Repriming the hydraulics – Pulsafeeder Pulsa Series 200-680C User Manual
Page 10
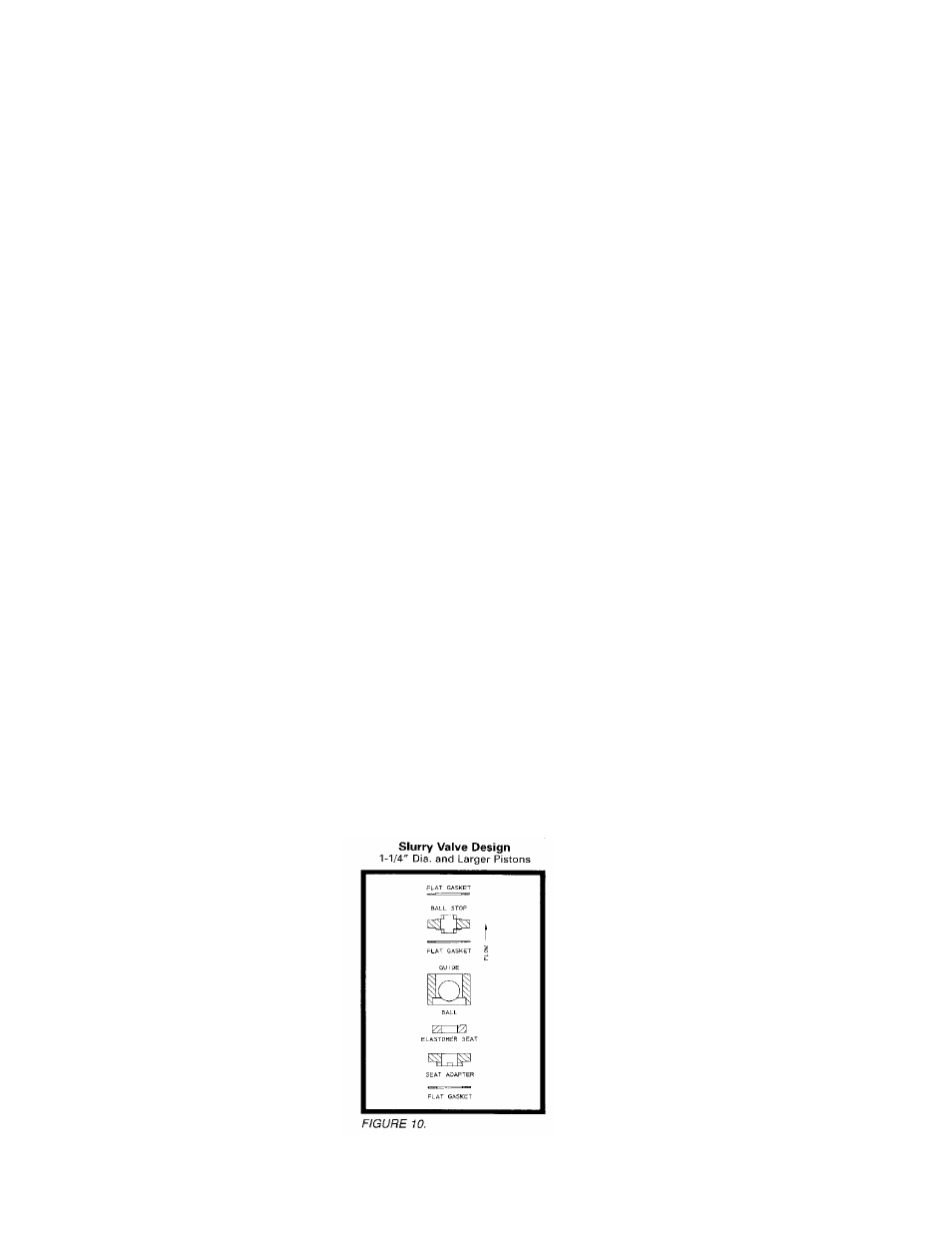
10
13. Diaphragm can be
3.
Connect inlet piping.
removed from the
4.
With discharge line
8.
Add PULSAlube oil to
reagent head by applying
bypassed around
front and rear oil
air pressure to one of the
process or to drain, start
reservoirs to bring oil
valve ports while
motor and prime reagent
level up to top of
blocking the other. Be
head.
partition.
sure diaphragm is
5.
Set stroke length
9.
After pump has run for
directed away from
adjustment to maximum
several hours, again
personnel so that it does
stroke.
check for any last traces
not strike the body when
6.
If not already lose,
of air at the bypass valve.
being expelled from the
counting turns, loosen
head.
the hydraulic bypass
Check Valve
14. Diaphragms which are
valve located at the top
punctured or show
of the hydraulic system
evidence of tearing or
to atmosphere and any
Operating experience on
abrasion at the sealing
air present will vent back
thousands of installations has
edge should be
into the gearbox oil
indicated that many pump
replaced. If diaphragm
reservoir as the
troubles have to do with check
shows evidence of
automatic make-up valve
valves. Problems usually
hardening so as to be
fills the piston/diaphragm
stem from (a) an
non-flexible it should be
chamber. Air bubbles
accumulation of trash
replaced.
will be evident at the vent
between the valve and seat,
Repriming Hydraulic
head in back of return
seating surfaces, (c) erosion
Systems on HYDRACONE
spring.
from high velocity flow, or (d)
Models
7.
When last traces of air
normal physical damage after
1.
Reassemble diaphragm
retighten the bypass
and reagent head,
valve the same number
When inspecting the valves,
tightening all bolts
of turns or to a desired
separate the assembly and
securely and evenly.
setting using a pressure
examine the components for
2.
Reassemble valve
gauge in the process
wear, damage or
housing, valves, seats
line. Approximately a 1/2
accumulation of solids. A ball
and seat gaskets and
turn more after process
valve seat should have a
take care in inserting
pressure setting has
sharp 90 edge, free of any
gaskets that they are
been reached will seat
nicks or dents. Hold the ball
properly placed. Tighten
valve. The valve can be
firmly on the seat and
securely.
set higher if desired but
examine against a light. If
hole, top center of pump
(b) corrosion which damages
have been expelled
extended service.
do not exceed MAX.
light is visible between the two
OPERATING
then replace the seat and/or
PRESSURE indicated on
ball.
the nameplate.
Figure 7, 8, 9 and 10
o
When reassembling after
cleaning or replacement be
sure to use new seals.