Chapter 7, Preventative maintenance, Periodic maintenance – Rockwell Automation 1395 Digital Reference Adapter for RTP Applications User Manual
Page 41
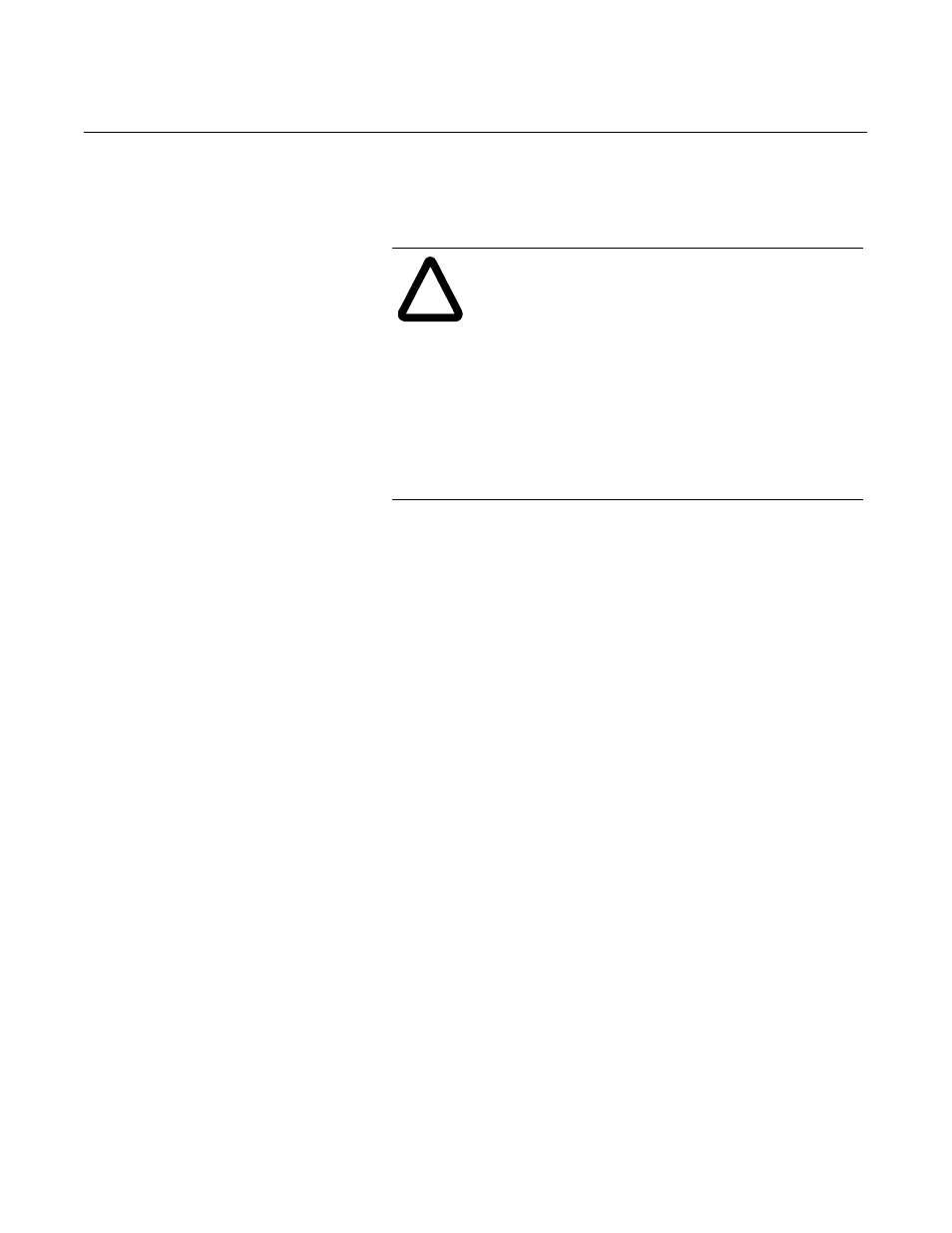
Publication 1395-RTP-5.2 - September 1997
Chapter
7
Periodic Maintenance
Preventative Maintenance
Periodic Inspection – Industrial control equipment should be
inspected periodically. Inspection intervals should be based on
environmental and operating conditions, and adjusted as indicated by
experience. An initial inspection within 3 to 4 months after
installation is suggested. Applicable parts of the following guidelines
should be used:
Contamination – If inspection reveals that dust, dirt, moisture or
other contamination has reached the control equipment, the cause
must be eliminated. This could indicate an incorrect or ineffective
enclosure, unsealed enclosure openings (conduit or other) or incorrect
operating procedures. Dirty, wet or contaminated parts must be
replaced unless they can be cleaned effectively by vacuuming or
wiping.
Terminals – Loose connections can cause overheating that can lead
to equipment malfunction. Check the tightness of all terminals and
bus bar connections and securely tighten any loose connections.
Replace any parts or wiring damaged by overheating.
Solid State Devices – Solid state devices require little more than a
periodic virtual inspection. Printed circuit boards should be inspected
to determine whether all ribbon cables are properly seated in their
connectors. Board locking tabs should also be in place. Necessary
replacements should be made only at the PC board or plug-in
component level. Solvents should not be used on printed circuit
boards. Where blowers are used, air filters if supplied should be
cleaned or changed periodically depending on the specific
environmental conditions encountered. For additional information see
NEMA Standards Publication No. ICS 1.1-1984 entitled: “Safety
!
ATTENTION: Servicing energized industrial control
equipment can be hazardous. Severe injury or death can
result from electrical shock, burn, or unintended
actuation of controlled equipment.
Recommended practice is to disconnect and lock out
control equipment from power sources, and allow
stored energy in capacitors to dissipate, if present. If it
is necessary to work in the vicinity of energized
equipment, the safety related work practices of NFPA
70E, Electrical Safety Requirements for Employee
Workplaces, must be followed.