Futaba CGY750 User Manual
Page 3
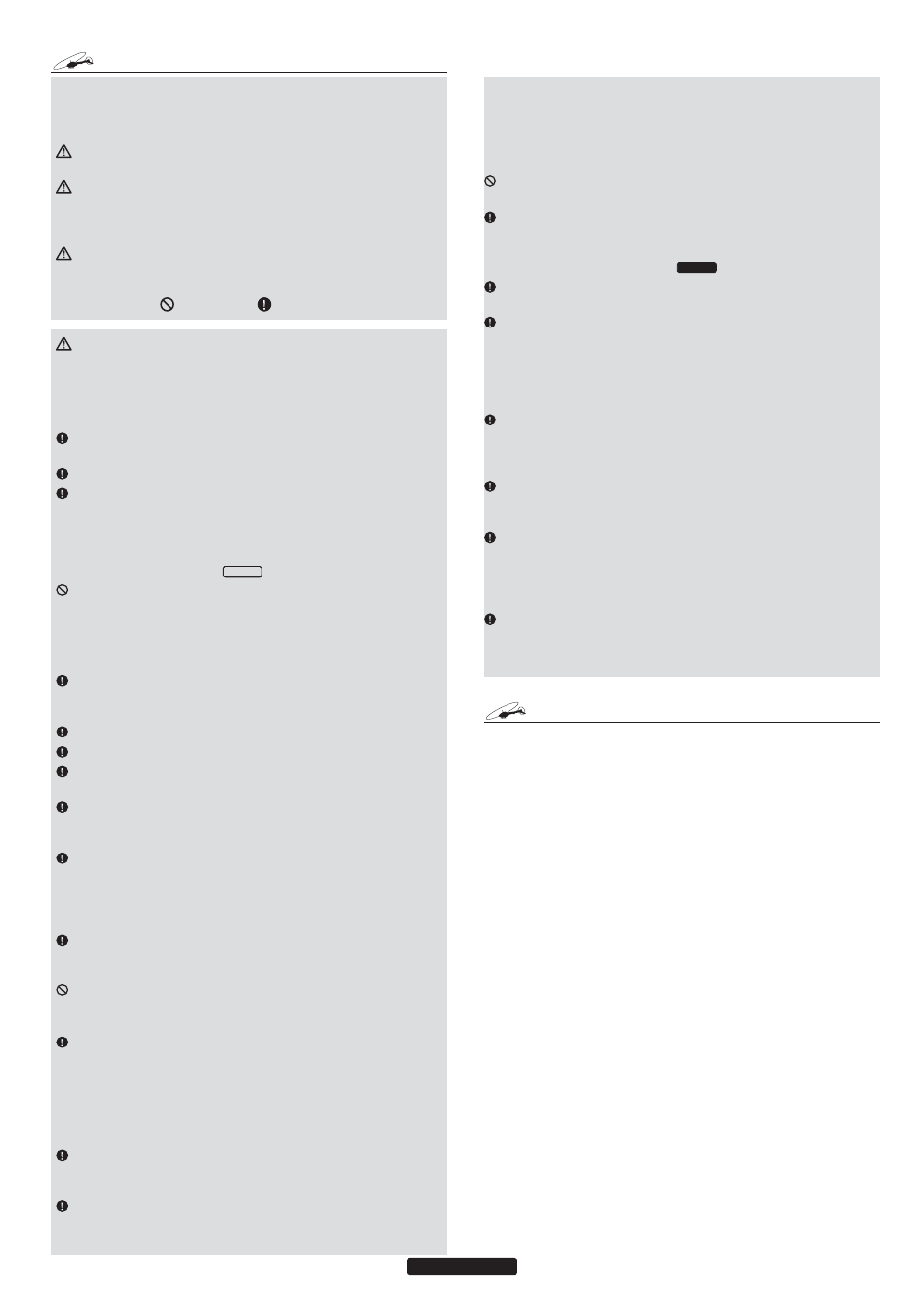
3
Meaning of Special Markings
3D\ VSHFLDO DWWHQWLRQ WR VDIHW\ ZKHUH LQGLFDWHG E\ WKH IROORZLQJ
PDUNV
DANGER
- Procedures which may lead to dangerous conditions
and cause death/serious injury if not carried out properly.
WARNING
- Procedures which may lead to a dangerous condition
or cause death or serious injury to the user if not carried out properly
or procedures where the probability of superficial injury or physical
damage is high.
CAUTION
- Procedures where the possibility of serious injury to
the user is small, but there is a danger of injury, or physical damage, if
not carried out properly.
: Prohibited
: Mandatory
WARNING
Failure to follow these safety precautions may result in severe
injury to yourself and others.
• Read through the entire manual before operating this product.
BEFORE EACH FLIGHT:
Always check the transmitter and receiver battery voltage to ensure
they have enough remaining capacity to complete the flight.
Always exit programming mode before attempting to fly the model.
Only use the CGY750 with a 2.4GHz system such as the Futaba
FASST™ system, or a PCM system. Use with an FM system is strong-
ly discouraged since interference can cause serious operational prob-
lems.
Gyro operating precautions:
Gyro
The CGY750 requires 5-10 seconds to initialize when the power
is turned on. Do not move the helicopter and do not move the tail
rotor, aileron and elevator sticks during this initialization or the
gyro may not initialize properly. Once the initialization process
has been completed the swash servos and tail servo will move
several times indicating that the CGY750 is now ready for flight.
Verify that the gyros are operating and compensating in the correct
direction before each flight. If the compensation direction is incorrect
on any axis the model will become uncontrollable after takeoff.
Verify that the gyro is operating in the desired mode.
Verify that the gyro mounting pads are in good condition.
Verify that the gyro wires are not contacting the frame of the heli-
copter.
The servo type parameters within the CGY750 must match the type
of servo you are using. Incorrect setting may damage the CGY750 or
the servos, possibly resulting in a loss of control during flight.
Always ensure that there is some slack in the gyro cables to help
maximize performance. Always use the supplied gyro mounting pads
to attach the gyro to the helicopter mechanics. Do not use a strap that
encompasses the CGY750 sensor. This may affect the overall perfor-
mance of the gyro.
Always allow the gyro to adjust to the surrounding environmental
temperature before flight. A large temperature change during use will
cause drift and other operational issues.
The gyro sensor and control box have a electroconductive coating.
Do not allow any power leads or other wiring to come into contact with
these items.
If you are switching between Normal Mode and AVCS Mode in
flight, please keep in mind that you must have the gyro re-learn the
center position after making a trim change within the transmitter.
To memorize the new center position simply flip the gain switch on
the transmitter three times between Normal Mode and AVCS Mode
(Normal
tAVCStNormaltAVCS) within one second. The servo will
center indicating that the new center position has been memorized.
When operating the gyro in AVCS Mode, all compensation and
revolution mixing must be disabled and any tail rotor or swash offsets
for flight modes must be disabled.
When the CGY750 is operated in AVCS mode the tail rotor or
swashplate servos will not center when tail rotor, aileron or rudder
stick is released. This is normal operation for AVCS mode. The servos
P
RECAUTIONS
may also move to the extent while the model is being carried out to the
flight line. Before take off, you must visually center the tail rotor pitch
slider and level the swash plate by using the transmitter control sticks.
You can also center the servos by moving the tail rotor stick full left, then
full right, back to full left and then allow the stick to center within one
second; the same method applies for aileron and elevator servos.
Do not drop the CGY750 sensor onto a hard surface or subject the
CGY750 sensor to a strong shock as this may damage the sensor.
Always use the supplied mounting pads or the Futaba replacement
mounting pads available from your local Futaba dealer.
Governor operating precautions:
Governor
When the throttle servo is connected to the CGY750, the battery fail-
safe function within the CGY750 must be setup and enabled.
Throttle fail safe function (transmitter setting): Use the fail safe func-
tion for the channel that turns the governor on and off to set the fail safe
position to the point at which the governor is turned off. With this setting,
when the system enters the fail safe state, the governor will be turned
off, and the receiver throttle signal (fail safe position preset) will be out-
put directly.
When using the condition hold function on the transmitter, always
set the throttle servo maximum operating point to less than the point at
which the governor is activated. If this is not done the governor may ac-
tivate while in condition hold.
While preparing for flight or starting the engine, always ensure the
throttle remains below the governor activation point and do not select
any flight modes that may activate the governor.
If you prefer to activate the governor while the model is still on the
ground, always ensure that you have at least -5 degrees of pitch in the
model before activating the governor. This negative pitch is necessary
to prevent an unexpected lift off as the governor activates and the head
speed increases to the desired RPM.
Periodically check the RPM sensor output to ensure proper governor
operation. Due to the high level of vibration and centrifugal forces the
magnet may come loose or the sensor alignment may change. Every
10th flight verify that the magnet and sensor are properly mounted.
Width (Controller): LQ>PP@
(Gyro sensor): LQ>PP@
(Revolution sensor): LQ>PP@
Length (Controller): LQ>PP@
(Gyro sensor): LQ>PP@
(Revolution sensor): LQ>PP@
Height (Controller): LQ>PP@
(Gyro sensor): LQ>PP@
(Revolution sensor): LQ>PP@
Weight (Controller): R]>J@
(Gyro sensor): R]>J@
(Revolution sensor): R]>J@
Operating Voltage: 9WR9'&
Current Drain: P$
Selectable Servo Frame: +]+]DQG+]
5XGGHU*\URRQO\5DWH
Center Pulse Width: 6+] +]
ȝV+]
Presets: '6SRUWV
DQG
Governor
Resolution: +]USP
(QJLQH530
RPM
Accuracy:
Head Speed Range: USP
Operating
Temperature: )WR)
&WR&
Control
System: 'LJLWDODGYDQFHGFRQWURO
Sensor: 0LFUR(OHFWURPHFKDQLFDO
6\VWHPV0(06*\UR
+DOOHIIHFWVHQVRU
Angular
Velocity
Range: 'HJUHHV3HU
6HFRQG*\UR
7KHRSHUDWLQJYROWDJHVKRZQRQO\DSSOLHVWRWKH&*<$OZD\VYHULI\WKDW
\RXUUHFHLYHUVHUYRVWDLOURWRUVHUYRVZLWFKDQGDQ\RWKHUHOHFWURQLFFRPSR-
QHQWVXVHGLQ\RXULQVWDOODWLRQDUHFDSDEOHRIRSHUDWLQJDWWKHYROWDJH\RXSODQ
WRXVH
S
PECIFICATIONS