Hydraulic fan system controller: hfs – High Country Tek HFS User Manual
Page 10
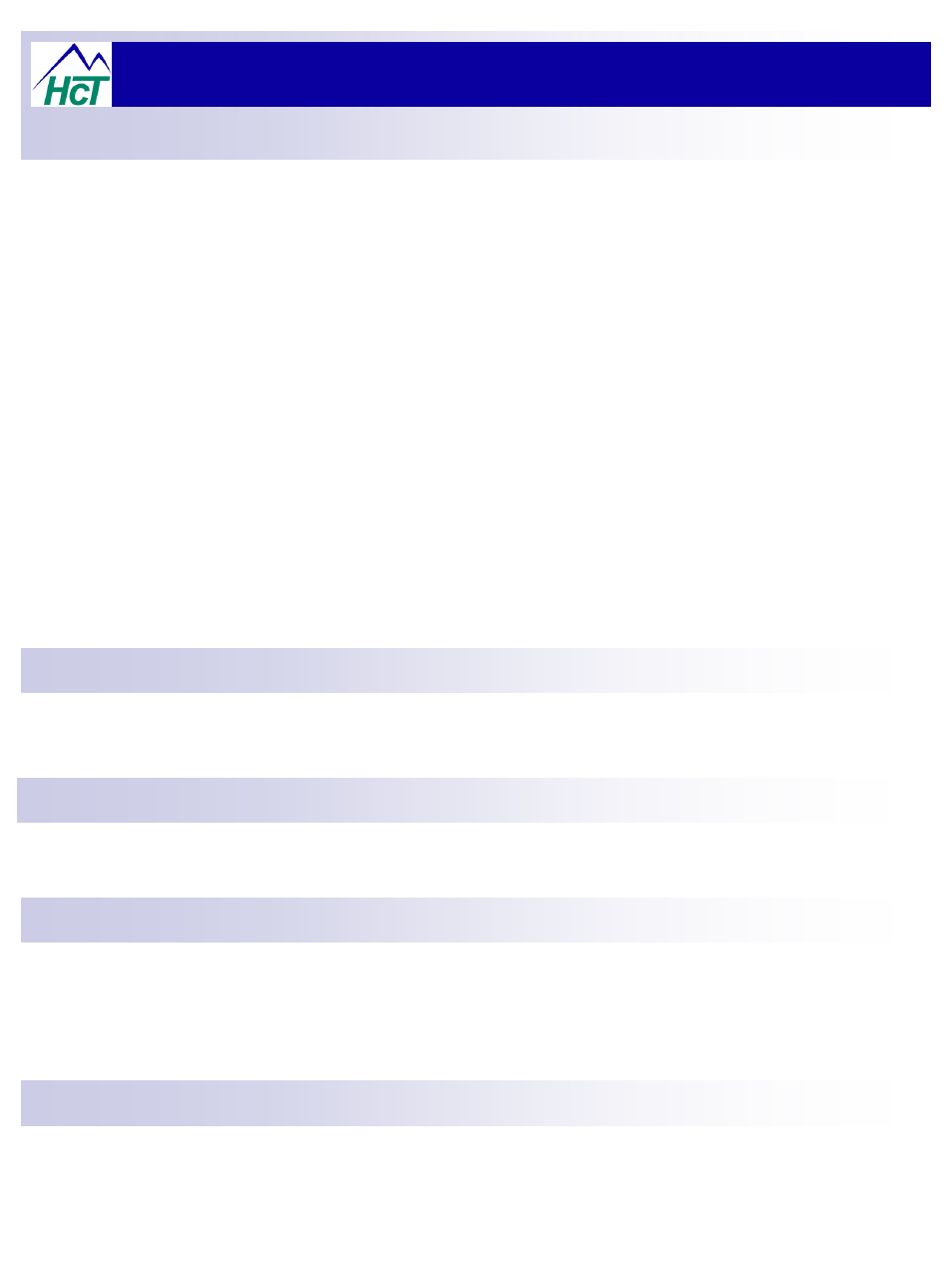
Hydraulic Fan System Controller: HFS
A variable current output is used for driving a proportional valve to control the fan speed.
BOTH wires from the valve coil must be connected to the controller where indicated by „+Prop Valve O/P‟ and „-Prop
Valve O/P‟.
The output is fully protected against shorted or mis-wired coils with errors being both indicated locally on the
associated LED and annunciated on the controller software if the program is running on a PC connected to the unit.
Shorted coils or connection wires are detected only when the controller tries to drive the coil and is indicated with a
RED FLASHING output LED.
Open circuit coils or connection wires are detected only when the controller tries to drive the coil and is indicated with
a GREEN FLASHING output LED.
The proportional valve coil selected must be capable of withstanding the power supply's maximum voltage or the user
must set the maximum output current ( I Max ) to a safe value.
User adjustable minimum current ( I Min ) and selectable PWM frequency ( 31 to 250 Hz ) allows tuning for smoothly
starting the fan from a stop.
The proportional output is rated for approx. 3A coil current maximum at the connected supply voltage.
The software allows user selection of driving normally open and normally closed proportional valves.
For data and integrity protection, the controller and proportional output is turned off if the units internal temperature
sensor temperature exceeds 80 C ( 176 F ).
This is called „ Max Vlv Current %‟ in the software and allows current to be adjusted from 0 – 100 % PWM output.
If Max Valve Current is set to zero (0) all other settings will also go to zero.
The user programmable ramp Up and Down times are applied to limit the controllers rate of change in output current
to a value that prevents damaging the hydraulic system components and the fan blades.
The ramp rate is set in seconds (s) for a full scale current output change in the range of 1 to 10 seconds.
This ramp time should be set low enough not to interfere with the temperature control loop response but high enough
to give smooth system operation.
The set-up software allows the dither frequency ( PWM frequency ) to be set from 31.5 to 250Hz to cater for the
known range of proportional valves that could be used for this application.
Proportional Output:
Fan MAX Speed Setting:
Fan MIN speed Setting:
Ramp Settings :
Dither Frequency Setting ( Valve Coil ):
This is called „ Min Vlv Current %‟ in the software and allows current to be adjusted from 0 – 100 % PWM output set by
„Max Vlv Current‟ above.
10