Safety information and guidelines for use, Parallel log stroke gripper rgp – ROHM RGP Long stroke gripper User Manual
Page 5
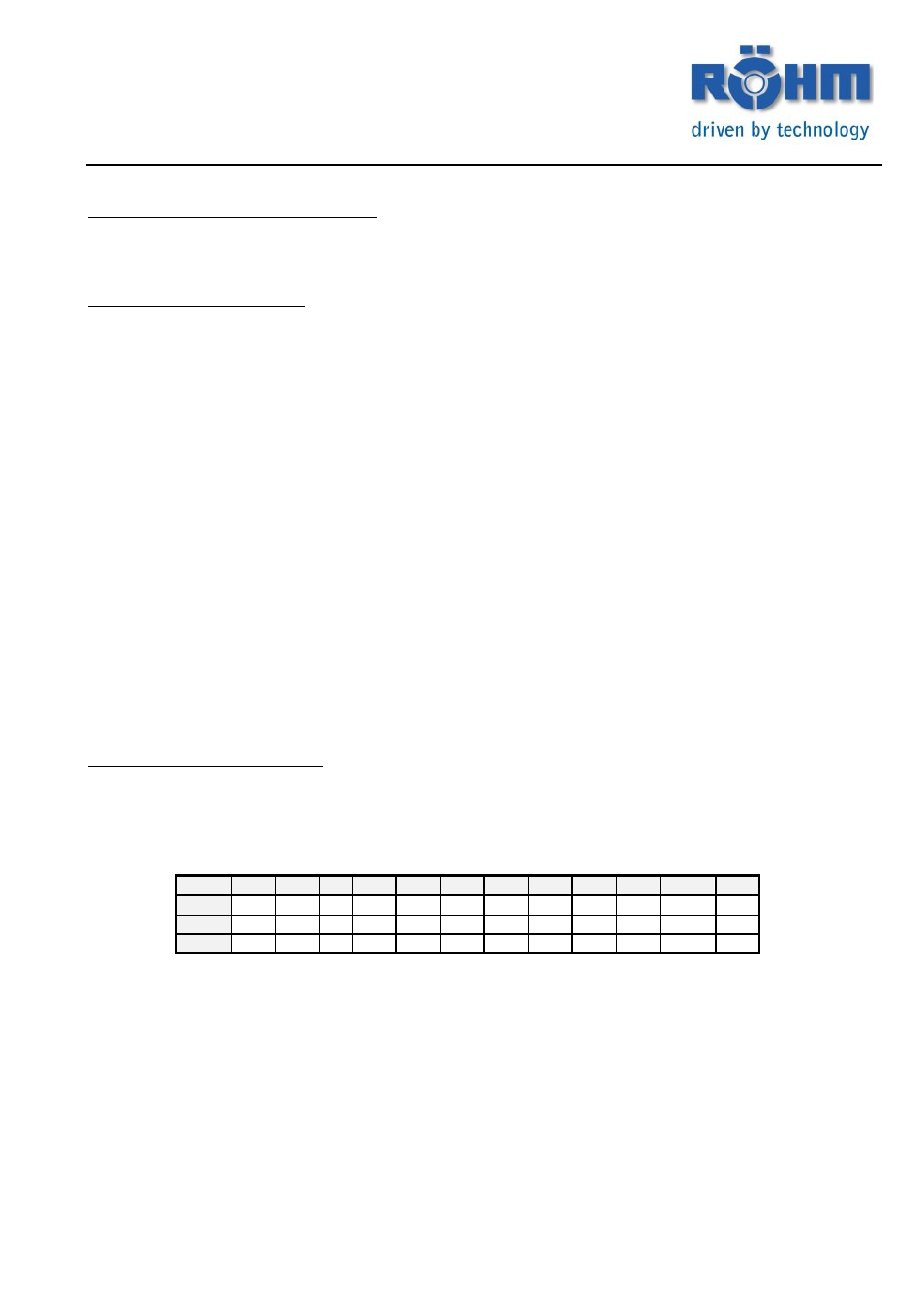
Safety information and guidelines for use
Parallel Log Stroke Gripper RGP
Id.1140167 Operating Instructions RGP
Röhm-Tool GmbH, Röhmstr. 6, 89407 Dillingen/Donau, GERMANY, Tel. (49)9071/508-0
Page
5 of 14
5. Stability of the workpiece to be clamped
To ensure that the workpiece can be clamped under the load forces which occur, the clamped material
must be strong enough to withstand the gripping force.
Non-metallic materials such as plastic, rubber, etc. may only be clamped after being tested or with special care!
6. Installing and setting-up work
Clamping movements and, where applicable, setting movements, involve short travel distances under the influence
of what are sometimes powerful forces in short times.
Before carrying out any mounting or setting up work, therefore, the drive units provided for actuating
the gripper must always be switched off first. If, however, the clamping movement is required during
the setting operation, the following instructions must be complied with for clamping travel distances of
over 4 mm:
- The attachment of a permanent or temporary workpiece holding device to the equipment, or
- an independently actuated holding device has to be fitted,
or
-a workpiece loading mechanism is required,
or
- require that the setting work is carried out in hydraulic, pneumatic and/or electric jog mode (corresponding control
must be possible!)
This type of auxiliary setting equipment depends basically on the machining system used and may have to be pro-
cured separately.
The machine owner/user is responsible for ensuring that the movement of the clamping equipment does not cause
any danger to persons throughout the entire clamping process. To this end, 2-hand controls for clamp initiation or –
better still – suitable safety equipment should be provided.
7. Fastening and replacing screws
If screws are replaced or loosened, defective replacement or fastening may lead to a hazard for persons and ob-
jects. For this reason, the corresponding torque recommended by the manufacturer for the screw and the screw
quality has to be used for all fastening screws as a matter of principle, unless explicitly stated otherwise.
The following tightening torque table applies for the common sizes M5 - M24 of qualities 8.8, 10.9 and 12.9:
Qual. M5
M6
M8 M10 M12 M14 M16 M18 M20 M22 M24
8.8
5,5
9,5
23 46
80
130 190 270 380 510 670
Nm
10.9
8,1
13
33 65
110 180 270 380 530 720 960
Nm
12.9
9,5
16
39 78
140 220 330 450 640 860 1120
Nm
All data in Nm
For this reason, the corresponding torque recommended by the manufacturer for the screw and the screw quality
has to be used for all fastening screws as a matter of principle, unless explicitly stated otherwise.
All fastening screws, which on account of their useful purpose have to be unscrewed and tightened again subse-
quently (e.g. for refitting work), have to be covered with an anti-seize agent (grease paste) in the thread area and
the head contact area in intervals of six months