USG Securock Glass-Mat Sheathing User Manual
Page 3
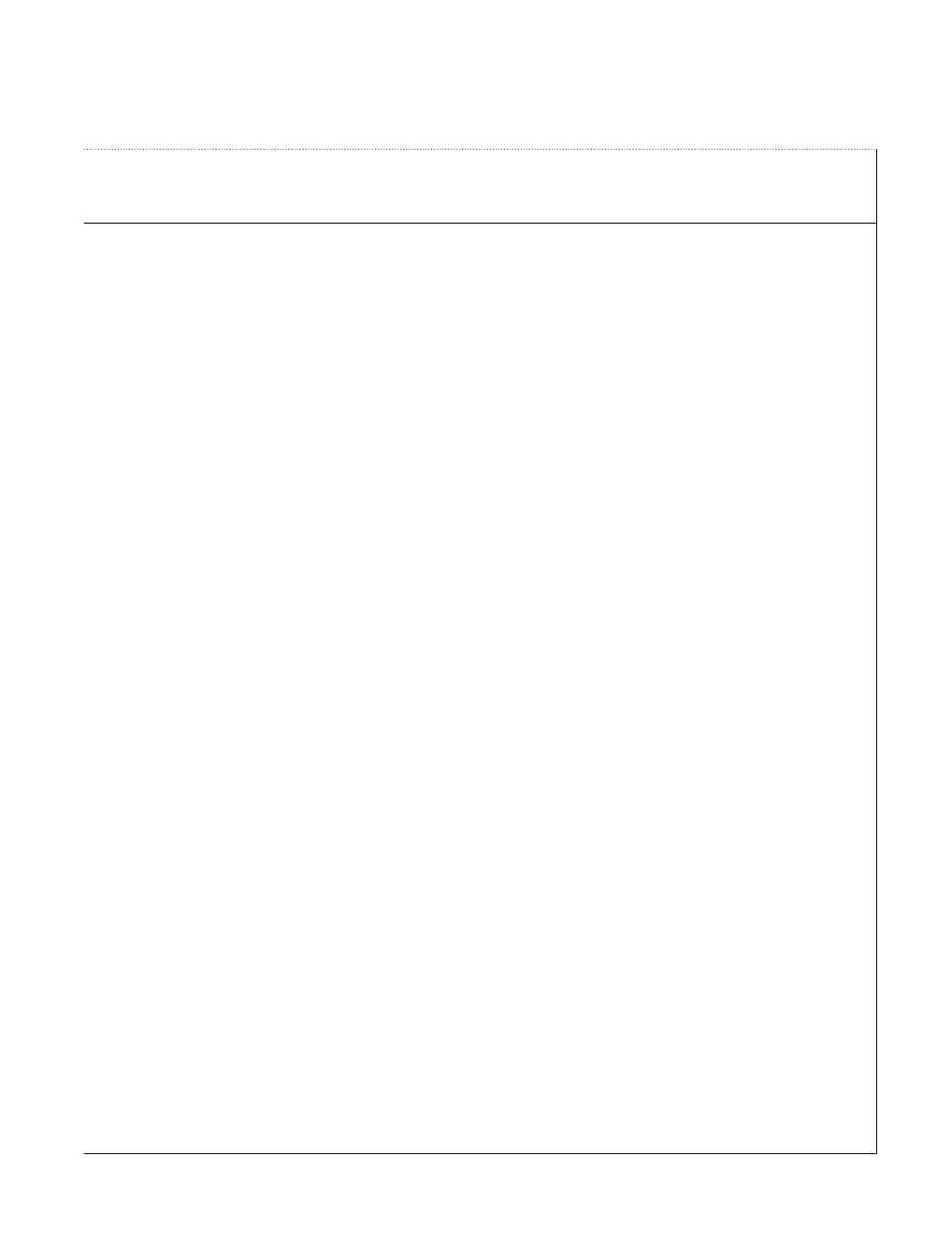
Sheathing Cutting and Application
4.1 S
ecurock
glass-mat sheathing may be applied with long dimensions parallel or perpendicular to framing
members except where limited by specific requirements. Sheathing orientation may be governed by local
code or by the requirements of shear or fire-rated construction. Consult local codes and site-specific
construction documents to ensure such requirements are met for every assembly prior to construction.
4.2 S
ecurock
glass-mat sheathing shall be cut to size by scoring the face mat with a utility knife from the face
side, or by sawing. Separate by snapping the panel away from the score line to fracture the core and then
by scoring the back mat with a utility knife. If a power saw is used, a cordless, low-rpm saw will generate
less airborne debris than a corded power saw.
4.3 The cut edges and ends of the sheathing shall be trimmed to obtain neat-fitting joints when installed.
4.4 Holes for pipe penetrations, fixtures or other small openings shall be scored or saw-cut from the face side
before removing the cutout.
4.5 Install panels with the logo side out. Panels are labeled “this side out” along the edge that must be visible
from the exterior side of the assembly when installed properly.
4.6 All vertical ends and edge joints shall abut over the centers of framing members and shall be offset a
minimum of one framing bay between adjacent rows of sheathing panels.
4.7 Center panel joints on framing members. Fit panels closely at edges and ends, but do not force together.
Hold panels in firm contact with framing members and secure with fasteners as specified. Fasteners
shall be driven flush with the panel surface, without countersinking or being deep enough to break the glass
mat, and into the framing. Fasten the panel to framing, working from the center of the panel toward the
edges and ends.
4.8 Screw profile must be designed for the framing in use, unless superseded by a more stringent specification.
The minimum requirements for sheathing fasteners shall be as follows:
a. Nails: 11-gauge hot-dipped galvanized roofing nails having a
7
/
16
" diameter head, 1-
1
/
2
" for
1
/
2
" sheathing, 1-
3
/
4
" for
5
/
8
" sheathing.
b. Screws: (1-
1
/
4
") (1-
5
/
8
") #6 buglehead corrosion-resistant fasteners.
c. Corrosion Resistance: Where sheet-type weather-resistive barriers or self-adhering membranes are
placed over the sheathing, corrosion resistance shall be equal to or greater than a hot-dipped galvanized
coating of 1.5 ounces of zinc per square foot of surface area. Where liquid or fluid-applied air and water
barriers are applied to the sheathing, or where no sheet-type weather-resistive barrier is used, screws
shall have a corrosion resistance of more than 800 hours per ASTM B-117. Stainless steel fasteners
may be used in coastal or aggressive environments.
d. Edge Distance: The minimum distance from any fastener to the edge or end of the panel is
3
/
8
".
e. Spacing: Maximum fastener spacing is 8" o.c.
4.9 Supplementary use of panel adhesive will strengthen the connection and bridge minor irregularities between
the panel and framing, facilitating enhanced performance and appearance. The use of adhesive, however,
will not reduce the number of fasteners required by the specification. For optimal bond, apply adhesive in
accordance with manufacturer’s instructions. Framing must be free from oil and dirt, and sheathing must be
clean and dry.
4.10 Fit sheathing snugly around window and door openings. Sheathing joints shall be offset a minimum of 4"
from the edge of any opening.
4.11 Sheathing shall be flashed at all openings (head, sill, etc.), and all roof/wall intersections (step, kickout, etc.)
so that water intrusion will not contact the sheathing.
4.12 Sheathing shall be no less than 8" from the finish grade in weather and water-protected siding and no less
than 12" from the ground when used in correctly drained and vented crawl spaces.