Build and install the cables, Ground shielded signal wires within a power cable – Rockwell Automation MPL-xxxx Low Inertia Servo Motor 215 mm or Larger User Manual
Page 7
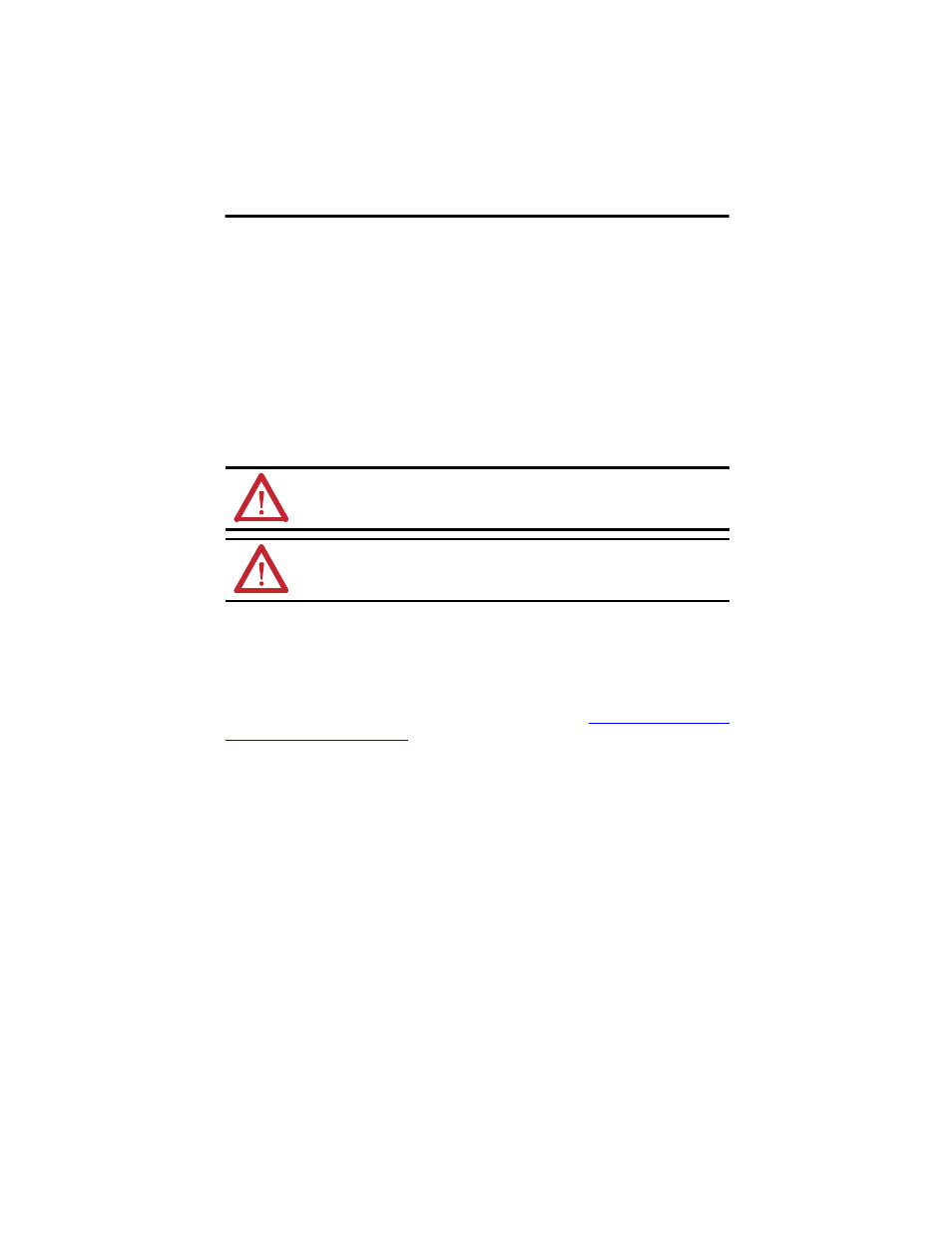
MP-Series Low-inertia Servo Motor with 215 mm or Larger Frame Size 7
Rockwell Automation Publication MP-IN002D-EN-P - January
Build and Install the Cables
Correct cable routing and careful cable construction improves system electromagnetic
compatibility (EMC).
Follow these guidelines to build and install the cables:
•
Keep the wire lengths as short as possible.
•
Route noise sensitive wiring (encoder, serial, and I/O) away from input power and motor
power wiring.
•
Separate cables by 0.3 m (1 ft) minimum for every 9 m (30 ft) of parallel run.
•
Ground both ends of the encoder cable shield and twist the signal wire pairs to prevent
EMI from other equipment.
Ground Shielded Signal Wires within a Power Cable
Always connect the shield on any signal wire pair routed inside a power cable to the overall
machine ground.
If you are installing a 2090-XXNPMF-
xxSxx or 2090-CPBM4DF-xxAFxx power with brake
cable, loop the signal wire pairs to the overall cable shield as shown in
Grounding of Signal Wire
Shields in a Power Cable on page 8
. Then clamp all of the shields together in the power cable
(chassis) ground connection on the drive.
ATTENTION: High voltage can be present on the shield of a power cable, if the shield is not grounded.
Verify that there is a connection to ground for any power cable shield.
ATTENTION: MP-Series motors produce leakage current in the protective earthing conductor that exceeds
3.5 mA AC and/or 10 mA DC.
Be sure to properly ground the motor cables per the drive installation instructions.