Rockwell Automation FlexPak Plus DC Drive User Manual
Page 15
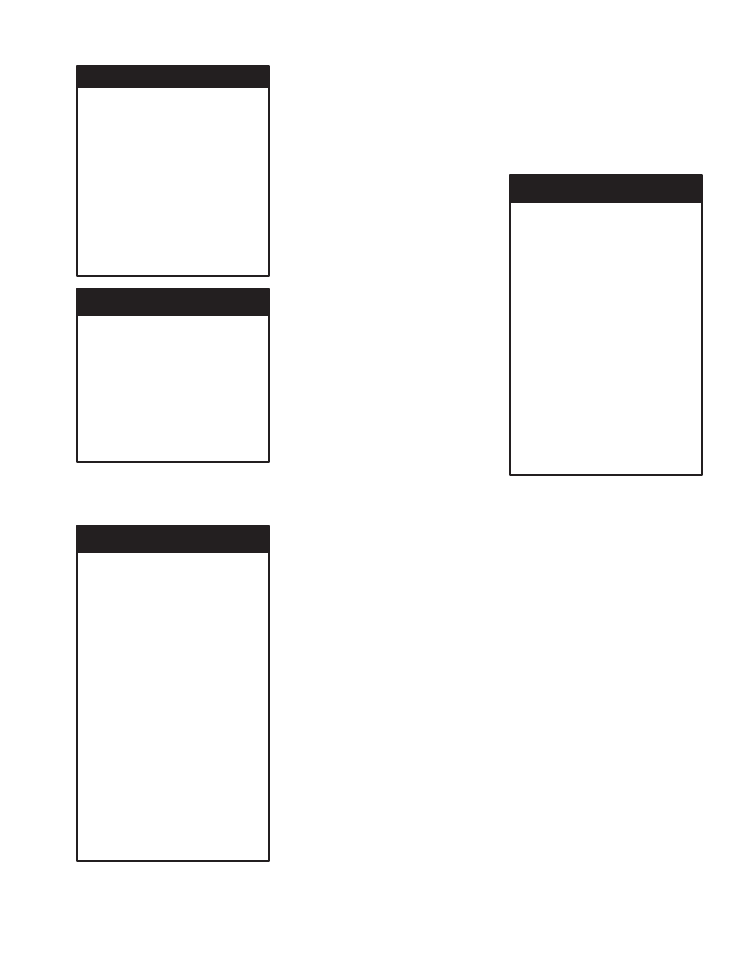
3:5
DANGER
THE USER IS RESPONSIBLE
FOR CONFORMING TO THE
NEC AND ALL OTHER APPLIĆ
CABLE LOCAL CODES WITH
RESPECT TO WIRING PRACĆ
TICES, GROUNDING, DISĆ
CONNECTS AND OVERCURĆ
RENT PROTECTION ARE OF
PARTICULAR IMPORTANCE.
FAILURE TO OBSERVE THIS
PRECAUTION COULD REĆ
SULT IN SEVERE BODILY
INJURY OR LOSS OF LIFE.
DANGER
THIS EQUIPMENT IS AT LINE
VOLTAGE WHEN AĆC POWER
IS CONNECTED.
DISCONĆ
NECT AND LOCKOUT ALL
UNGROUNDED
CONDUCĆ
TORS OF THE AĆC POWER
LINE. FAILURE TO OBSERVE
THESE PRECAUTIONS COULD
RESULT IN SEVERE BODILY
INJURY OR LOSS OF LIFE.
Ground the Controller and
Enclosure, the Motor and the
Operator's Control Station.
DANGER
CONNECT
THE
GROUND
WIRE BROUGHT IN WITH THE
INCOMING AĆC POWER LINE
TO
THE
CONTROLLER
GROUND POINT. CONNECT
AN APPROPRIATE EQUIPĆ
MENT GROUNDING CONDUCĆ
TOR UNBROKEN FROM THE
THE CONTROLLER GROUND
POINT, THE MOTOR FRAME,
THE TRANSFORMER ENCLOĆ
SURE IF USED, THE CONĆ
TROLLER ELECTRICAL ENĆ
CLOSURE, THE WIRING CONĆ
DUITS, AND THE OPERAĆ
TOR'S CONTROL STATION TO
AN APPROPRIATE GROUNDĆ
ING ELECTRODE. FAILURE
TO OBSERVE THESE PREĆ
CAUTIONS COULD RESULT IN
SEVERE BODILY INJURY OR
LOSS OF LIFE.
1. Locate the Controller ground
point provided.
2. Run a suitable equipment
grounding conductor unbroken
from the Controller ground point
(see step 1) to the plant ground
(grounding electrode). A ring
lug is recommended at the
ground point.
3. Connect a suitable grounding
conductor from each conduit to
this controller ground point.
4. Connect a suitable equipment
grounding conductor to the
motor frame, the transformer
enclosure if used, and the
controller enclosure. Run this
conductor unbroken to the
grounding electrode.
5. Connect the GND
(green/ground) wire brought in
with the incoming AĆC power line
to the controller ground point.
General Wiring Practices
The Controller is designed for AĆC
and DĆC power entry at the top and
control and signal wiring to enter
from the sides or bottom.
Reference signal wiring should be
run in a separate conduit isolated
from all AĆC and DĆC power and
control. All reference signals should
be wired with either twisted double
or twisted triple conductor wire, 2
twists per inch, stranded copper,
AWG No. 16, 600 VAC rated,
polyĆvinyl chloride insulation, with a
temperature range of 40 - 105_C
(104 - 221_F). Signal wires should
not be run in parallel with high
voltage or electrically noisy
conductors. Always cross such
conductors at 90_.
Tachometer Feedback, Instrument
Interface and Voltage/Tachometer
Follower signal wiring should be run
in a separate conduit isolated from
all AĆC and DĆC power and logic
control. Wiring should be the same
as for the reference signals above.
For mounting with external
contactors and solenoids, coils
should be suppressed to reduce
noise.
Wire AĆC Power to the
Controller
DANGER
THE DRIVE REQUIRES A
SINGLEĆPHASE
POWER
SOURCE OF EITHER 115 VAC
OR 230 VAC, 50 OR 60 HZ. IF
THE CORRECT VOLTAGE IS
NOT AVAILABLE, A TRANSĆ
FORMER
MUST
BE
INĆ
STALLED
BETWEEN
THE
POWER SOURCE AND THE
DRIVE. DO NOT OPERATE
THE
CONTROLLER
WITH
AVAILABLE SHORT CIRCUIT
CURRENTS IN EXCESS OF
5000 AMPERES. FAILURE TO
OBSERVE THESE PRECAUĆ
TIONS COULD RESULT IN
SEVERE BODILY INJURY OR
LOSS OF LIFE.
1. Size the AĆC line supply
conductors for the specific
controller rating and according
to all applicable codes.
2. Run the AĆC line supply to fuses
L1 and L2 at the top of the
Controller if an optional auxiliary
panel is used.
Power Transformation
Although auto transformers may
step up or down the AĆC power
supply voltage, they do not isolate
the Drive from the AĆC line. Users
should consider using an isolation
transformer in lieu of an auto
transformer for the following
advantages:
D Should a person come in
contact with the AĆC incoming
line, an isolation transformer
would reduce the risk of severe
or fatal injury.
D AĆC power line disturbances and
transients are minimized by an