JLG 40RTS ANSI Service Manual User Manual
Page 20
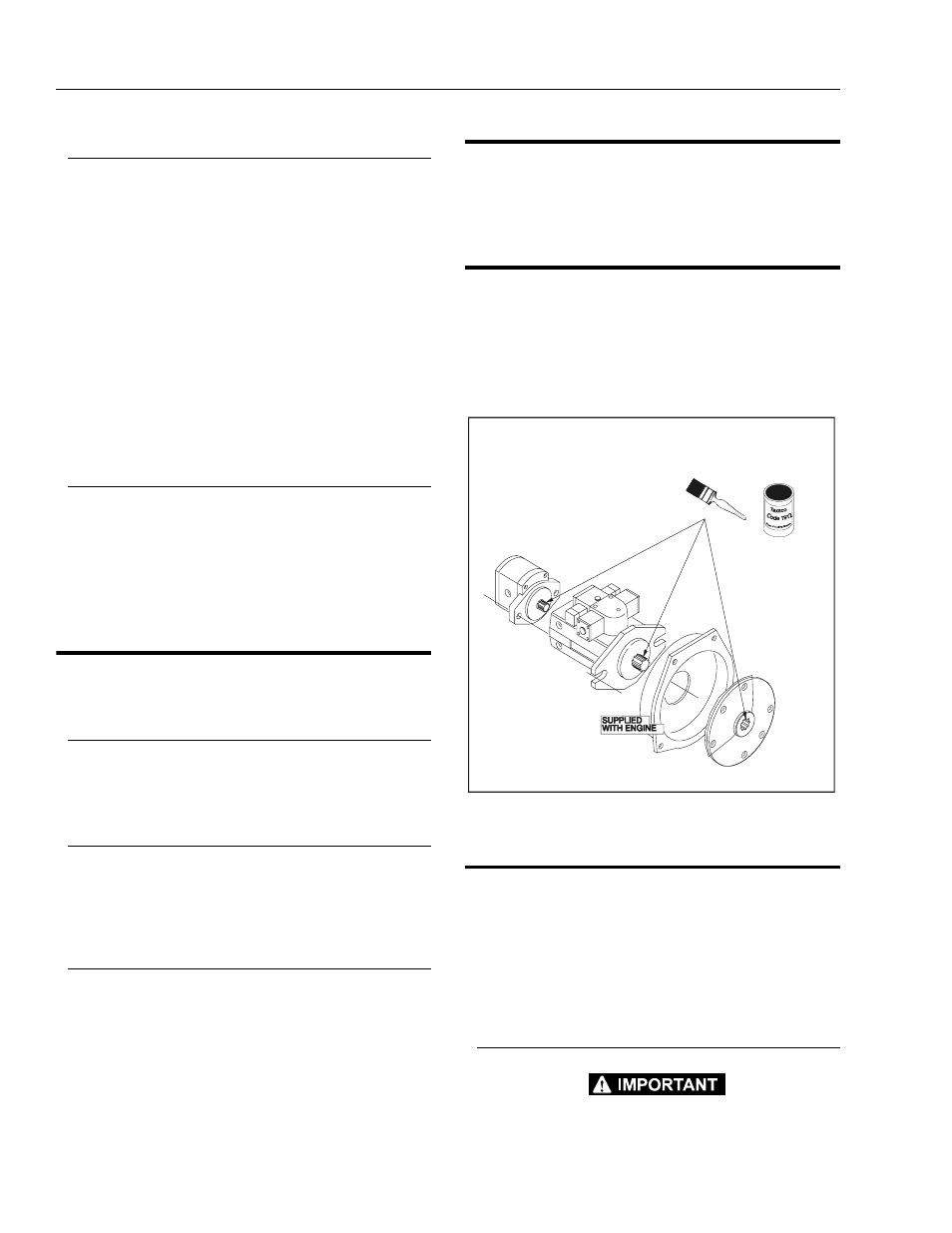
SECTION 2 - PROCEDURES
2-4
– JLG Sizzor –
3120691
Relief Valves
Main relief valves are installed at various points within the
hydraulic system to protect associated systems and com-
ponents against excessive pressure. Excessive pressure
can be developed when a cylinder reaches its limit of
travel and the flow of pressurized fluid continues from the
system control. The relief valve provides an alternate path
for the continuing flow from the pump, thus preventing
rupture of the cylinder, hydraulic line or fitting. Complete
failure of the system pump is also avoided by relieving cir-
cuit pressure. The relief valve is installed in the circuit
between the pump outlet (pressure line) and the cylinder
of the circuit, generally as an integral part of the system
valve bank. Relief pressures are set slightly higher than
the load requirement, with the valve diverting excess
pump delivery back to the reservoir when operating pres-
sure of the component is reached.
Crossover Relief Valves
Crossover relief valves are used in circuits where the actu-
ator requires an operating pressure lower than that sup-
plied to the system. When the circuit is activated and the
required pressure at the actuator is developed, the cross-
over relief diverts excess pump flow to the reservoir. Indi-
vidual, integral relief’s are provided for each side of the
circuit.
2.6
COMPONENT FUNCTIONAL
DESCRIPTION
Piston Hydraulic Pump
The Sundstrand piston hydraulic pump is attached to and
driven by the engine. The pump is a 2.8 in.[3] (45.9 cm[3])
displacement piston pump that powers the drive motors.
Gear Hydraulic Pump
The John Barnes gear pump is “piggy-backed” to the pis-
ton pump, and operates all machine functions except
drive. The gear pump has a displacement of 0.6 in. [3]
(10.5 cm[3]).
Manual Descent Valve
The manual descent valve is located on top of the holding
valve on the lift cylinder. The holding valve is a normally
closed solenoid valve, and holds the platform in place
when raised. When activated, the valve opens to permit lift
down. The holding valve is connected to the manual
descent valve, which is connected to a cable which, when
pulled, manually opens the lift down port of the valve and
allows the platform to be lowered in the event hydraulic
power is lost.
2.7
SLIDING WEAR PADS
The original thickness of the sliding pads is 2.0 in. (50.8
mm). Replace sliding pads when worn to 1.87 in. (47.5
mm).
2.8
PUMP AND COUPLING LUBRICATION
To insure proper operation and a long service life for the
Hayes pump coupling, it is necessary to lubricate the
splines of the coupling any time the coupling is disassem-
bled or replaced. Lubricate the splines with Texaco Code
1912 Pump Coupling Grease ONLY. No other lubricant is
recommended.
2.9
CYLINDER CHECKING PROCEDURES
NOTE: Cylinder checks must be performed any time a cylin-
der component is replaced or when improper system
operation is suspected.
Cylinder w/o Counterbalance Valves - Steer
Cylinder, Axle Lockout Cylinder (If
Equipped)
OPERATE FUNCTIONS FROM GROUND CONTROL STATION
ONLY.
Figure 2-1. Pump and Coupling Lubrication