Drive startup / tuning, Reading additional signals from powerflex 700s – Rockwell Automation 9329 Drive Application Software Positioning Point to Point User Manual
Page 9
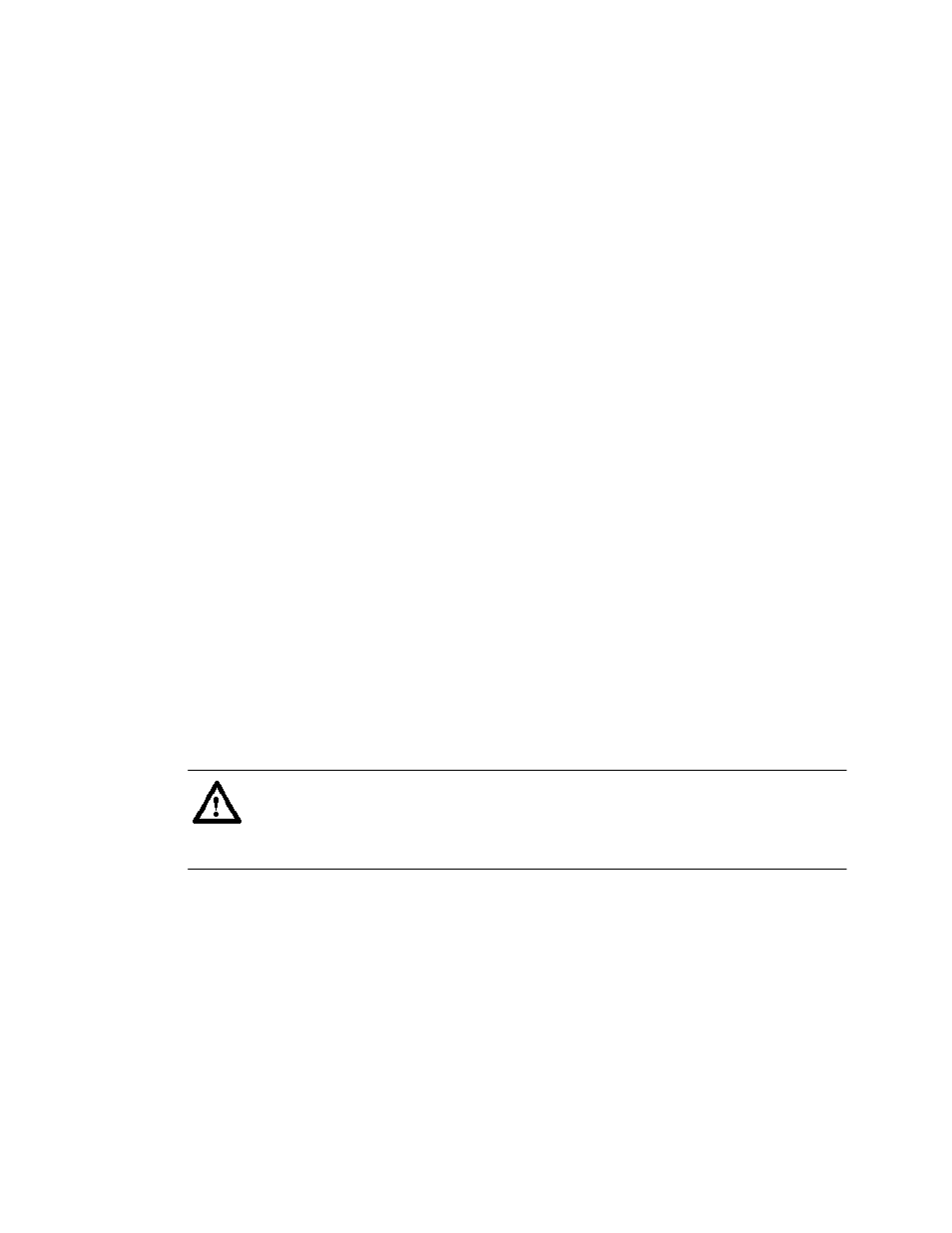
Quick Start – Positioning (Pt to Pt)
Drive Application Software – page 9 of 10
Drive Startup / Tuning
For basic commissioning of the application, the drive must first be tuned to regulate the
motor. The following steps will guide you through the basic requirements of drive tuning
when using an application module.
1. Set param 153 bit 8 high. This will set the start/stop control to 3 wire for
operation via the HIM. When the start up is complete this must be set to low for
2 wire operation from DriveLogix.
2. From the HIM, select the “Start-Up” function and follow the directions. In this
section you will perform the following steps.
a. Motor Control
i. FOC – for Induction Motor
ii. PMag – for Permanent Magnet Motor
b. Motor Data – Enter all motor data for the attached motor, check # poles
c. Feedback Config – Select feedback type
d. Pwr Circuit Diag
e. Direction Test – (NOTE, the motor will run) recommend always changing
wires and not software, this is for maintenance purposes, if the program
is restored it will default to the standard direction setting.
f. Motor Tests – (NOTE, the motor will run)
g. Inertia Measure – (NOTE, the motor will run)
h. Speed Limits
i. Select “+/- Speed Ref”
ii. Fwd Speed Limit
iii. Rev Speed Limit
iv. Abs Overspd Lim – Max over speed past the Fwd and Rev
Speed Limit. This is where the drive will fault.
i. Do not complete the remainder of the Start-Up procedure in the
drive.
j. Scroll down to “Done/Exit”
3. Tune the speed regulator. Depending on the inertia of the machine and other
factors, the speed regulator bandwidth (param 90) should be set for 10 to 100
radians.
4. Adjust the position regulators Kp gain (param 768) to 1/5 of the speed regulators
bandwidth. Example: If p90 = 50 then set p768 = 50/5 = 10
5. Set param 153 bit 8 Low. This will set the start/stop control to 2 wire for
operation via DriveLogix.
ATTENTION: Parameter 153 bit 8 must be set low for operation from the DriveLogix
controller. If the control selection of 2 wire (NOT 3 Wire Control) is not made the
drive will fail to stop when the run command is removed. 2 wire control is the
intended and designed configuration for the PowerFlex 700S drive when operated
from a controller such as DriveLogix
6. The drive is ready for control from DriveLogix and the rest of the commissioning
and tuning may be completed.
Reading additional signals from PowerFlex 700S
Reading of additional signals from the PowerFlex 700S can be accomplished through the
Peer Communications setup in the drive. Do not change any defined links, as this will
break the application module. In the Positioning (Pt to Pt) application there are available 5
undefined REAL data connections. In DriveExecutive access the “Peer Communication
Setup” under “Drive” / “Peer Communication…”. Select the tab “To Controller” and edit the
undefined links as needed. These are Real data links only. Parameters with data types
other than real cannot be connected at these points. The data will be sent to DriveLogix and
available at tags ( Drive:I.UserDefinedRealData[2] – [6] ). If additional data is required,
messaging must be employed. Contact Local Drives Solutions or SupportPlus for assistance.