Ecm overview and setup (cont.) – Titus Fan Powered Term. IOM User Manual
Page 6
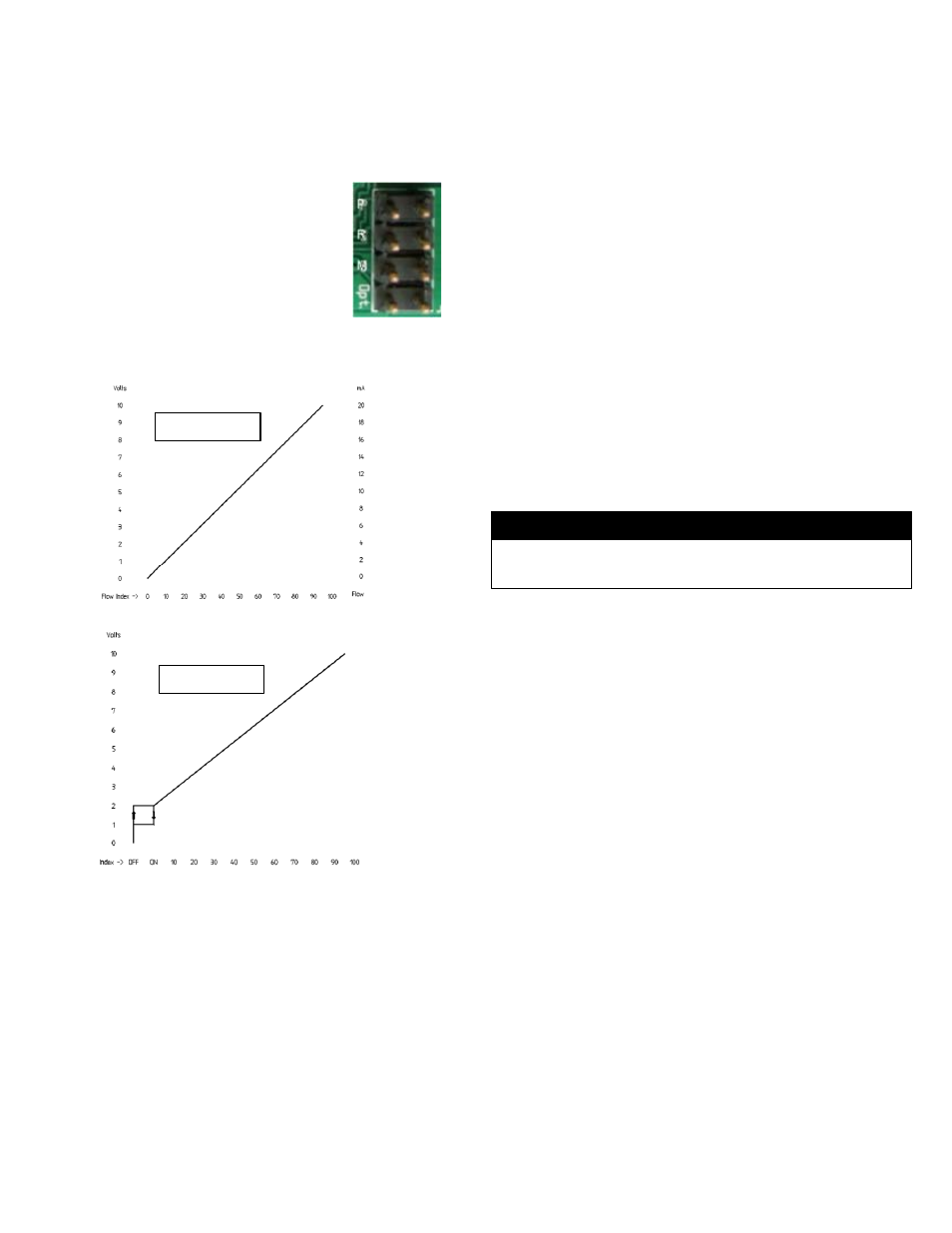
TU-FB-IOM 08-26-13
6 of 9
ECM Overview and Setup (Cont.)
DDC Control - Air Balance
If the DDC Controller signal is already installed, air
balance can be achieved using the DDC Controller
software tools. Please notice that a control signal less than
0.2Vdc may put the interface board into manual override.
Avoid setting the DDC signal to less than 0.2Vdc.
Cycle power ON/OFF for faster lockout removal.
Manual Air Balance
The interface board can be manually adjusted before the
DDC Controller signal is available. The balancer’s manual
adjustment has authority until automation is connected.
Air Balancer
1. Use Adjust to set the air flow. This adjustment will have
authority for at least 15 minutes.
2. Read the flashing green light and record the flow index
on the air balance report.
DDC Integrator
1. Set the Signal to 0Vdc to invoke manual override.
2. Record the RPM on the air balance report.
3. Enter the flow index the air balancer entered on the air
balance report.
4. Observe the RPM is at or near the RPM observed in
step 2.
5. Cycle the motor on/off 5 times. This clears the manual
override function unless the “M” jumper is in
place.
Turning Adjust potentiometer locks out the BAS
signal for 15 minutes
WARNING
Remote PWM Signal Interface Board Details
Jumpers
P - Jumper provides ON/OFF control by
switching the motor's "GO" control line
when the input signal drops below the
2 volt (4 mA) operating point. without the
jumper, turn power to the interface board
+ On/Off to control motor On/Off.
Rotating Adjust changes the Flow Index
from 0 to 100.
The “P” jumper also allows manual on/off control.
M - Jumper enables manual override. Manual override is
overridden when the 0-10V automation signal exceeds
0.2Vdc.
Manual override controls the motor before Building
Automation System (BAS) is installed, or when BAS fails.
Without the “M” jumper, manual override is enabled
whenever Adjust is turned. It is disabled by causing the
Interface board to turn the motor off/on 5 times while signal
is greater than 0.1Vdc.
R - Jumper reverses Adjust rotation so adjustment is
correct from the component side of the board.
Opt - The Opt. space has no function. The space
may be used to store an unused jumper.
Signal with
“P” Jumper Out
Signal with
“P” Jumper In
Input / Output Control Signals
"Opt" Configuration
- 0-10 Vdc = 1% to 100%
"P" Configuration
- 2-10Vdc = 0-100%
- 4-20mA = 0-100%
- ON/OFF Control Between1 & 2
Vdc (2 & 4 mA)
RPM Signal
- 0-10 Vdc, 5 mA max. = 0 to 2,000
RPM in 10 RPM steps
Outputs Go & VSpd
- 22Vdc @ 5mA