Futaba CGY750 User Manual
Page 4
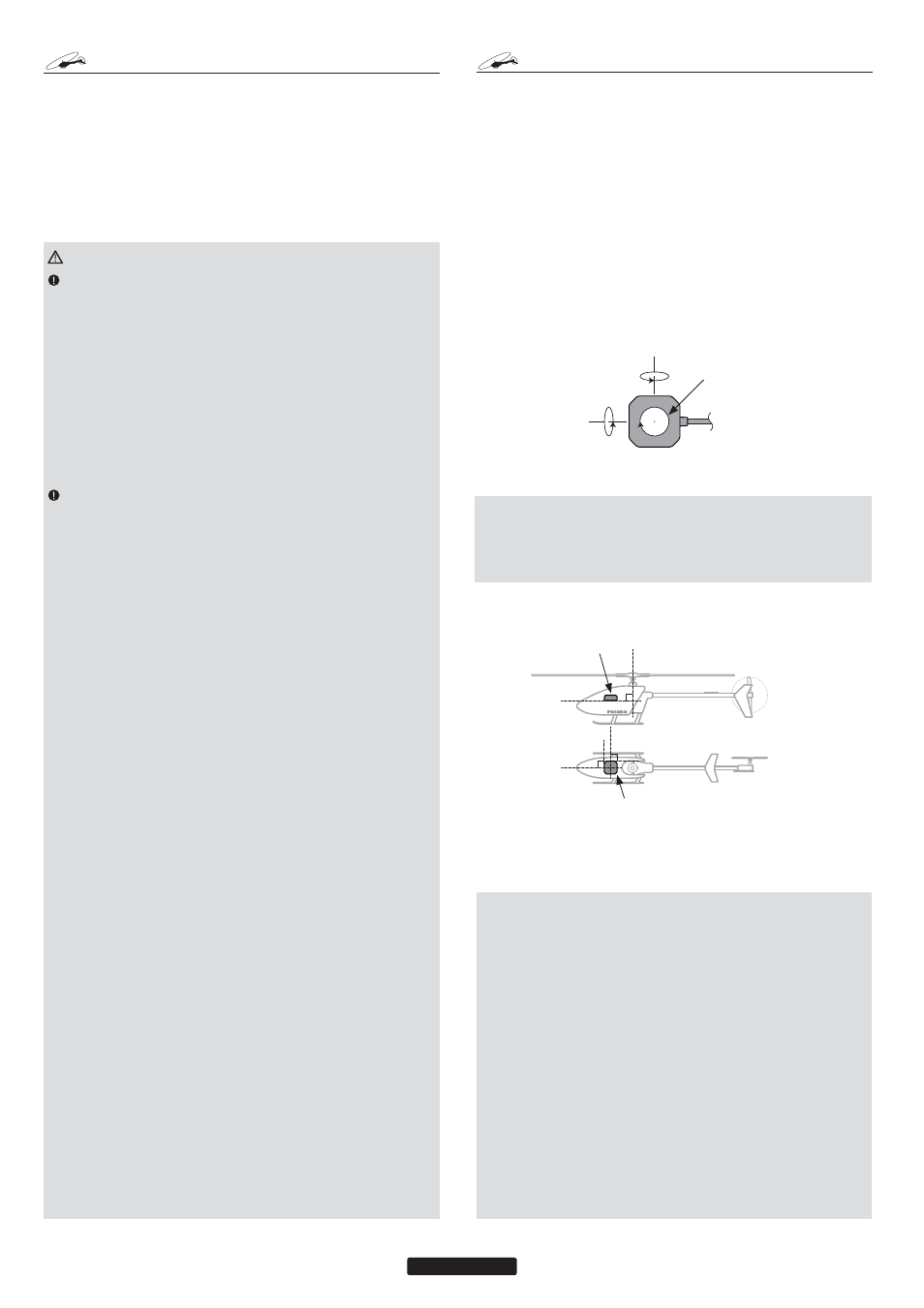
4
R
EPLACEMENT &
O
PTIONAL
I
TEMS
Futaba PC Interface CIU-2: FUTM0951
Extension 200 mm:
Extension 350 mm:
Extension 55 mm:
Extension 80 mm:
Extension 130 mm:
Mounting
Pad:
1x22x22 mm (10)
WARNING
Newer high end servos and other radio equipment
are capable of placing large demands on the power
systems in use today. When using a regulator you
must ensure that the regulator is capable of supply-
ing the current demands of the equipment you have
selected. In addition to this make sure the wiring
and switch you have selected are capable of han-
dling high current draws.
• The servo current draw can be up to 50% higher on a flybar-
less helicopter. Always ensure your receiver battery is fully
charged before each flight.
Even though the CGY750 is a high performance
gyro and governor, it will be necessary to ensure
that the helicopter mechanics are also in optimum
operating condition. Please use the guidelines be-
low and address all issues before installing and fly-
ing the CGY750.
• The CGY750 must be used with a rigid tail rotor drive system.
Any modern torque tube or belt drive system should be ad-
equate. Do not attempt to fly the CGY750 using a wire driven
tail rotor system.
• Always ensure the drive gears, torque tube, pulleys, belt,
bearings and shafts are in proper working condition. If any of
these items are damaged or worn they must be replaced.
• The linkage rod, tail rotor bell crank, pitch slider and tail rotor
grips must operate without friction to obtain the best perfor-
mance from the CGY750. Binding in the tail rotor control linkage
will decrease the performance of the CGY750 gyro and this may
also shorten the servo lifespan. Please take the time now to en-
sure the tail rotor system on your helicopter is working correctly
and without friction or binding.
• Vibration will affect the CGY750’s overall performance. All
rotating components on the helicopter should be balanced
to minimize vibrations in flight. Ensure that your engine or
electric motor is running smoothly and that all vibrations have
been addressed before installing and test flying the CGY750.
Gyro sensor replacement:
• Each CGY750 gyro control box is calibrated specifically for
the gyro sensor included. Do not attempt to use another
CGY750 sensor with the control box as performance will suf-
fer due to being out of calibration. The calibration process
must be completed by an authorized service center.
If your sensor needs replacement, please send the complete
unit to your region’s support center for repair.
7KH J\UR VHQVRU VKRXOG EH PRXQWHG RQ D ULJLG SODWIRUP DW OHDVW LQ
>PP@ DZD\ IURP D 1LWUR (QJLQH ,W LV QRW QHFHVVDU\ WR PRXQW
WKHJ\URQHDUWKHPDLQVKDIWRIWKHKHOLFRSWHUEXWLWLVYHU\LPSRUWDQW
WKDWWKHPRXQWLQJDUHDFKRVHQLVULJLG3OHDVHUHIHUWR\RXUKHOLFRSWHU
PDQXIDFWXUHU¶VLQVWUXFWLRQVIRUUHFRPPHQGHGPRXQWLQJORFDWLRQV
7HVW¿WWKHJ\URVHQVRUHQVXULQJWKDWWKHVHQVRULVLQSHUIHFWDOLJQPHQW
ZLWKWKHKHOLFRSWHURQWKHUROODQGSLWFKD[LV7KHFDEOHIURPWKHJ\UR
VHQVRUPXVWH[LWWRZDUGWKHIURQWRUWKHUHDURIWKHKHOLFRSWHUVLQFHWKLV
LVWKHSLWFKD[LV$Q\PLVDOLJQPHQWZLOOFDXVHDORVVRISHUIRUPDQFH
VRLWLVYHU\LPSRUWDQWWRHQVXUHWKDWHYHU\WKLQJLVDOLJQHGSURSHUO\
2QFH\RXDUHFHUWDLQHYHU\WKLQJLVSURSHUO\DOLJQHGDQGWKDWWKHVHQVRU
OHDG FDQ EH URXWHG WR WKH J\UR JR DKHDG DQG PRXQW WKH J\UR VHQVRU
WRWKHKHOLFRSWHUXVLQJRQHRIWKHVXSSOLHGJ\URSDGV5RXWHWKHJ\UR
VHQVRUOHDGWRWKH&*
Gyro Sensor
• Elevator (Pitch) axis
• Rudder (Yaw) axis
• Aileron (Roll)
axis
G
YRO
S
ENSOR
I
NSTALLATION
Important: The CGY750 gyro sensor must be mounted so that the
roll and pitch sensing axis are in alignment with the helicopter. Any
misalignments over 1/2 of a degree will cause a loss in performance.
Please take extra care in this step to ensure the optimum flight perfor-
mance.
TROUBLESHOOTING
If any issues are noted during flight (such as drifting, inconsistent hold
or inconsistent control rates) then please review the following trouble-
shooting recommendations.
1. Always verify that the tail rotor and swash plate mechanisms oper-
ate, and that the drive system is in proper working order.
2. Electromagnetic interference could be causing the problem. If you
feel everything is set up correctly and that the helicopter is vibration
free, then consider moving the gyro sensor to a new location away
from servos, ESC and drive motors.
3. Vibrations will decrease the performance of all gyro systems. Even
though the CGY750 gyro sensor is the most vibration resistant gyro
sensor available, eliminating vibrations will always improve perfor-
mance. Throughout extensive testing it has been found that the
CGY750 gyro sensor performs best when the sensor is mounted
rigidly to the airframe. This is mainly due to the sensing of all 3
axes. It is highly recommended to avoid using soft foam pads as
this may allow the gyro to bounce around on the roll and pitch axis,
causing instabilities and possible loss of control during flight.
• The bottom of the CGY750 Gyro
Sensor must be perpendicular to
the main shaft.
• The roll axis must be parallel to
the tail boom and the pitch axis
must be perpendicular to the side
frame.