Servicing, maintenance of the parallel gripper – ROHM RGP Long stroke gripper User Manual
Page 11
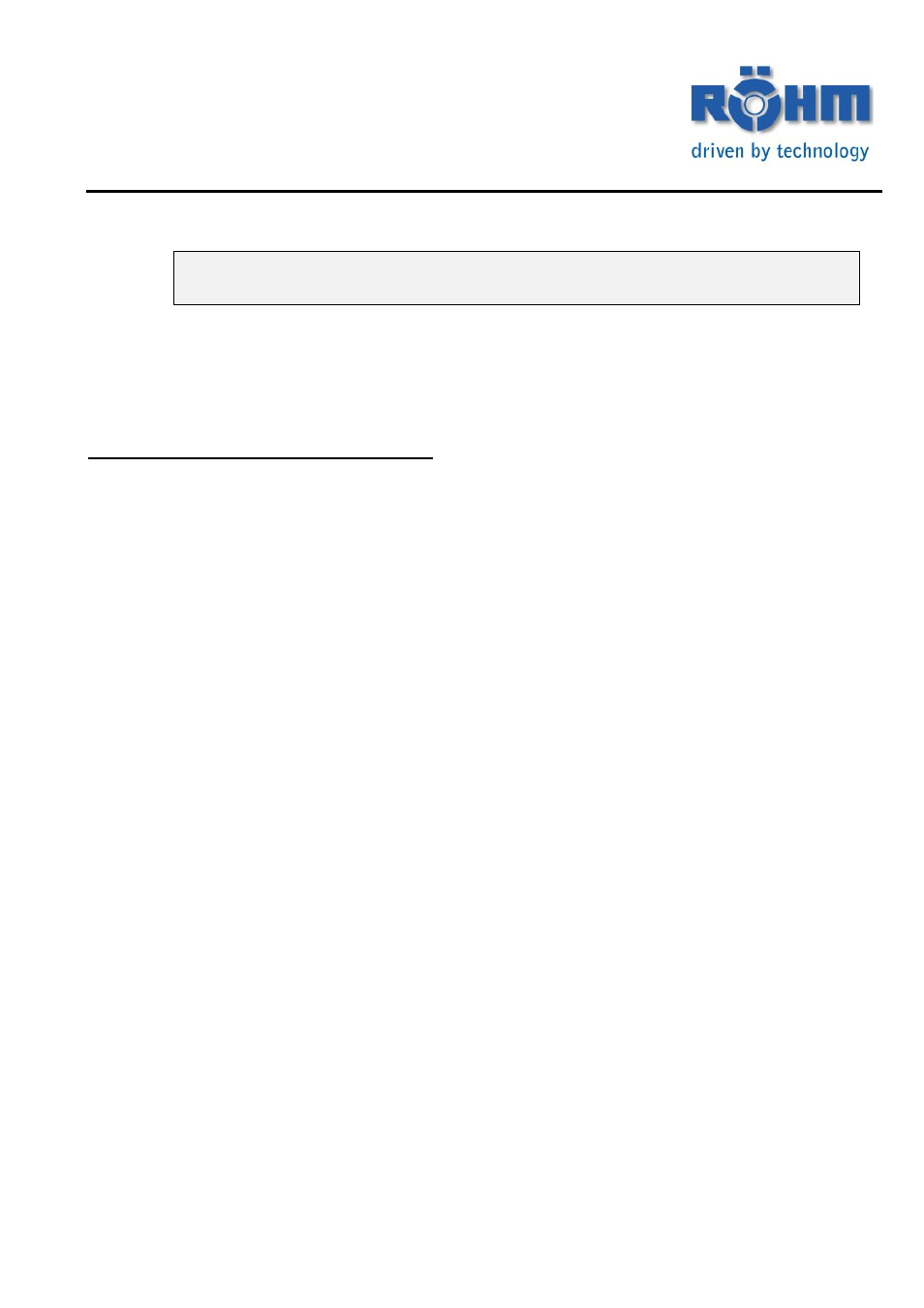
Servicing, Maintenance of the parallel gripper
Parallel Long Stroke Gripper RGP
Id.1140167 Operating Instructions RGP
Röhm-Tool GmbH, Röhmstr. 6, 89407 Dillingen/Donau, GERMANY, Tel. (49)9071/508-0
Page
11 of 14
The steering rack guides are thereby supplied with lubricant.
Note:
To achieve optimum lubrication
,
the start of the lubrication impulses must co-
incide with the open position stage of the gripper
.
Although the chuck is sealed hermetically, lubricant may seep out in the case of great internal pressure. This can be
caused by continuously added, unconsumed lubricant. Seeping quantities of lubricant, in particular in the area of the
intermediate jaws indicate over-lubrication.
If the lubricant seeps there every time the central lubrication is activated, the lubricating impulses can be interrupted
for the duration of an 8-hour shift.
Dismantling and assembling a gripper:
Important: It is essential that you observe the safety information
1) Remove the pressure lines
2) Undo the screws
Pos.23, dismantle the cylinder pin Pos.38. Now you can remove the intermediate jaw.
3) Remove the screws Pos.28, dismantle the cylinder pin Pos.39. The wiper blade Pos.12 can then be re-
moved. Remove the sealing ring Pos.45.
4) Remove the screws Pos.24 and remove the cover Pos.8.
5) Undo the screw Pos.21 and remove it. The piston disc Pos.4 can now be removed rearwards, together with
the piston rod Pos.5. The steering rack Pos. 2 together with the carrier Pos.7 can also be pulled forwards
out of the guide. Careful! The steering rack on the other side is switched co-rotating to the centre via a gear
wheel Pos. 9 (pay attention to the positions of the steering rack)
6) Pull the gear wheel bearing Pos.10 from the body Pos. 1 with the help of a pin package. The gear wheel
can be removed.
7) Turn the set screw Pos.33 back by about 3mm and remove the sockets Pos.6 from the body Pos.1.
8) Remove all the seals
9) Clean all the parts thoroughly and check the parts for signs of wear or defects
10) Replace all the seals
The assembly process is the same as above but in reverse.
Pay special attention to the numbering and position of the components. Unless specified to the contrary all the
screws are to be secured using Loctite 222 and tightened with the torque specified in DIN standards (see point II/7).
.
Version GA resp. GI with gripping force safety device:
Attention!
The cover Pos.8 with GA version and the piston disc Pos.4 with GI version can be subject to spring tension. This
presents special dangers.
Please always refer to the assembly drawing.
When dismantling the cover Pos.8 t
he spring tension (approx. 210N) must be counteracted by suitable
measures. (Clamping into a vice, then undoing the screws).
When dismantling the piston disc Pos.4 the
spring tension (approx. 210N) must be counteracted by an aux-
iliary device.