11 grinding with the conversion kit for pin mills, Separator, Using the device – FRITSCH PULVERISETTE 14 User Manual
Page 36
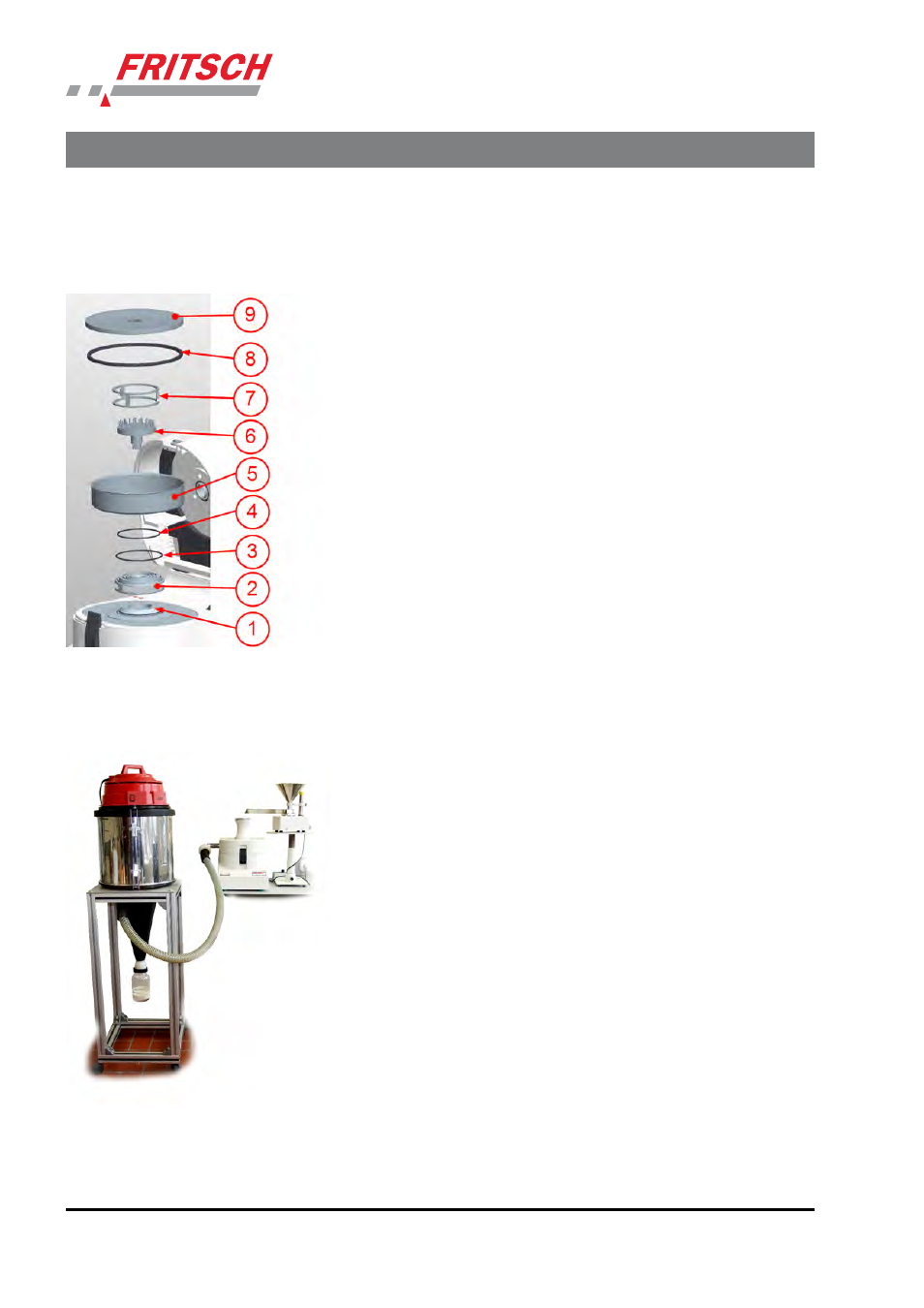
6.11 Grinding with the conversion kit for pin mills
For the article numbers, please refer to our homepage or the spare parts
catalogue.
1 Motor mounting flange
2 Labyrinth disk
3 O-ring 94x3
4 O-ring 88x3
5 Collecting vessel
6 Pin rotor
7 Spacer ring
8 Lid seal
9 Collecting vessel lid with pin insert
With this conversion kit, the rotor mill can be converted to a pin mill
without sieve. The spacer ring must be installed in order to maintain the
distance and centring between rotating and fixed pin disks.
The handling of the pin insert is the same as for the standard grinding
elements (see Ä Chapter 6.3 ‘Installing the grinding elements’
on page 27, Ä Chapter 6.5 ‘Removing the grinding elements’ on page 29
and Ä Chapter 6.4 ‘Conducting a grinding operation’ on page 28). The
sieve ring is just replaced with the spacer ring (7).
The pin mill operates best as an open system with the conversion kit for
large quantities, order no. 14.3510.00. Ä Chapter 6.6 ‘Milling with con‐
version kit for larger quantities’ on page 30
6.12 Grinding with the sample exhaust system and cyclone separator
We recommend using the vibratory feeder "LABORETTE 24" in combina-
tion with the "sample exhaust system and cyclone separator" for contin-
uous feeding of larger quantities of free-flowing grinding stock (see
Chapter 6.9 ‘Continuous feeding of source material’ on page 33.
The sample exhaust system and cyclone separator consist of:
n
Collecting vessel with outlet inserted in the PULVERISETTE 14
n
Frame for the exhaust system
n
Dust exhaust system with cyclone separator
n
Powder bottle, 500 ml
We recommend using the conversion kit:
n
when milling larger quantities.
Due to the centrifugal effect of the impact rotor and the increased
air flow rate, the source material is discharged and collected in the
sample bottle.
n
when milling temperature-sensitive source material.
The increased air flow rate cools the source material. This shortens
the milling time and also the amount of time the material spends in
the grinding chamber.
Using the device
- 36 -