Servicing, maintenance of the parallel gripper, Maintenance and service life – ROHM RGP Long stroke gripper User Manual
Page 10
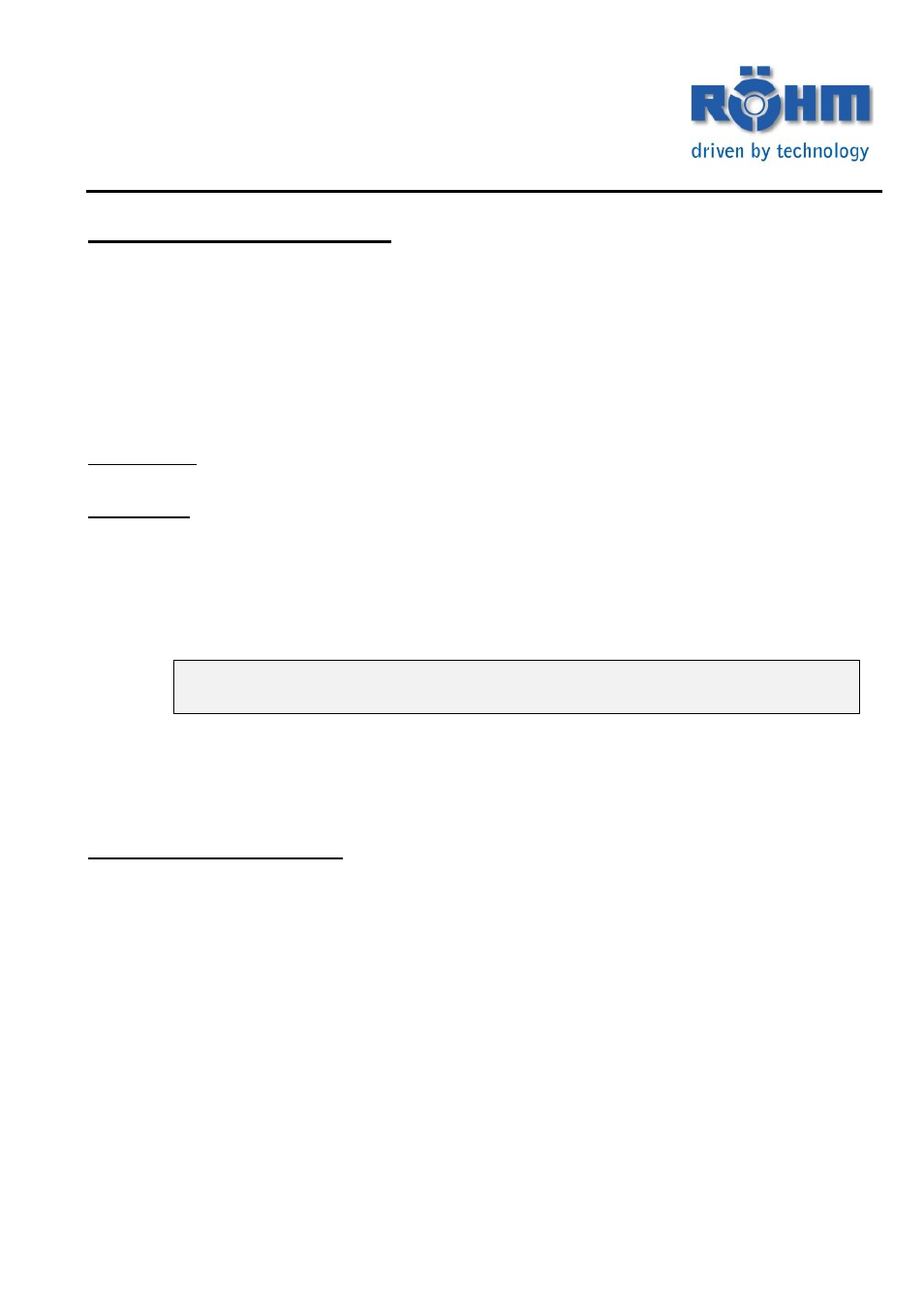
Servicing, Maintenance of the parallel gripper
Parallel Long Stroke Gripper RGP
Id.1140167 Operating Instructions RGP
Röhm-Tool GmbH, Röhmstr. 6, 89407 Dillingen/Donau, GERMANY, Tel. (49)9071/508-0
Page
10 of 14
Maintenance and service life:
The service condition of the gripper has a critical influence on its operation, clamping force, accuracy
and service life.
The gripper undergoes basic lubrication at the factory using special grease Id.1096752 Klueberplex
BEM 41-132.
Service life for normal use without preventive maintenance:
5 million cycles
Service life for normal use with preventive maintenance:
10 million cycles
Recommendation for preventive maintenance:
For normal use:
Lubrication/Cleaning: Every 2 million cycles or once per year.
For heavy use:
Lubrication/Cleaning: Every 1 million cycles or every six months using the grease nipple.
To be able to lubricate the gripper, a grease nipple must be installed at the central lubrication connection and this
must be used for the lubrication.
The grease nipple can also be positioned where it can be greased best via the direct connections and by using an
adapter plate. One must, however, pay attention that two central lubricating connections on the gripper are fitted
with a separate grease nipple. This ensures that the guides of the steering racks are supplied with lubricant
Note:
To achieve optimum lubrication, the start of the lubrication must co-incide with the
open position stage of the gripper.
Although the chuck is sealed hermetically, lubricant may seep out in the case of great internal pressure. This can be
caused by too frequent greasing of the gripper. Seeping lubricant, in particular in the area of the intermediate jaws
indicate over-lubrication.
If the lubricant seeps there every time lubrication is carried out, the lubricating intervals can be omitted for a short
time, resp. can be extended.
Lubricating via the central lubrication:
To retain the function and quality of the gripper it must be lubricated at regular intervals.
Requirement: there are no dosing valves installed in the gripper; the central lubrication must be provided by the
machine manufacturer dosed for each connection.
Lubricant:
Lubricating oil VG 220 DIN 51519
Semi-fluid greases of NLGI-classes 000; 00
With a worked penetration of 400-430
Full cleaning with taking the gripper apart approx. every 2000-3000 operating hours.
Basic lubrication: Special grease Id. 1096752 Klueberplex BEN 41-132
Dosing volume of 10 mm
3
each per lubricating impulse with 4 impulses per operating hour,
+ with an impulse duration of at least 3 sec.,
+ with an impulse pressure between 12 and 20 bar,
+ with an impulse interval of at least 5 sec.,
+ with an impulse interval pressure of max. 0.8 bar at the input of the dosing valves
+ with a lubricant with ISO designation C GLP 68 DIN 51502 or with viscosity class VG 220 DIN 51519
triggered (these data apply to V
OGEL
dosing units)