Rotation, Final steps, Operation – COOK UCIC User Manual
Page 5: Inspection, Wiring installation, Wheel rotation, Final installation steps, Start up
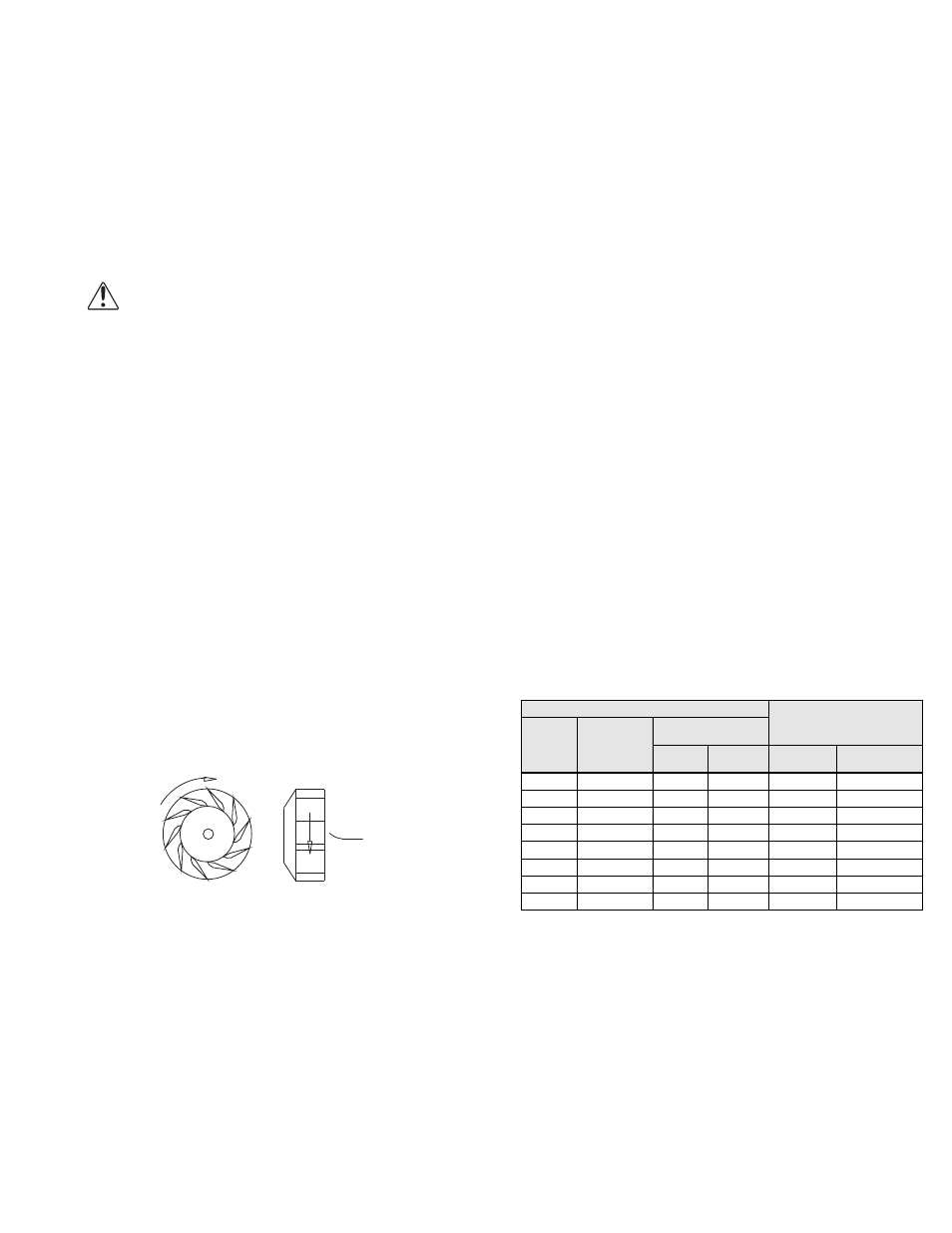
5
Wiring Installation
All wiring should be in accordance with local ordinances
and the National Electrical Code, NFPA 70. Ensure the
power supply (voltage, frequency, and current carrying
capacity of wires) is in accordance with the motor name-
plate.
Leave enough slack in the wiring to allow for motor
movement when adjusting belt tension. Some fractional
motors have to be removed in order to make the connec-
tion with the terminal box at the end of the motor. To
remove motor, remove bolts securing motor base to power
assembly. Do not remove motor mounting bolts.
Follow the wiring diagram in the disconnect
switch and the wiring diagram provided with
the motor. Correctly label the circuit on the
main power box and always identify a closed
switch to promote safety (i.e., red tape over a
closed switch).
Wheel Rotation
Test the fan to ensure the rotation of the wheel is coun-
ter-clockwise as viewed from the drive side of the wheel.
115 and 230 Single Phase Motors
Fan wheel rotation is set correctly at the factory. Chang-
ing the rotation of this type of motor should only be
attempted by a qualified electrician.
208, 230, and 460, 3 Phase Motors
These motors are electrically reversible by switching
two of the supply leads. For this reason, the rotation of the
fan cannot be restricted to one direction at the factory. See
Wiring Diagrams on page 4 for specific information on
reversing wheel direction.
NOTICE! Do not allow the fan to run in the wrong
direction. This will overheat the motor and cause seri-
ous damage. For 3-phase motors, if the fan is running
in the wrong direction, check the control switch. It is
possible to interchange two leads at this location so
that the fan is operating in the correct direction.
Final Installation Steps
a. Inspect fasteners and setscrews, particularly fan
mounting and bearing fasteners, and tighten accord-
ing to the recommended torque shown in the table
Recommended Torque for Setscrews/Bolts.
b. Inspect for correct voltage with voltmeter.
c. Ensure all accessories are installed.
Operation
Pre-Start Checks
a. Lock out all the primary and secondary power
sources.
b. Ensure fasteners and setscrews, particularly those
used for mounting the fan, are tightened.
Tubular Centrifugal Wheel Rotation
c. Inspect belt tension and pulley alignment.
d. Inspect motor wiring.
e. Ensure belt touches only the pulley.
f. Ensure fan and ductwork are clean and free of debris.
g. Inspect wheel-to-inlet clearance. The correct wheel-to-
inlet clearance is critical to proper fan performance.
h. Close and secure all access doors.
g. Restore power to the fan.
Start Up
Turn the fan on. In variable speed units, set the fan to its
lowest speed and inspect for the following:
• Direction of rotation.
• Excessive vibration.
• Unusual noise.
• Bearing noise.
• Improper belt alignment or tension
(listen for squealing)
.
• Improper motor amperage or voltage.
NOTICE! If a problem is discovered, immediately
shut the fan off. Lock out all electrical power and check
for the cause of the trouble. See Troubleshooting.
Inspection
Inspection of the fan should be conducted at the first 30
minute, 8 hour and 24 hour intervals of satisfactory opera-
tion. During the inspections, stop the fan and inspect as per
the Conditions Chart.
30 Minute Interval
Inspect bolts, setscrews, and motor mounting bolts.
Adjust and tighten as necessary.
8 Hour Interval
Inspect belt alignment and tension. Adjust and tighten as
necessary.
24 Hour Interval
Inspect belt tension, bolts, setscrews, and motor mount-
ing bolts. Adjust and tighten as necessary.
Recommended Torque for Setscrews/Bolts
Setscrews
Hold Down Bolts
Size
Key Hex
Across
Flats
Recommended
Torque
Min.
Max.
Size
Wrench
Torque
No.10
3/32”
28
33
3/8”-16
240
1/4”
1/8”
66
80
1/2”-13
600
5/16”
5/32”
126
156
5/8”-11
1200
3/8”
3/16”
228
275
3/4”-10
2100
7/16”
7/32”
348
384
7/8”-9
2040
1/2”
1/4”
504
600
1”-8
3000
5/8”
5/16”
1104
1200
1-1/8”-7
4200
3/4”
3/8”
1440
1800
1-1/4”-7
6000
(IN/LB.)