Chapter 2 installing the ldt – AMETEK 955DQ Brik LDT User Manual
Page 6
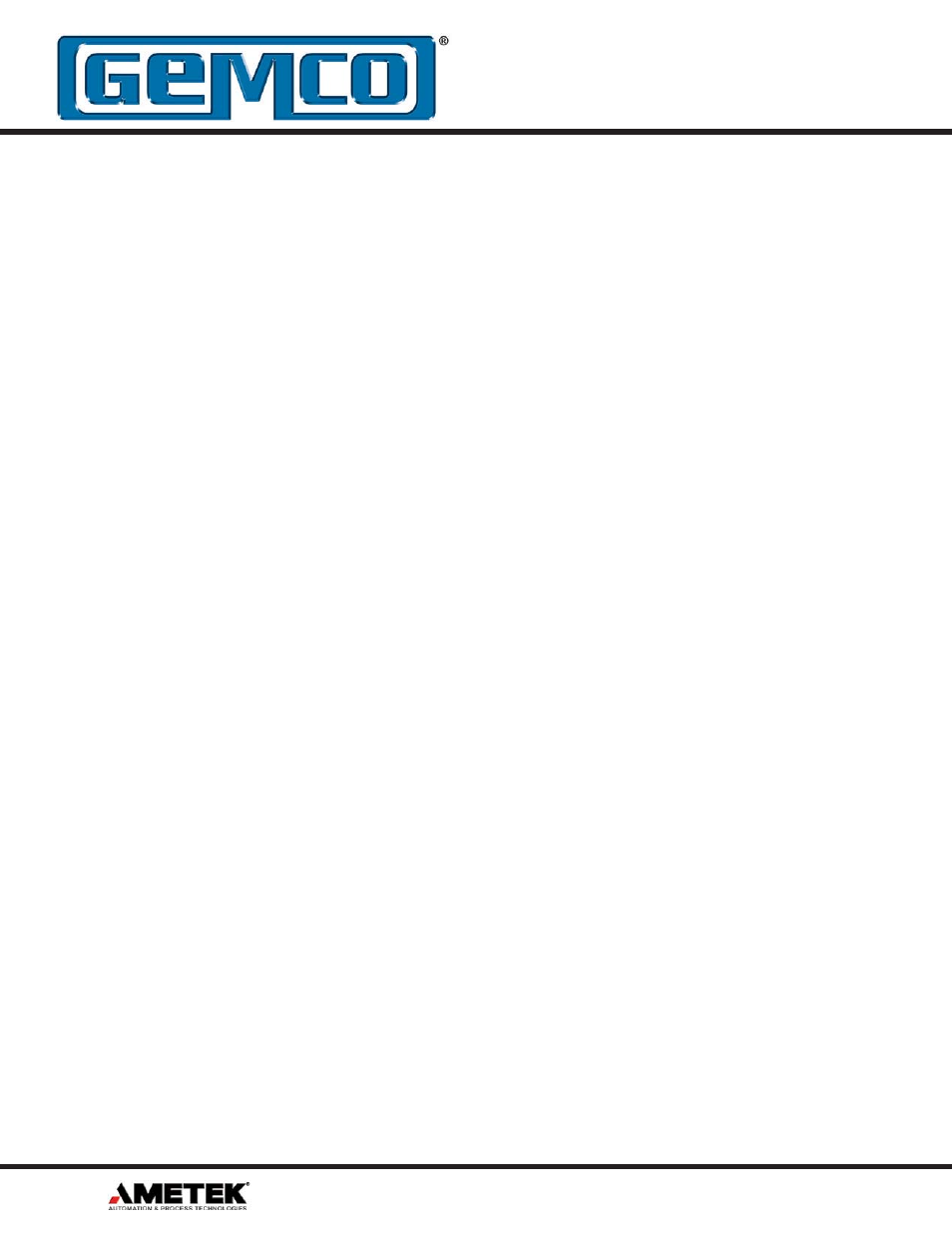
6
1080 N. Crooks Road • Clawson, MI 48017 • 800.635.0289 • 248.435.0700 • Fax 248.435.8120 • www.AMETEKAPT.com
2.1 Mounting Instructions
The Series 955DQ can be mounted vertically or
horizontally using SD0522000 mounting brackets. The
mounting brackets slide in the grooves on the lower part
of the extrusion and clamp down when tightened. It is
recommended to use one mounting bracket on each end
and every three feet in between.
Ferro-magnetic material, (material readily magnetized)
should be placed no closer than .25” from the sensing
surface of the LDT.
2.2 Mounting the Magnet Assembly
Before mounting the magnet assembly, you should
consider the following
• Ferromagnetic material should not be placed closer
that 0.25” from the LDT’s sensing surface. Failure
to do so could cause erratic operation. Non-ferrous
materials, such as brass, copper, aluminum,
nonmagnetic stainless steel or plastics, can be
in direct contact with the magnet assembly and
sensing surface without producing any adverse
results.
• Make sure that the magnet is located within
the LDT’s active stroke area. Captive magnet
assemblies should be positioned so that they can
move freely over the entire area of the active stroke
without binding or pushing on the extrusion. Non-
captive magnet assemblies should be situated so
that the magnet is no further than 3/8” from the
sensing surface at any point in the floating magnet
assembly’s movement.
• When using the Floating Magnet assembly
(SD0522100), the magnet should be installed within
3/8” of the sensing surface. The magnet assembly
should also be installed in such a manner that
it remains an even distance from the aluminum
extrusion throughout the entire stroke. Improperly
installed magnets can result in output signal non-
linearity.
Chapter 2 Installing the LDT