Piping, Warning, Suction piping – Goulds Pumps 3100 - IOM User Manual
Page 24: Discharge piping
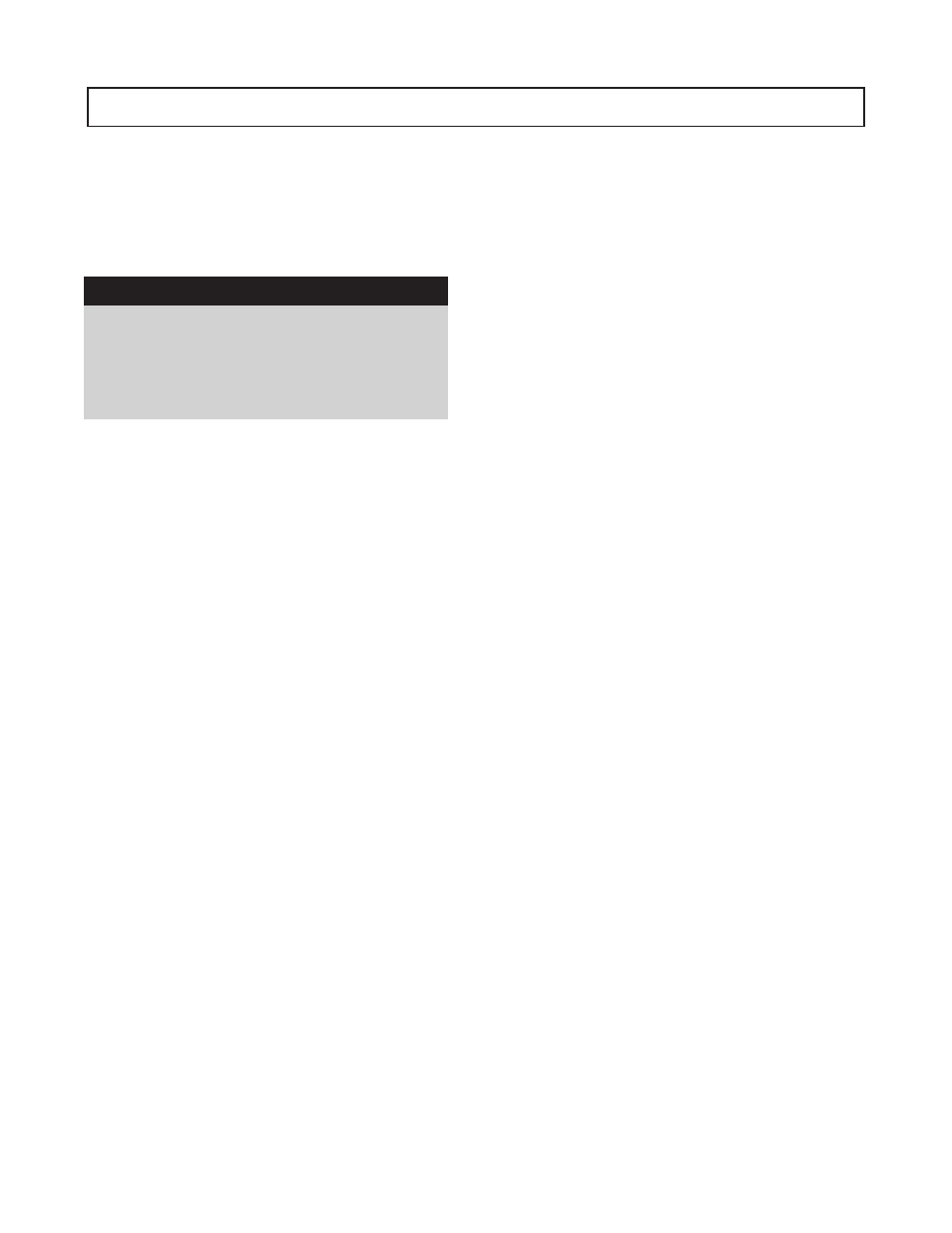
PIPING
Guidelines for piping are given in the “Hydraulic
Institute Standards” (Edition 14, Centrifugal Pump
section) and should be reviewed prior to pump
installation.
1.
Pump must be supported independently and
must line up naturally with the pump flanges.
▲
!
WARNING
Never draw piping intor place by forcing the
flanged connections to the pump. This will
impose dangerous strains on the unit and
cause misalignment between pump and driver.
Pipe strain can adversely effect the operation
of the pump. That could result in serious
personal injury and damage to equipment.
2.
Piping runs shall be designed to minimize
friction losses.
3.
DO NOT make final connection of piping to
pump until grout has hardened and pump and
driver hold-down bolts have been tightened.
4.
Piping should be arranged to allow pump
flushing and draining prior to removal of the
pump for servicing.
5.
System should be thoroughly cleaned prior to
installation.
6.
Gasket installation and materials must be
suitable for the service.
SUCTION PIPING
Properly installed suction piping is a necessity for
trouble free pump operation. Suction piping should
be flushed BEFORE connection to the pump.
1.
Use of elbows close to the pump should be
avoided. There should be a minimum of 2 pipe
diameters of straight pipe between the elbow
and the suction inlet. Any elbows used should
be long radius (Fig. 9).
2.
Use suction pipe one or two sizes larger than
pump suction, with a reducer at suction flange.
Suction piping must never be of smaller
diameter than the pump suction.
3.
Reducers, if used, must be eccentric at pump
suction flange with sloping side down (Fig. 9).
4.
Suction strainers, when used, must have a net
“free area” of at least three times the suction
pipe area (Fig. 9).
5.
Separate suction lines are recommended when
more than one pump is operating from the
same source of supply.
Suction Lift Conditions
1.
Suction pipe must continuously slope upwards
towards pump suction to eliminate air pockets.
2.
All joints must be air tight.
3.
A means of priming the pump must be provided,
such as a foot valve.
Suction Head/Flooded Suction Conditions
1.
An isolation valve should be installed in suction
line to permit closing of the line for pump
inspection and maintenance (Fig. 10).
2.
Piping should be level or slope gradually
downward from source of supply.
3.
No portion of piping should extend below pump
suction flange.
4.
The suction pipe shall be submerged sufficiently
below the liquid surface to prevent vortices and
air entrainment at the supply (Fig. 10).
DISCHARGE PIPING
1.
Isolation and check valves should be installed in
the discharge line. Locate check valve between
isolation valve and pump which will permit
inspection of check valve. An isolation valve is
required for isolating, priming, regulation of flow,
inspection and maintenance of the pump. A
check valve prevents pump damage due to
reverse flow when driver is turned off (Fig. 11).
2.
Increasers, if used, should be placed between
the pump and check valves.
3.
Cushioning devices should be used to protect
pump from surges and water hammer, if
quick-closing valves are installed in the system.
16
3100 IOM 1/97