Tweco Maximizer 300 Torch for BNFL User Manual
Page 28
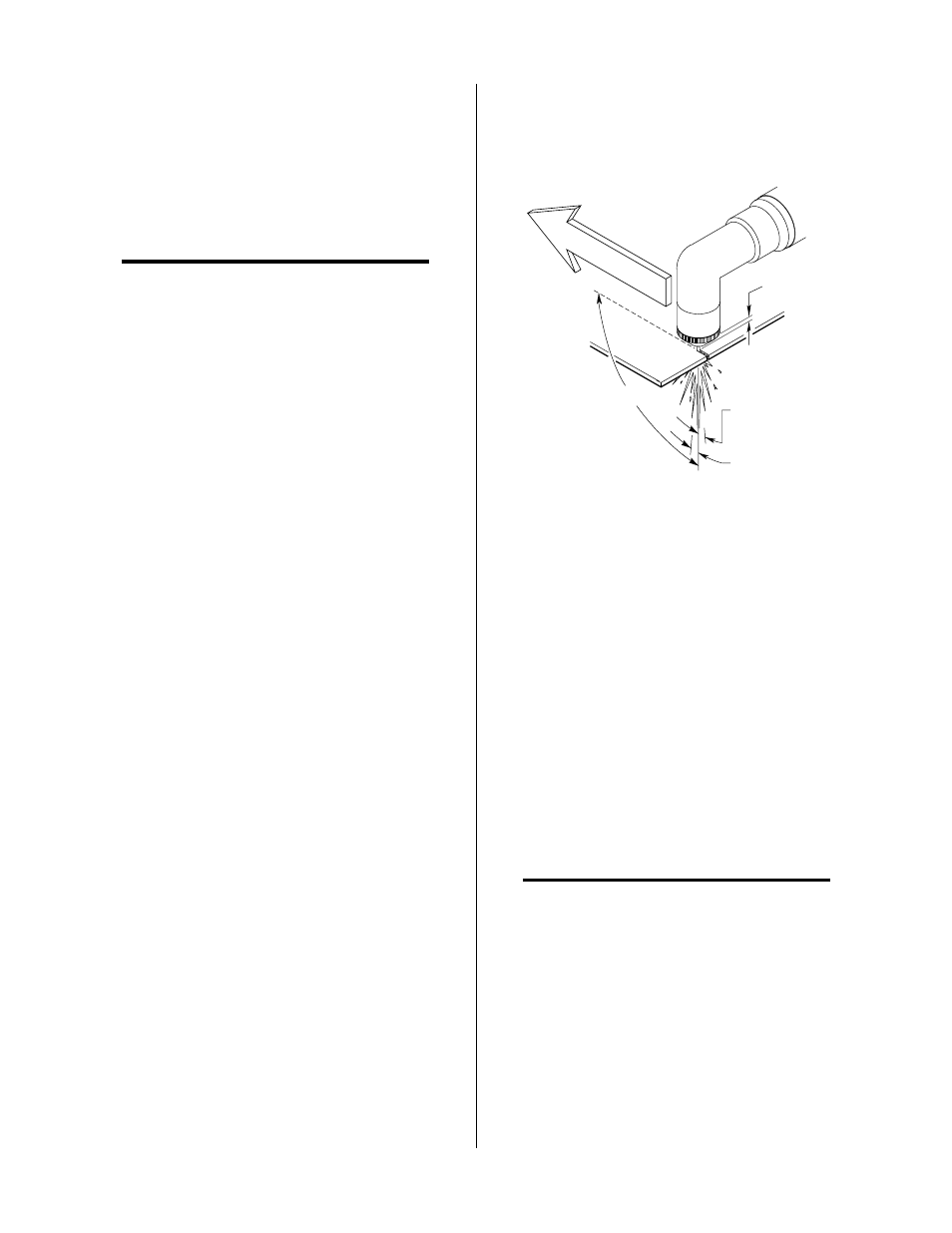
OPERATION
4-6
Manual 0-2990
4. With the pilot arc on, the main cutting arc will be
established when the torch is brought within 1/8
- 3/8 in (3 - 10 mm) of the workpiece. If the cut-
ting arc is interrupted and the torch is still acti-
vated, as when cutting expanded metal, the pilot
arc will automatically restart (see NOTE). Deac-
tivating the torch will shut off either the pilot or
main arc, depending on the mode of operation.
NOTES
Pilot arc will automatically restart in AIR, N2 or
Ar/H2 PLASMA Modes, if AUTO-RESTART
function is enabled in the Power Supply.
AUTO-RESTART is always disabled in O
2
Mode.
The AUTO-RESTART is factory set to disable.
Refer to Auto-Restart function in the Power Sup-
ply Operating Manual.
5. Cut with a standoff of 1/8 - 3/8 in (3 - 10 mm)
from the work. The torch should be held perpen-
dicular to the workpiece while cutting. Start cut-
ting slowly and adjust cutting speed for optimum
cutting performance. Refer to Section 4.08, Rec-
ommended Cutting Speeds, for typical cutting
speeds for various materials and material thick-
nesses.
B. Travel Speed
Proper travel speed is indicated by the trail of the arc
which is seen below the plate. The arc can be one of
the following:
1. Straight Arc
A straight arc is perpendicular to the workpiece
surface. This arc is generally recommended for
the best cut using air plasma on stainless or alu-
minum.
2. Leading Arc
The leading arc is directed in the same direction
as torch travel. A five degree leading arc is gener-
ally recommended for air plasma on mild steel.
3. Trailing Arc
The trailing arc is directed in the opposite direc-
tion as torch travel.
A-01987
Standoff
Distance
Straight Arc
Trailing Arc
Leading Arc
Direction of Torch Travel
Figure 4-6 Machine Torch Operation
The arc characteristics vary with gases used, cutting
speed, material, and thickness. Air plasma normally
produces a straight arc (on stainless or aluminum),
while nitrogen plasma generally creates a 5° trailing
arc.
For optimum smooth surface quality, the travel speed
should be adjusted so that only the leading edge of
the arc column produces the cut. If the travel speed
is too slow, a rough cut will be produced as the arc
moves from side to side in search of metal for trans-
fer.
Travel speed also affects the bevel angle of a cut.
When cutting in a circle or around a corner, slowing
down the travel speed will result in a squarer cut.
The power source output should be reduced also.
NOTE
Refer to the Power Supply Operating Manual for
any Corner Slowdown (CSD) adjustments that
may be required.