Disassembly, Assembly – Viking Pump TSM141.1: G-LL 125/4125 User Manual
Page 8
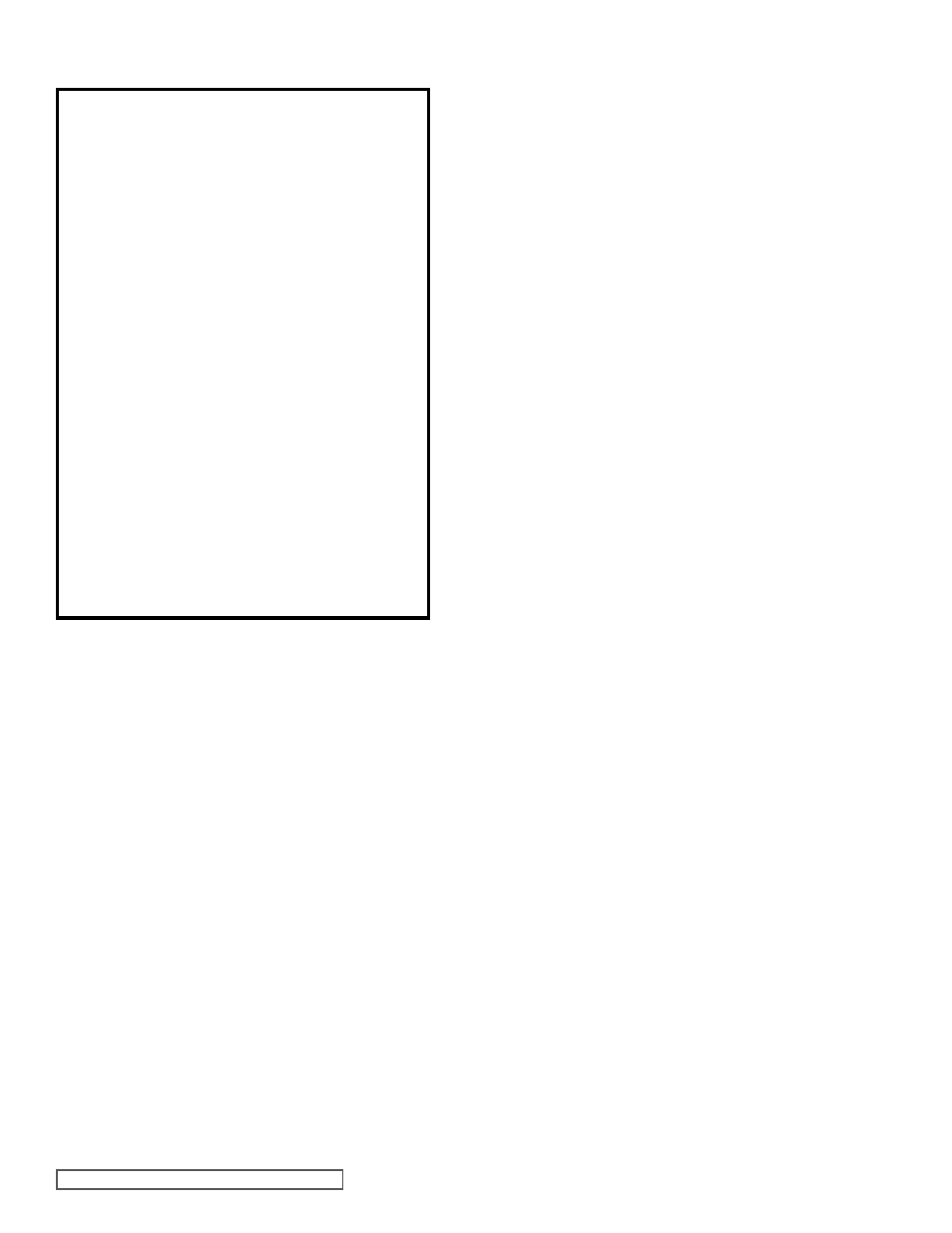
SECTION TSM 141.1
ISSUE
E
PAGE 8 OF 16
1. Mark the head position relative to the casing before
disassembly to ensure proper reassembly. The idler pin,
which is offset in the pump head, must be positioned
toward and equal distance between the port connections
to allow for proper flow of liquid through the pump.
Tilt the top of the head back when removing the head
to prevent the idler from falling. Remove the head from
the pump. Avoid damaging the head gasket. If the pump
is furnished with a pressure relief valve, it need not be
removed from the head or disassembled at this point.
Refer to Pressure Relief Valve Instructions, page 15.
If the pump has a jacketed head plate, it will separate
from the head when it is removed. The gasket between
the head and the jacket head plate must be totally
removed.
Always use a new gasket when assembling
the pump.
2. Remove
the idler and bushing assembly.
3. Insert a length of hardwood or brass through the port
opening between the rotor teeth to keep the shaft
from turning. Bend up the tang of the lockwasher
and with a spanner wrench remove the locknut and
lockwasher from the shaft. There is no lockwasher on
G size pumps.
4. Tap
the shaft forward approximately 0.5 inch and remove
the pair of half round rings under the inner spacer collar.
There is no pair of half round rings on G, H and HL size
pumps.
DISASSEMBLY
DANgER !
Before opening any Viking pump liquid
chamber (pumping chamber, reservoir,
relief valve adjusting cap fitting, etc.)
Be sure:
1. That any pressure in the chamber has
been completely vented through the
suction or discharge lines or other
appropriate openings or connections.
2. That the driving means (motor,
turbine, engine, etc.) has been “locked
out” or made non-operational so that
it cannot be started while work is
being done on pump.
3. That you know what liquid the
pump has been handling and the
precautions necessary to safely
handle the liquid. Obtain a material
safety data sheet (MSDS) for the
liquid to be sure these precautions
are understood.
Failure to follow above listed
precautionary measures may result in
serious injury or death.
ASSEMBLY
Standard Mechanical Seal
(Synthetic Rubber Bellows Type)
Sizes g, H, HL, K, KK, L, LQ and LL
5. Carefully remove the rotor and shaft to avoid damaging
the bracket bushing.
6. Remove the rotary member of the seal from the shaft
and the stationary seal seat from the bracket.
7.
Loosen the setscrews. Two on G, H and HL size pumps,
four for all other sizes. With a spanner wrench, remove
both end caps and lip seals. Remove the ball bearing
and spacer collars.
Refer to Figure 6, page 5.
8.
Examine the seal chamber lip seal and remove if it
shows wear or damage. The lip seal must be removed if
the bracket bushing needs to be replaced.
9. Clean all parts thoroughly and examine for wear or
damage. Check the lip seals, ball bearing, bushing and
idler pin and replace if necessary. Check all other parts for
nicks, burrs, excessive wear and replace if necessary.
Wash
the bearings in clean solvent. Blow out the
bearings with compressed air. Do not allow the bearings
to spin; turn them slowly by hand. Spinning the bearings
will damage the race and balls. Make sure the bearings
are clean, then lubricate with non-detergent SAE 30
weight oil and check for roughness. Roughness can be
determined by turning the outer race by hand.
Be sure the shaft is free from nicks, burrs and foreign
particles that might damage the bracket bushing.
Scratches on the shaft in the seal area will provide
leakage paths under the mechanical seal.
10.
Casing can be checked for wear or damage while
mounted on the bracket.
The seal used in this pump is simple to install and good
performance will result if care is taken during installation.
The principle of the mechanical seal is contact between the
rotary and stationary members. These parts are lapped to
a high finish and their sealing effectiveness depends on
complete contact.
Viking furnishes a number of heavy-duty pumps with special
mechanical seals installed in the packing end of the pump.
These special seals are not discussed in this manual
(TSM141.1). Information is available by contacting the factory.
When requesting special seal information, be sure to give the
pump model number and serial number.
1. Install
the bracket bushing. If the bracket bushing has
a lubrication groove, install the bushing with the groove
at the 12:00 o’clock position in the bracket. If replacing
carbon graphite bushings,
Refer to Installation of
Carbon graphite Bushings, page 14.
2. Install the lip seal in the bracket. Refer to Figure 8,
page 9.