Non-standard electrical interfaces, Electrical launch support equipment, Payload design constraints – Orbital Minotaur VI User Manual
Page 77: Payload center of mass constraints, Final mass properties accuracy, Pre-launch electrical constraints, Payload emi/emc constraints
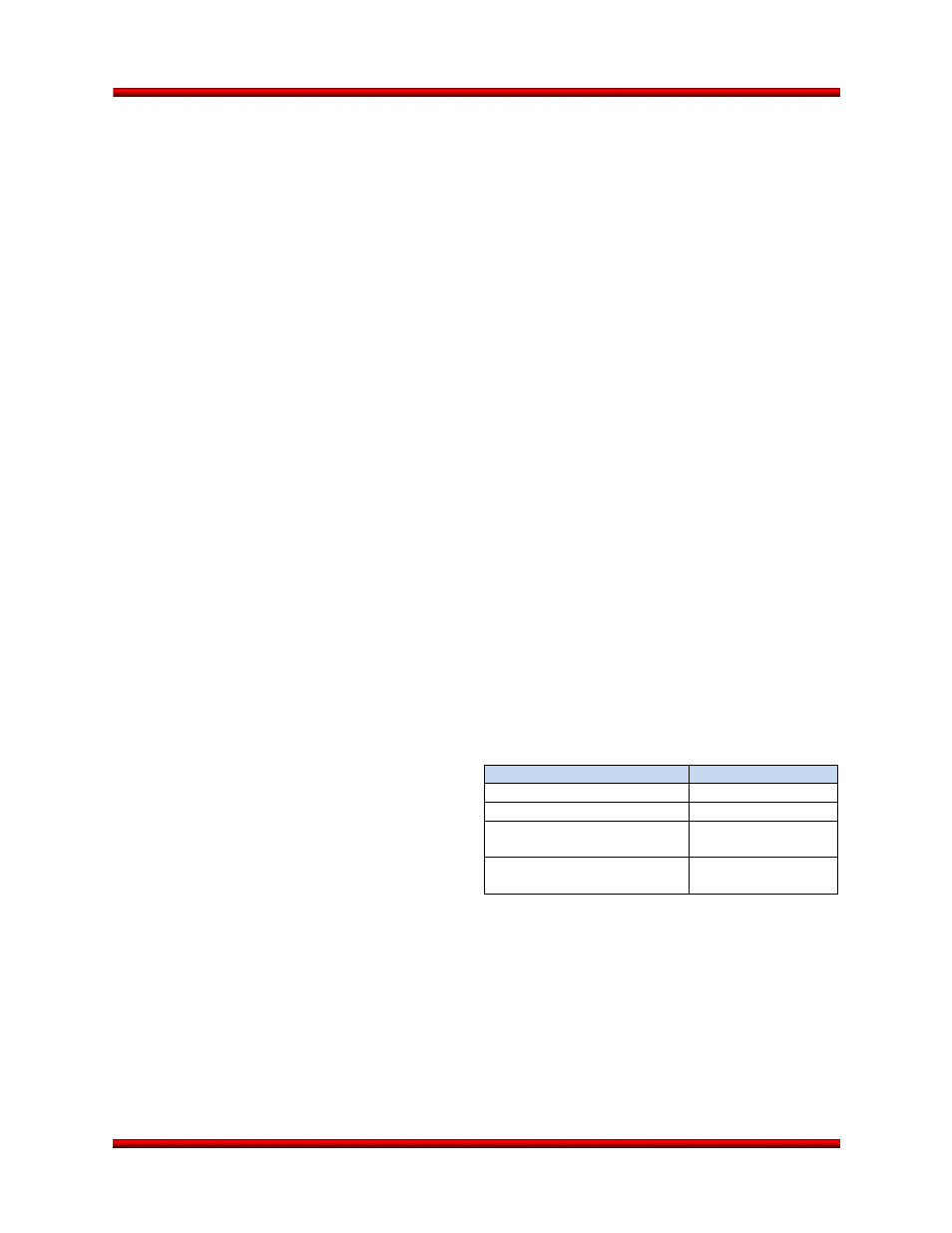
Minotaur IV • V • VI User’s Guide
Section 5.0 – Payload Interfaces
conditioning, PCM formatting (programmable) and data transmission bit rates. The number of channels,
sample rates, etc. will be defined in the Payload ICD.
5.3.9. Non-Standard Electrical Interfaces
Non-standard services such as serial command and telemetry interfaces can be negotiated between
Orbital and the payload on a mission-by-mission basis. The selection of the separation system could also
impact the payload interface design and will be defined in the Payload ICD.
5.3.10. Electrical Launch Support Equipment
Orbital will provide space for a rack of customer supplied EGSE in the LCR, and at the on-pad LEV or
SEB. The equipment will interface with the launch vehicle/spacecraft through either the dedicated payload
umbilical interface or directly through the payload access door. The payload customer is responsible for
providing cabling for their EGSE within the LCR, LEV, and SEB to the appropriate umbilical interface.
Separate payload ground processing harnesses that mate directly with the payload can be
accommodated through the payload access door(s) as defined in the Payload ICD. The payload will
provide all cabling for this operation.
5.4. Payload Design Constraints
The following sections provide design constraints to ensure payload compatibility with the Minotaur
launch vehicle.
5.4.1. Payload Center of Mass Constraints
Along the Y and Z-axes, the payload CG must be within 1.0 inch (2.54 cm) of the vehicle centerline.
Payloads whose CG extend beyond the 1.0 inch lateral offset limit will require Orbital to verify the specific
offsets that can be accommodated.
5.4.2. Final Mass Properties Accuracy
In general, the final mass properties statement
must specify payload weight to an accuracy of
±0.5% of the payload mass, the center of gravity
to an accuracy of at least 0.64 cm (0.25 in.) in
each axis, moment of inertia to ±5%, and the
products of inertia to an accuracy of less than
2.7 kg-m
2
(2.0 slug-ft
2
), as shown in Table 5.4.2-
1. However these accuracies may vary on a
mission specific basis. In addition, if the payload
uses liquid propellant, the slosh frequency must be provided to an accuracy of 0.2 Hz, along with a
summary of the method used to determine slosh frequency.
5.4.3. Pre-Launch Electrical Constraints
Prior to launch, all payload electrical interface circuits are constrained to ensure there is no current flow
greater than 10 mA across the payload electrical interface plane. The primary support structure of the
spacecraft shall be electrically conductive to establish a single point electrical ground.
5.4.4. Payload EMI/EMC Constraints
Table 5.4.2-1. Payload Mass Properties
Measurement Tolerance
Component
Accuracy
Mass
±0.5%
Principal Moments of Inertia
±5%
Cross Products of Inertia
±2.7 kg – m
2
(±2.0 slug – ft
2
)
Center of Gravity X, Y,
and Z Axes
±0.64 cm
(±0.25 in.)
Release 2.0
June 2013
62