Storage, Motor lubrication – Aerovent IM-121 User Manual
Page 10
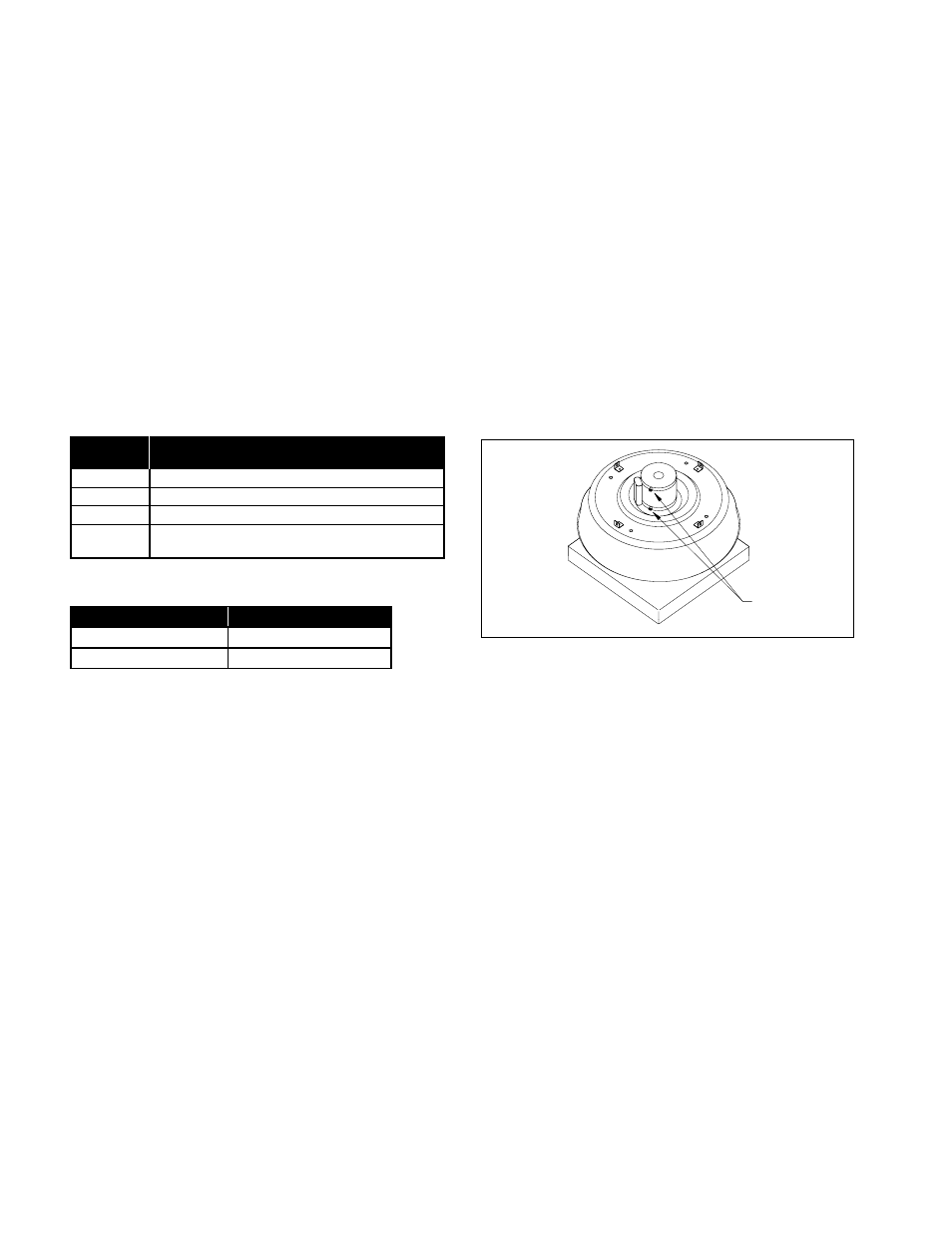
10
Aerovent IM-121
OIL TUBES
Figure 10. Sleeve Bearing Motor Oil Tube Location
Storage
If fans are stored for any length of time, they should
be stored in a clean, dry location to prevent rust and
corrosion. Outdoor storage is not recommended. When
outdoor storage is necessary, fans should be protected
from the elements as completely as possible. Cover the
fan inlet and outlet and keep motors dry and clean.
For extended storage (more than 3 months) motor shafts
and bearings should be rotated monthly. If stored longer
than 6 months, bearing grease in motor and fan should
be purged and replaced with compatible grease. Belts
should be rechecked for proper tension. Storage records
should be kept to assure proper maintenance. The fac-
tory can advise warranty centers to provide motor and
bearing service if needed.
Table 5. Suggested Fan Bearing Greasing Intervals
INTERVAL
TYPE OF SERVICE
(MONTHS)
12 to 18
Infrequent operation or light duty in clean atmosphere.
6 to 12
8 to 16 hrs./day in clean, relatively dry atmosphere.
3 to 6
12 to 24 hrs./day, heavy duty, or if moisture is present.
1 to 3
Heavy duty in dirty, dusty locations; high ambient
temperatures; moisture laden atmosphere; vibration.
Table 6. Grease Manufacturers
MANUFACTURER
GREASE (NLGI #2)
Shell
Shell Gadus S2 V100 2
Exxon/Mobil
Ronex MP
12. The standard pillow block bearings on belt driven
ventilators are factory lubricated and are provided with
external grease fittings. Lubrication annually is recom-
mended, or more frequently if needed (see Table 5).
It is recommended to add fresh grease at start-
up, but do not over-grease. Use only 1 or 2 shots
of a recommended lubricant with a hand gun in
most cases (see Table 6). Maximum hand gun rating
40 P.S.I. Rotate bearings during lubrication where
good safety practice permits.
CAUTION: Greases of different soap bases
(lithium, sodium, etc.) may not be compatible when
mixed. Prevent such intermixing by completely purg-
ing the bearing of old greases.
The most frequent causes of bearing failure are
not greasing often enough, using an excessive
quantity of grease, or using incompatible greases.
Excessive vibration, especially if the bearing is not
rotating, will also cause bearings to fail. Bearings
must also be protected from water and moisture to
avoid internal corrosion.
13. During the first few months of operation it is rec-
ommended that the bearing setscrews be checked
periodically to ensure that they are tight.
14. The rotating wheel requires particular attention since
materials in the air being handled can build up on
the blades to cause destructive vibration or weaken
the structure of the wheel by corroding and/or erod-
ing the blade metal. Regular inspection and correc-
tive action at intervals determined by the severity of
each application are essential to good service life
and safety.
Motor Lubrication
Motors which contain ball bearings are permanently
lubricated from the factory. No additional maintenance
is required.
Motors which contain sleeve bearings require lubrication
every six (6) months. Use SAE-20W lubricant and add
five (5) drops to each location shown in Figure 10. DO
NOT OVER LUBRICATE.