Wheel replacement, Bearing replacement – COOK SRSH User Manual
Page 5
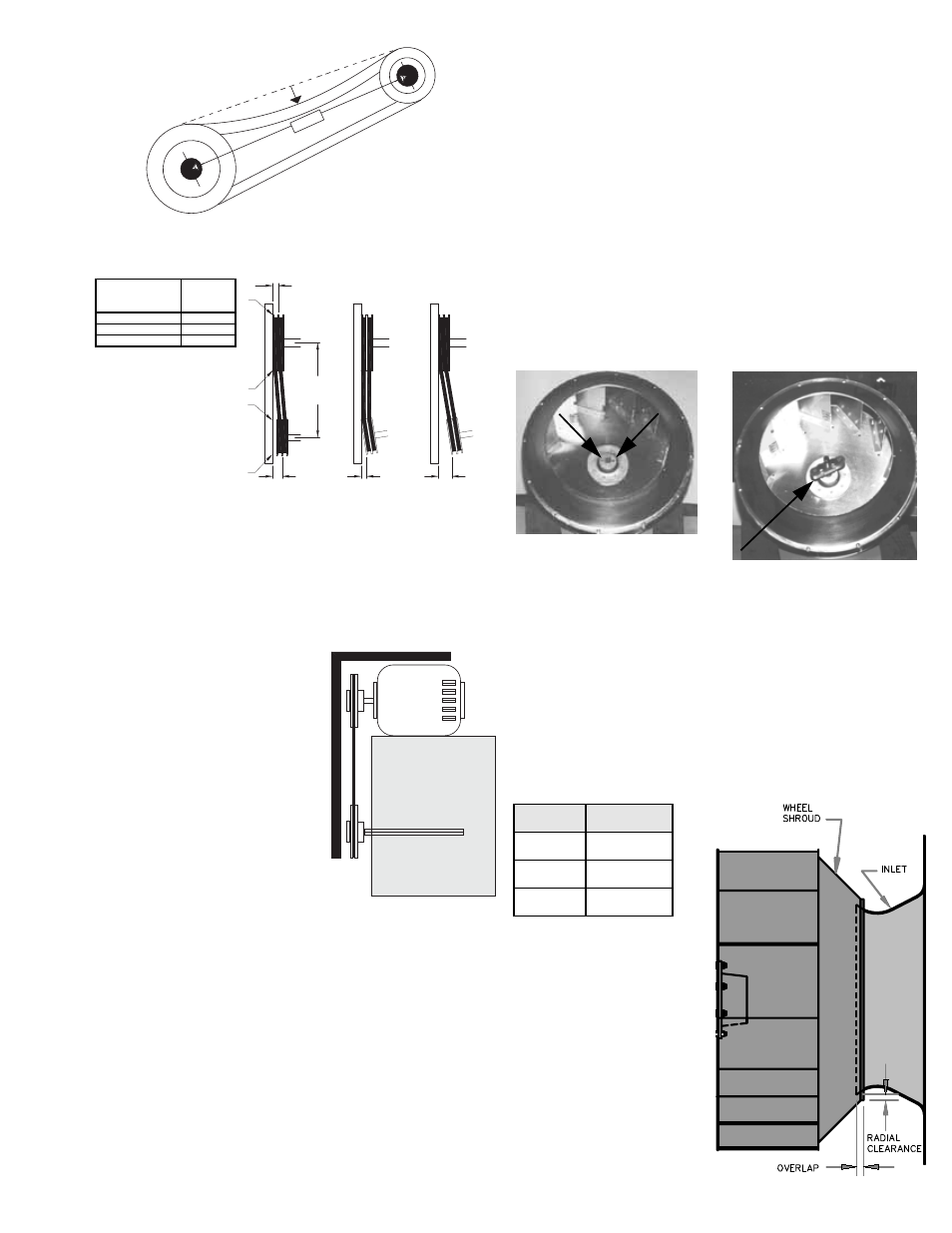
5
Wheel Replacement
a. Drill two holes approximately centered between the
shaft and the edge of the hub OD with the following
dimensions:
• 1/4" diameter
• 3/8" to 1/2" deep
• 180° apart in face of hub
b. Tap 1/4" holes to 5/16" thread with the 5/16" hole tap.
Do not drill or tap any larger than recommended.
c. Screw the puller arms into the tapped holes full depth of
threads (3/8" to 1/2" approximately). Align center of
puller with center of shaft. Make certain all setscrews in
hub (normally a quantity of two) are fully removed. Work
puller slowly to back wheel off the shaft.
Recommended Puller
Lisle No. 45000 Sterling Wheel Puller. This puller is available
at most automotive parts retail outlets.
Wheel-to-Inlet Clearance
The correct wheel-to-inlet clearance is critical to proper
fan performance. This clearance should be verified before
initial start-up since rough handling during shipment could
cause a shift in fan components. Refer to wheel/inlet draw-
ing for correct overlap.
Adjust the overlap by loosening the wheel hub and mov-
ing the wheel along the shaft to obtain the correct value.
A uniform radial gap (space between the edge of the
cone and the edge of the inlet) is obtained by loosening the
inlet cone bolts and repositioning the inlet cone.
Size
Overlap
60 - 165
3/16”
180 - 245
1/4”
270
5/16”
Above - Drilled hole placement.
Right - Wheel puller.
c. Lock the motor plate adjustment bolts in place.
d. Ensure pulleys are properly aligned. Refer to Figure 2.
Pulley Alignment
Pulley alignment is adjusted by loosening the motor pul-
ley setscrew and by moving the motor pulley on the motor
shaft. Figure 2 indicates where to measure the allowable
gap for the drive alignment tolerance. All contact points
(indicated by WXYZ) are to have a gap less than the toler-
ance shown in the table. When the pulleys are not the same
width, the allowable gap must be adjusted by half of the dif-
ference in width. Figure 3 illus-
trates using a carpenter’s square
to adjust the position of the motor
pulley until the belt is parallel to the
longer leg of the square.
Bearing Replacement
The fan bearings are pillow block
type ball bearings.
a. Remove the old bearing.
b. Remove any burrs from the
shaft by sanding.
c. Slide new bearings onto the
shaft to the desired location
and loosely mount bearings
onto the bearing support. Bearing bolts and setscrews
should be loose enough to allow shaft positioning.
d. Correctly position the wheel and tighten the bearing
bolts securely to the bearing support.
e. Align setscrews bearing to bearing and secure tightly
to the shaft.
NOTICE! Never tighten both pairs of setscrews
before securing bearing mounting bolts. This may dam-
age the shaft.
f. Inspect the wheel position again. If necessary, readjust
by loosening the bearing bolts and setscrews and
repeat from step e.
1 foot
1/4 inch
Figure 1
Tolerance
Center Distance
Maximum
Gap
Up thru 12”
1/16”
12” up through 48
1/8”
Over 48”
1/4”
OFFSET
ANGULAR
OFFSET/ANGULAR
A
W
X
Y
Z
B
CENTER
DISTANCE
(CD)
GAP
GAP
Figure 2
Figure 3