Dc drive configuration, Jumpers, Potentiometer descriptions – Pulsafeeder Pulsa Series Cruise Control User Manual
Page 14: Dc d, Rive, Onfiguration, 1 jumpers, 2 potentiometer descriptions
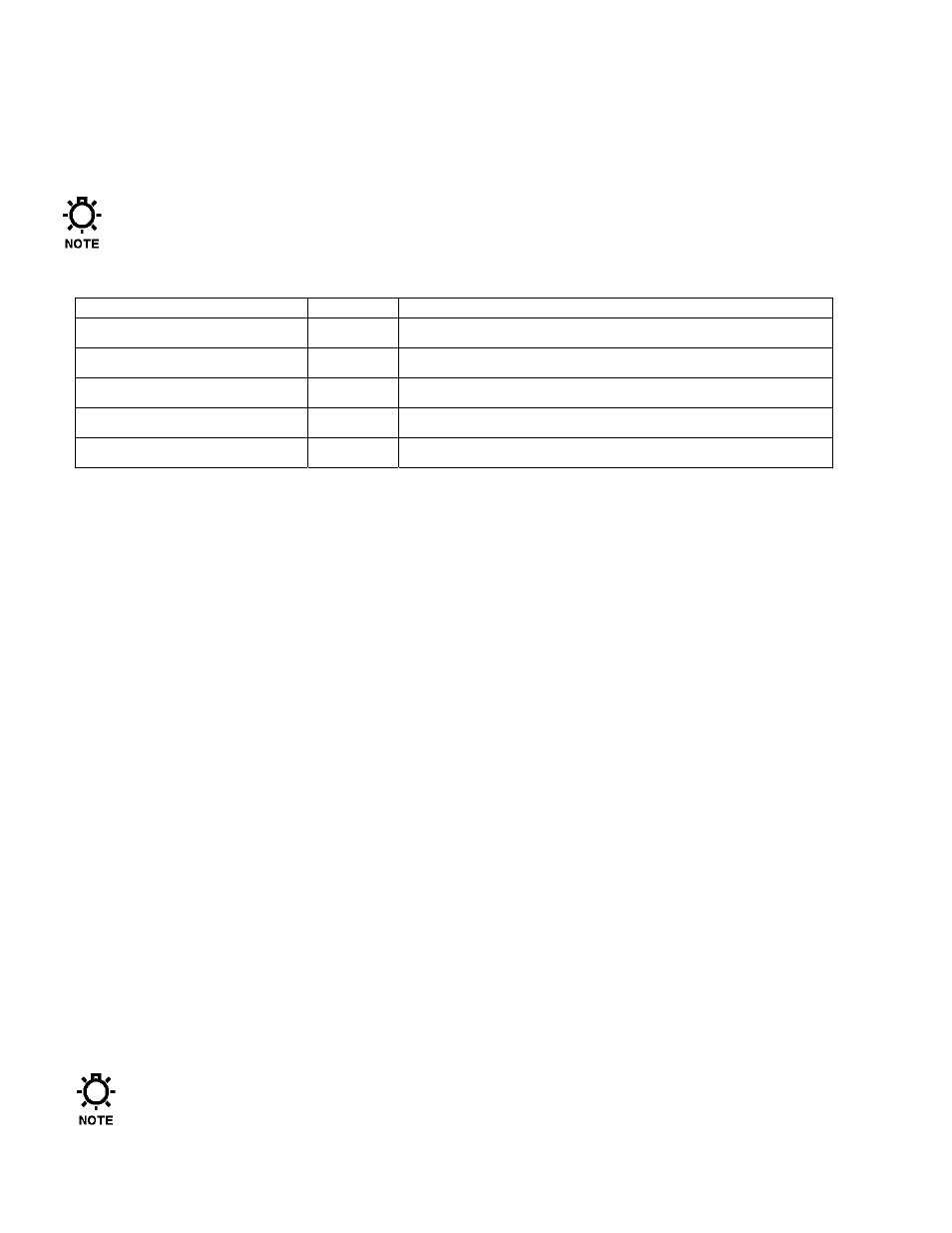
8. DC
Drive
Configuration
The Control Techniques DC Drive is properly configured for your application during assembly. The following
information is for reference only.
Some panels may be supplied with an alternate drive to conform to the user’s specification. If your
panel is so equipped, please refer to the appropriate manufacturer’s literature for this information.
8.1 Jumpers
Description Jumper
Position
Input Voltage
JP11
A-E and B-D (120 VAC) or A-C and B-C (240 VAC)
Speed Feedback Selector
JP4
ARM (Armature) or TACH (Tachometer)
Armature Voltage Level
JP8
LOW (90 VDC) or HI (180 VDC)
Current Feedback Range
JP9
No Jumper (2.6A) A (5.5A) B (7.5A)
Tachometer Feedback Range
JP3
LOW (6.5-17.4 VDC) or HI (60-160 VDC)
(Note: feedback range is based on tachometer output at maximum motor speed)
8.2 Potentiometer
Descriptions
1. Acceleration Time (ACCEL) and Deceleration Time (DECEL). Adjust the ACCEL and DECEL
potentiometers clockwise to increase the linear acceleration and deceleration times (.3-30 seconds).
2. Maximum Speed (MAX. SPEED) and Minimum Speed (MIN. SPEED). These potentiometers adjust the
maximum speed (70-120% of motor base speed) and minimum speed (0-30% of maximum speed setting)
at which the motor will run.
3. Speed Loop Offset (OFFSET SPEED). This potentiometer is used to zero out any offsets in the speed
loop amplifier. With the door mounted speed potentiometer and drive minimum speed potentiometer
(MIN. SPEED) set to zero, adjust the OFFSET SPEED potentiometer so any remaining motor rotation is
eliminated.
4. Speed Signal Follower Gain (SPEED REF. GAIN). The Speed Signal Follower Gain should be adjusted
so the motor is at its rated voltage/speed when the door-mounted potentiometer is at its full clockwise
position.
5. Signal Follower Zero Bias (ZERO BIAS). The Signal Follower Zero Bias potentiometer should be
adjusted so the motor is at zero speed when the minimum current reference input signal (4mA) is applied.
6. Current Signal Follower Gain (CURRENT REF GAIN). The Current Signal Follower Gain should be
adjusted so the motor is at its rated voltage/speed when the maximum current reference input signal
(20mA) is applied.
7. Internal Resistance Compensation (IR COMP). The IR compensation potentiometer is used to overcome
the motor’s natural tendency to slow down as the load increases. If the motor slows down excessively as
it is loaded, adjust the IR COMP potentiometer clockwise. The speed of the motor will oscillate or ‘hunt’
if the IR COMP potentiometer is adjusted too far clockwise. If this pulsing occurs, adjust the IR COMP
potentiometer counterclockwise until the motor speed stabilizes.
Refer to Control Techniques Focus 3
™
User Guide page 20 for additional information.
10