USG IMPERIAL Basecoat Plaster User Manual
Page 3
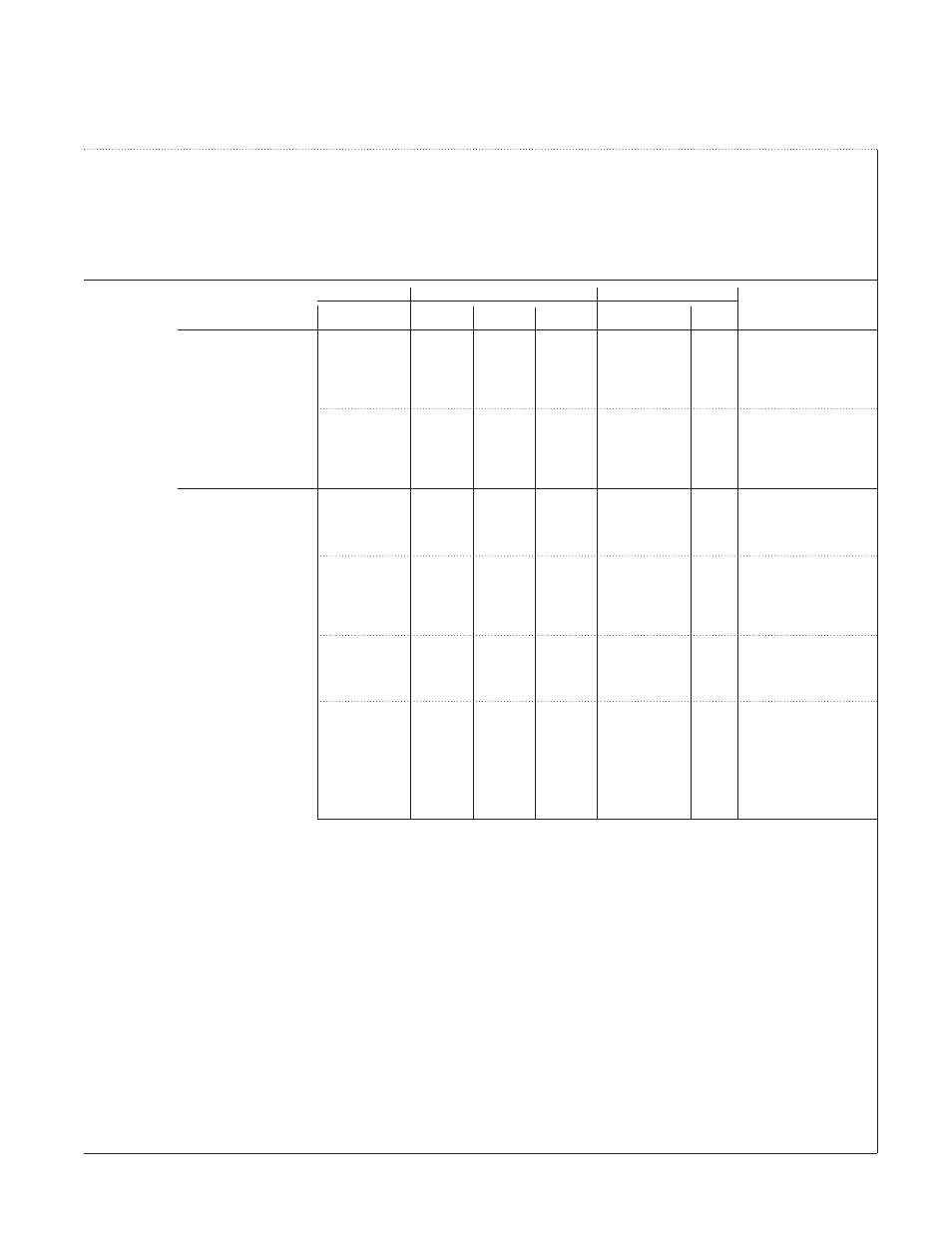
For I
MPERIAL
Basecoat/Basecoat MA
Ratio of mix (dry wt.)
Approx. coverage
(1)
Finish Characteristics
(Two-Coat) Applications
m
2
/ton
Product Lime
(2)
Gauging
(3)
Sand
(4)
ft
2
/ton
(metric)
Veneer Finishes/
I
MPERIAL
Brand
—
—
—
3200-3600
330-340 Prepared Finish—Ultimate in
High Strength–
Finish Plaster
surface hardness and abrasion
Superior Surface
resistance. Easily textured. Low
Hardness
productivity due to additional
work necessary to achieve a
smooth finish.
D
IAMOND
Brand
—
—
—
6000
615
Prepared Finish—Single bag,
Interior Finish
ready-to-use finish. Moderate
Plaster
(2)
strength. Acceptable workability.
Extremely adaptable to textured
finishes. Satisfactory smooth
finish.
Gauged Lime
R
ED
T
OP
Finish
(2)
—
—
—
4450
460
Prepared Finish—Hard dense
Putty Finishes/
prepared putty finish. Highest
Standard Surface
degree of workability of
Hardness
prepared finishes. Joinable,
dense, smooth finish.
S
TRUCTO
-G
AUGE
1
1
—
2940
300
Lime Gauging Finish—1:1
Plaster
2
1
—
4450
460
Hard dense putty finish; 2:1
Moderate surface hardness
putty finish. Good workability
and ease of application.
Excellent finish appearance.
R
ED
T
OP
, C
HAMPION
2
1
—
4040
410
Lime Gauging Finish—High
& S
TAR
Gauging
2
1
8
2900
300
productivity. Best workability
Plasters
putty finish. Joinable, easiest to
achieve a monolithic finish.
Good surface hardness.
R
ED
T
OP
Keenes 2
1
8
2430
250
Lime Gauging Finish—
Cement
1
1
—
3330
345
Unique, only truly retemperable
2
1
—
3870
400
material.Ultimate choice for
texturing. Can be floated for
extended time period or built up
to promote heavy, drawn down
type texture finishes. Can be
used for coloring or tinting large
plaster wall area.
(1) Total mix. (2) Packaged in 50 lb. (22.7 kg) bag. (3) Packaged in 100 lb. (45.4 kg) bag. (4) Natural, uniform, graded, clean silica sand
.
Finish coat materials are applied by scratching in and doubling back with the selected finish (see table above) to
achieve a smooth, dense surface for decoration, free of surface blemishes. For textured finishes, floating or tex-
turing is conducted once the surface has become firm or textured with additional material from the same batch.
Float finishing should be conducted using water sparingly to avoid texture and color variation.
For a spray-applied finish, mix R
ED
T
OP
Keenes Cement-lime-sand in proportion of 50 lbs. (23 kg) Keenes Cement
to 100 lbs. (45 kg) dry double-hydrated lime, and up to 400 lb. (180 kg) but not less than 200 lb. (60 kg) clean,
properly graded silica sand with sufficient water to form a smooth consistency for hand application. Apply this mix
evenly over a properly prepared I
MPERIAL
Brand Basecoat surface by first applying a well-ground-in scratch coat,
then immediately double-back with sufficient material to cover the basecoat to a total thickness of 1/16
Љ to 1/8Љ.
When the surface has become firm by water removal, float the surface to a uniform blemish-free flat texture. After
floating, and while the application is still wet but totally firm, prepare additional finish material with the consisten-
cy adjusted for spray application. With either a hand-held hopper gun or machine-application equipment without
catalyst spray, apply texture to provide a uniform texture appearance. Vary aggregate grading, aggregate propor-
tion, number of passes over the surface, air pressure and nozzle orifice size as necessary to achieve the desired
finish. For more information about spray-applied finishes, see USG publication PM6, Veneer Plaster Application
Technique.
Page 3 of 4