Figure 9: shaft end gap – Hale 4DK Series User Manual
Page 25
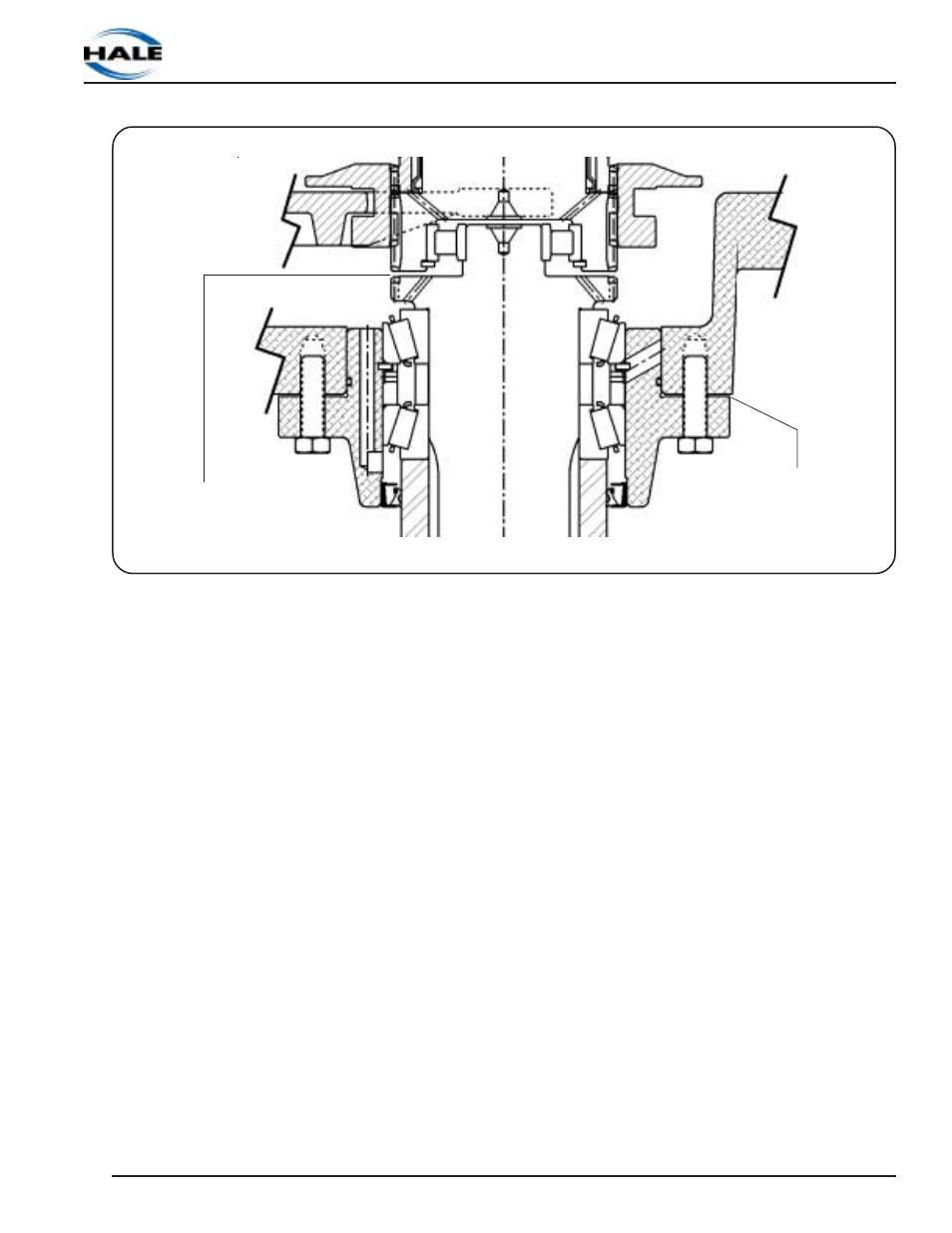
Manual p/n: 029-0020-79-0
25
4DK Series Pumps
5. Insert tail shaft into gearbox housing,
aligning inner race of roller bearing with
outer race on the mating input shaft. Also
see Figure 9: "Shaft End Gap."
6. Carefully slide bearing carrier over the tail
shaft.
7. Temporarily secure bearing cover using
eight 7/16-14 x 1-1/2" screws. Torque
screws to 50ft.-lb. (68N-m).
8. Using a feeler gauge, measure the gap
between the input and tail shafts, as shown
in Figure 9 above.
9. Remove the bearing carrier and install
correct amount of spacers to produce a
0.060" ± 0.010" (1.524mm ± 0.254mm)
gap.
Note: Under normal circumstances, replacing
bearings, seals, cones, etc. will have little effect on
the gap setting. Reinstalling all existing shims will
maintain the required gap (0.060" ± 0.010"
[1.524mm ± 0.254mm]).
Note, continued: However, if either shaft is
replaced or the housing is changed, the gap must
be checked and set.
10. Repeat Steps 5 through 8. Also repeat
Step 9, if necessary.
11. When the gap is properly shimmed and
you are ready to install the bearing carrier
to the gear box, install a new gasket.
Using a light coating of general purpose
grease to hold the gasket in place.
12. Place the inner spacer and shims onto the
tail shaft. Insert the remaining bearing
cone onto the tail shaft. Both are a tight fit.
13. Carefully press a new oil seal into the
bearing carrier.
14. Place the yoke onto the end of the tail shaft
and secure using the 3/4-10 x 1-3/4" screw
and washer. Torque screw to 260 ft.-lb.
(352 N-m).
Adjust gap between
shafts to 0.060" ± 0.010"
1.52mm ± 0.25mm
Figure 9: Shaft End Gap
Bearing Carrier
Shim Placement