Excessive current to motor—use a milder motor or a smaller pinion gear.
• untidy wiring or signal and power wired bundled together. Input harness
and servo wires should be bundled separately from power wires. Power wires
should be as short as possible.
motor and Steering Servo do Not Work
• Check wires, receiver signal harness wiring & color sequence, radio system,
crystals, battery/motor connectors, & battery pack.
• Possible receiver damage––Check operation with a different receiver.
• Possible internal damage––Refer to Service Procedures.
motor Runs Backward
• Reverse motor rotation direction––Refer to ‘CUSTOM PROGRAMMING
OPTIONS’ section.
• Improper One-Touch set up––Refer to ‘ONE-TOUCH PROGRAMMING’ section.
Speed Control Runs excessively Hot
• Gear ratio too low––Increase ratio/Reduce pinion (refer to ‘PROPER GEAR SELECTION’).
• Motor is damaged––Try a different motor.
eSC is melted or Burnt/eSC Runs With Switch off
• Internal damage––Refer to Service Procedures.
BeC and/or Receiver Cuts out under High Steering load
• using very high-power servos––use an external BEC to power servos & receiver.
• Steering end points set too high––Reduce steering travel to prevent servo
from pulling excessive current when steering is at full lock position.
• Operating on 3S LiPo/LiFe––use an external BEC to power servos & receiver.
No Power to the BeC
• Check power wire connections to your battery, ESC, and BEC unit.
• Check that the input harness from the BEC is plugged into the receiver correctly
and the red wire from the ESC’s input harness is removed.
• Be sure that the BEC unit’s power switch is turned ON.
error codes
• Green &
red status LEDs on solid––Check input signal harness connections at
ESC and receiver. Check input signal harness wiring sequence––Refer to
STEP 1.
•
Blue & red status LEDs blinking. Possible ESC thermal shut-down––Check
gear ratio & free operation of drive train for possible overloading/ESC is being
severely over-loaded––allow system to cool & return throttle to neutral to
regain motor control.
LEDs will continue to blink until system is cooled down.
• Green &
red status LEDs blinking on and off. LiPo/LiFe Safety Cut-Off voltage
reached. Remove and charge/replace battery pack.
Check Novak’s web site for additional information.
proper gear selection
motor & eSC operating temperature is the
proper way to set the vehicle gearing
The motor and Speed Control should not exceed
160°F at any time during a run!
Change the gearing to avoid overheating.
With the extreme loads that can be encountered during Crawling, high current draw
can produce excessive speed control & motor heating. always check the operating
temperature of the ESC after initial vehicle set-up and again after making any
gearing adjustments or drive train modifications to avoid overheating.
The M2 Dig 3S speed control features Novak’s Smart-Stop Voltage Cut-
Off Circuitry built-in. When used properly, the Voltage Cut-Off circuitry
will allow you to safely use LiPo and LiFe batteries, without letting the
cells drop below their critical safety voltage.
The default in the speed control is that the Voltage Cut-Off circuitry is
turned on, and is set to the LiPo battery setting. If you are using NiMH
or NiCd cells, you will need to switch the Voltage Cut-Off circuitry to
the OFF setting. If using LiFe cells, you will need to switch the Voltage
Cut-Off circuitry to the LiFe battery setting.
Note: Whenever the speed control’s One-Touch Programming is
performed, the Voltage Cut-Off circuitry will revert back to the
default setting, which is the LiPo battery setting.
do Not uSe liPo/liFe BatteRieS WitH VoltaGe Cut-oFF tuRNed oFF
voltage cut-off circuitry
Please follow the steps below to ensure that your M2 Dig 3S speed
control is adjusted properly and that the front & rear Digs are
operating correctly:
1. TURN ON THE TRANSMITTER & ESC’S POWER
2. CONFIRM BASIC ESC FUNCTION
A. When the Transmitter’s Aux/3rd channel switch or dial is in the
center or neutral position, the ESC’s Blue & Red Dig indicator LEDs
should be OFF.
B. Apply a small amount of throttle to confirm that both front & rear
drives are functioning properly.
Both front & rear motors should
run, and should both be rotating the proper direction.
3. CONFIRM FRONT & REAR DIGS OPERATE PROPERLY
A. Position the transmitter’s Aux/3rd channel switch/dial to the left
or right end point.
B. Apply a small amount of throttle to confirm that
ONLy the front or
rear motor is running and the opposite end’s Dig is engaged. One
of the Dig indicator LEDs will illuminate. The Dig power may not
feel that strong at this point--refer to the CUSTOM PROGRAMMING
section to adjust.
C. Now position the transmitter’s Aux/3rd channel switch/dial to
the opposite end point.
D. Apply a small amount of throttle to confirm that
ONLy the opposite
motor of Step 3C is running and the other end’s Dig is engaged
(reverse of Step 3B). The other Dig indicator LED will illuminate.
The Dig feature allows you to lock one drive axle while driving the
other to let you navigate around obstacles or turn tighter as needed.
The amount of Dig Power applied to the motor that is being “locked”
is independently adjustable from the hill/Drag Brake power to give you
finer tuning and better performance than typical two speed control
installations with an auxiliary dig unit.
proper dig operation
temperature monitoring
The M2 Dig 3S ESC has a built-in diagnostic temperature monitoring
feature that lets you quickly and easily check the speed control’s operating
temperature at any time, without the need for a temperature gun.
While connected to a battery and powered ON,
simply tap the ESC’s
SET button and one of the on-board LED lights will flash 4 times to
indicate the operating temperature of the speed control.
BLUE flashing LED = normal operating temperature.
YELLOW flashing LED = medium operating temperature.
GREEN flashing LED = hot operating temperature.
RED flashing LED =
hottest operating temperature.
you are now pushing the ESC extremely hard and should be very
careful to avoid overheating and possible thermal shut-down.
All LEDs flashing = daNGeRouS operating temperature
.
your ESC is now about to thermally shut-down.
--reduce pinion size to avoid overheating and potential ESC damage--
P8
NoVaK R/C, iNC.
Lake Forest, CA 92630
(949) 916-6044; [email protected]
w w w . t e a m n o v a k . c o m