Cirrus Logic AN31 User Manual
Page 12
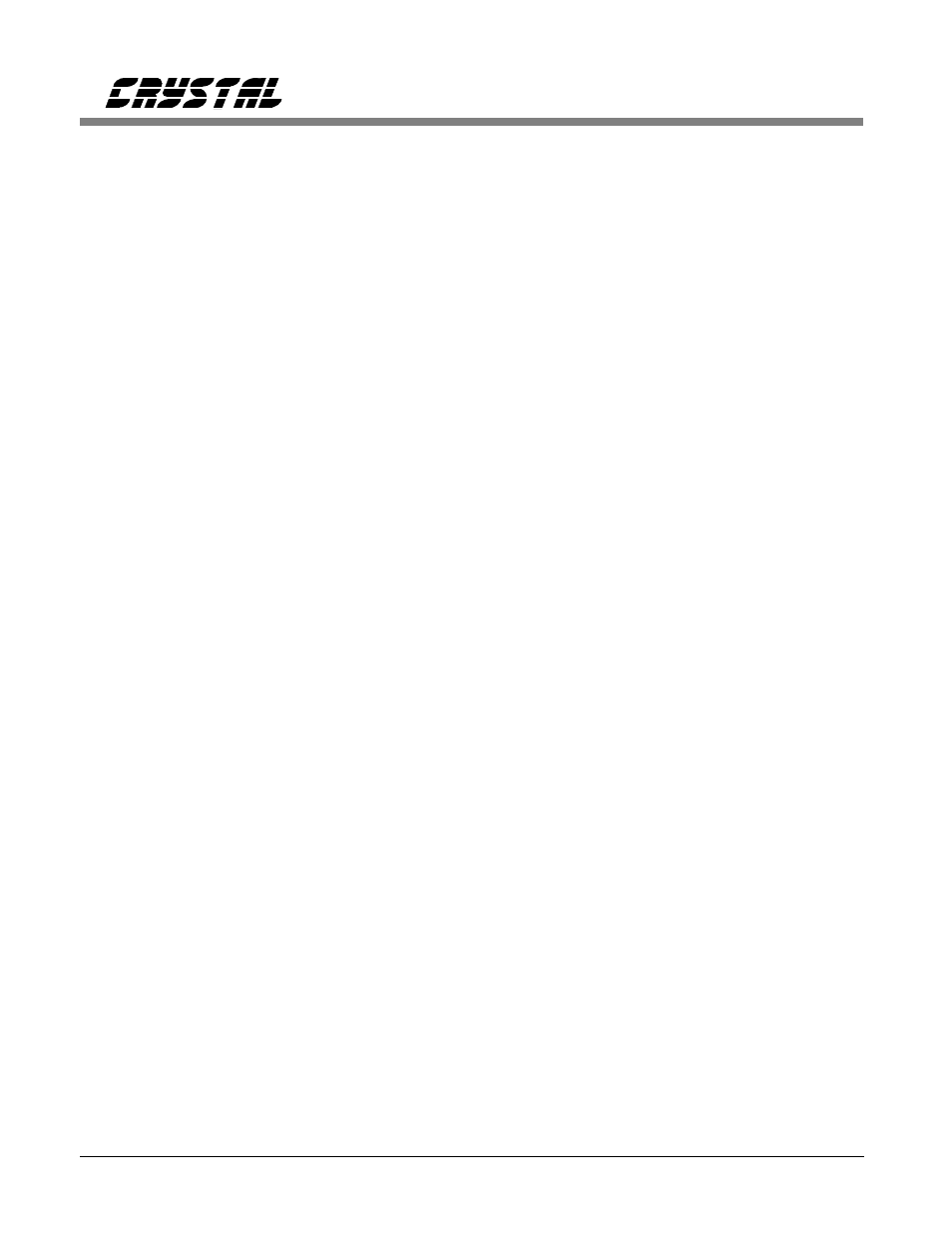
includes the negative supply rail. One
application for this may be for measuring a
temperature compensating resistor in series with
the bridge (see inset in Figure 9).
The converter in Figure 9 is set up in bipolar
mode (use bipolar mode even if you want
unipolar measurements as the bipolar setup
provides less noise per code and allows for
negative tempco drift of the zero reference point)
and runs at 200 conversions a second. To correct
offset and measurements on both channels, the
following measurement sequence was used:
Select the DG303 to short the inputs to both
channel one and channel two. Use A0 on the
converter to select channel one. Perform one
conversion and discard the data to allow for
settling. Perform a second conversion and keep
the offset code for channel one. Change A0 to
opposite state and measure the offset code for
channel two. Switch the DG303 on both
channels to measure the input signal and set A0
to measure channel one. Perform one dummy
conversion and discard the data. Then perform a
second conversion and keep the reading.
Correct this reading with the offset reading taken
for the same channel. Then change A0 and read
channel two and correct it for offset. Each
channel takes four conversions per result, so for
two channels, outputs are available at 25 per
second. A running average of 12 corrected
words is recommended to improve noise
performance. With 12 words averaged, the
performance is greater than 150,000 noise-free
counts with two updates per second for each
channel.
If the circuit in Figure 9 is used at higher
temperatures, one DG303 should be used for
each amplifier stage with a switch (always on)
included in the negative lead of the bridge
circuit. With this configuration, the errors due to
leakage currents and the on resistance of the
switches will be more balanced on both the plus
and minus leads of the bridge.
The voltage reference input to the A/D converter
is buffered to reduce loading by the Kelvin sense
leads. If the voltage reference Kelvin sensing
lines are long, 50 and 60 Hz line interference
may be picked up. The voltage reference input to
the CS5504/5/6/7/8/9 should be filtered to
prevent line interference if the devices are
operated at a clock frequency other than
32.768 kHz.
Bridge with Signal Chopping Using CS5504
The load cell is often the dominant cost factor in
many weighing systems. A lower cost load cell
can be achieved by leaving out the temperature
compensation gages and reducing testing during
manufacturing. As long as the load cell
temperature drift is repeatable, the entire system
can be compensated with software in a
microcontroller. In this type of system, a
temperature sensor is usually embedded inside
the load cell. The entire system is then
characterized over temperature. A
microcontroller reads the load cell and its
temperature and uses a look-up table to correct
the load cell output for drift over temperature.
Figure 10 illustrates an example.
The circuit uses the CS5504 two channel fully
differential A/D configured to convert at 200
samples per second. The analog portion of the
A/D and the bridge are operated from +10 volts.
The voltage reference for the A/D is developed
from the bridge excitation. Channel two of the
converter measures the output of a thermistor
mounted in the load cell housing. The thermistor
is excited with the same voltage as the bridge.
The output of the bridge is amplified by a buffer
amplifier composed of two LT1007s. The
CS5504 is operated in bipolar mode with
±
524,000 counts. A DG303 analog switch is
used to reverse the polarity of the signal into the
amplifier upon command from the
microcontroller. A convert (CONV) command is
Bridge Transducer Digitizer Circuits
12
AN31REV3