Troubleshooting guide, Reduced pressure zone assemblies – Watts TK-DL User Manual
Page 7
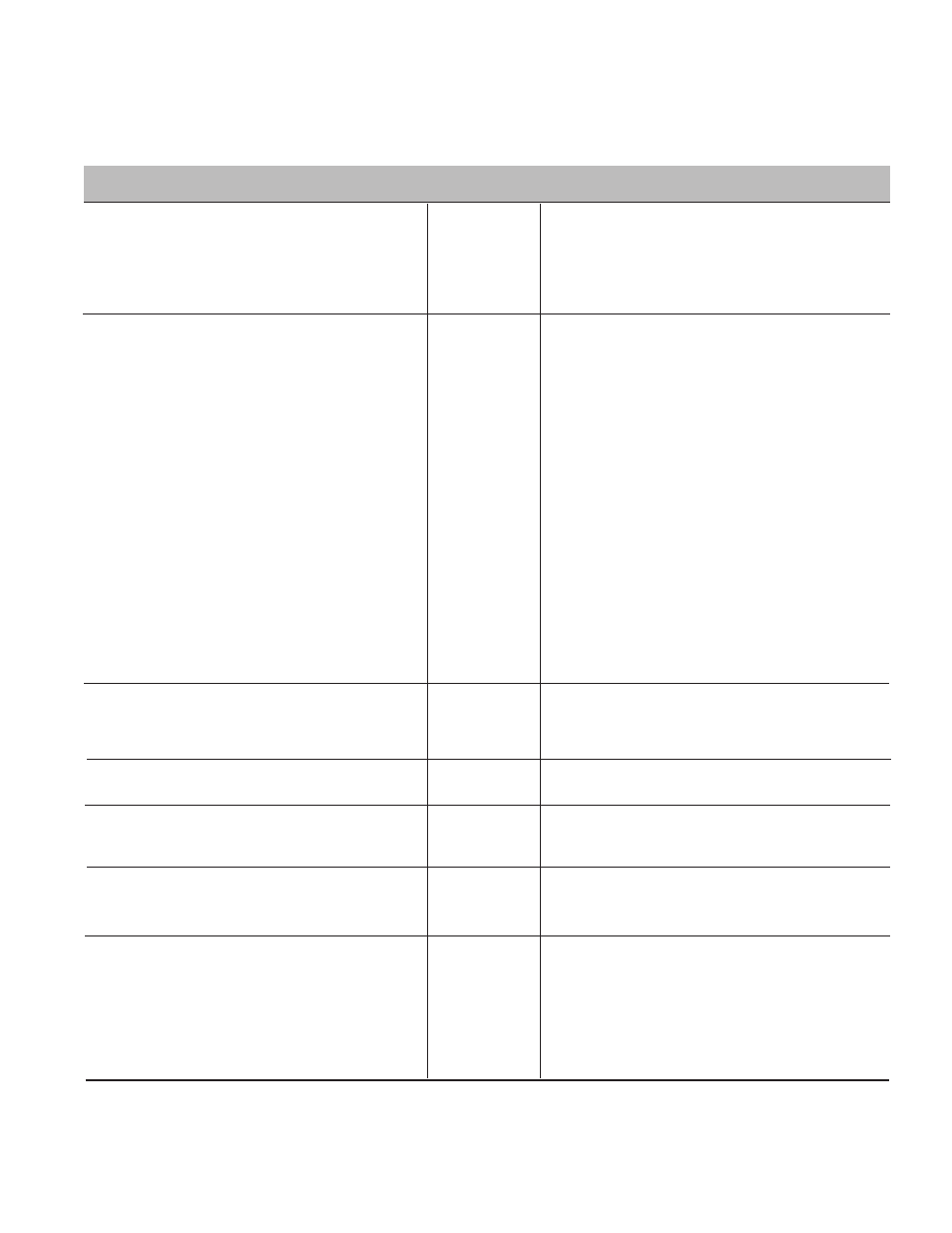
7
Should valve
PROBLEM
CAUSE
be replaced?
SOLUTION
A. Valve spits periodically from the vent.
A.1 Fluctuating supply pressure.
No
A.1 Install a soft seated check valve immediately upstream
of the device. (Watts 3/4”- 2” No. 601 bronze valve.)
A.2 Fluctuating downstream pressure.
No
A.2 Install a soft seated check valve downstream of the
device close as possible to the shutoff valve.
(Watts 3/4”- 2” No. 601 bronze valve.)
B. Valve drips continually from the vent.
B.1 Fouled first check.
No
B.1 Flush valve. If flushing does not resolve problem,
disassemble valve and clean or replace the first check.
B.2 Damaged or fouled relief valve seat.
No
B.2 Clean or replace the relief valve seat.
B.3 Relief valve piston “O” ring not free to move due to
No
B.3 Clean, grease or replace the piston “O” ring.
pipe scale, dirt or build-up of mineral deposits.
B.4 Excessive backpressure, freezing, or water hammer
No
B.4 Eliminate source of excessive backpressure or water
has distorted the second check.
hammer in the system downstream of the device. Use
Watts No. 601 to dampen out backpressure and No. 15
to eliminate water hammer. Replace defective second
check assembly. In case of freezing; thaw,
disassemble, and inspect internal components.
Replace as necessary.
B.5 Electrolysis of relief valve seat or first check seats.
No
B.5 Replace relief valve seat or inlet cover. Install dielectric
unions (Watts Series 3001 through 3006). Electrically
ground the piping system and/or electrically isolate the
device with plastic pipe immediately upstream and
downstream of the device.
B.6 Valve improperly reassembled.
No
B.6 If valve is diassembled during installation, caution must
be exercised to install check springs in
their proper location.
C. Valve exhibits high pressure drop.
C.1 Fouled strainer.
No
C.1 Clean strainer element or replace.
C.2 Valve too small for flows encountered.
Yes
C.2 Install proper size device based upon flow
requirements.
D. No water flows downstream of valve.
D. Valve installed backwards.
No
D. Install valve in accordance with flow direction arrow.
E. Valve does not test properly.
E.1 Follow manufacturer’s test procedure.
No
E.1, E.2 Clean or replace gate valve with full port ball
E.2 Leaky downstream gate valve.
No
valves or resilient wedge shutoff valves.
F. Valve quickly and repeatedly fouls following servicing.
F. Debris in pipe line is too fine to be trapped by strainer.
No
F. Install finer mesh strainer element in the strainer.
G. Winterization of backflow preventers.
G. Electric heat-tape wrap closely together around valve
body. Build a small shelter around the valve with a
large light bulb installed and left on at all times.
If supply line is not used during the winter, removal
of the complete body is the best. This would create
an air gap to eliminate any possible backflow.
Troubleshooting Guide
Reduced Pressure Zone Assemblies