Van Air Systems FR-800 User Manual
Page 13
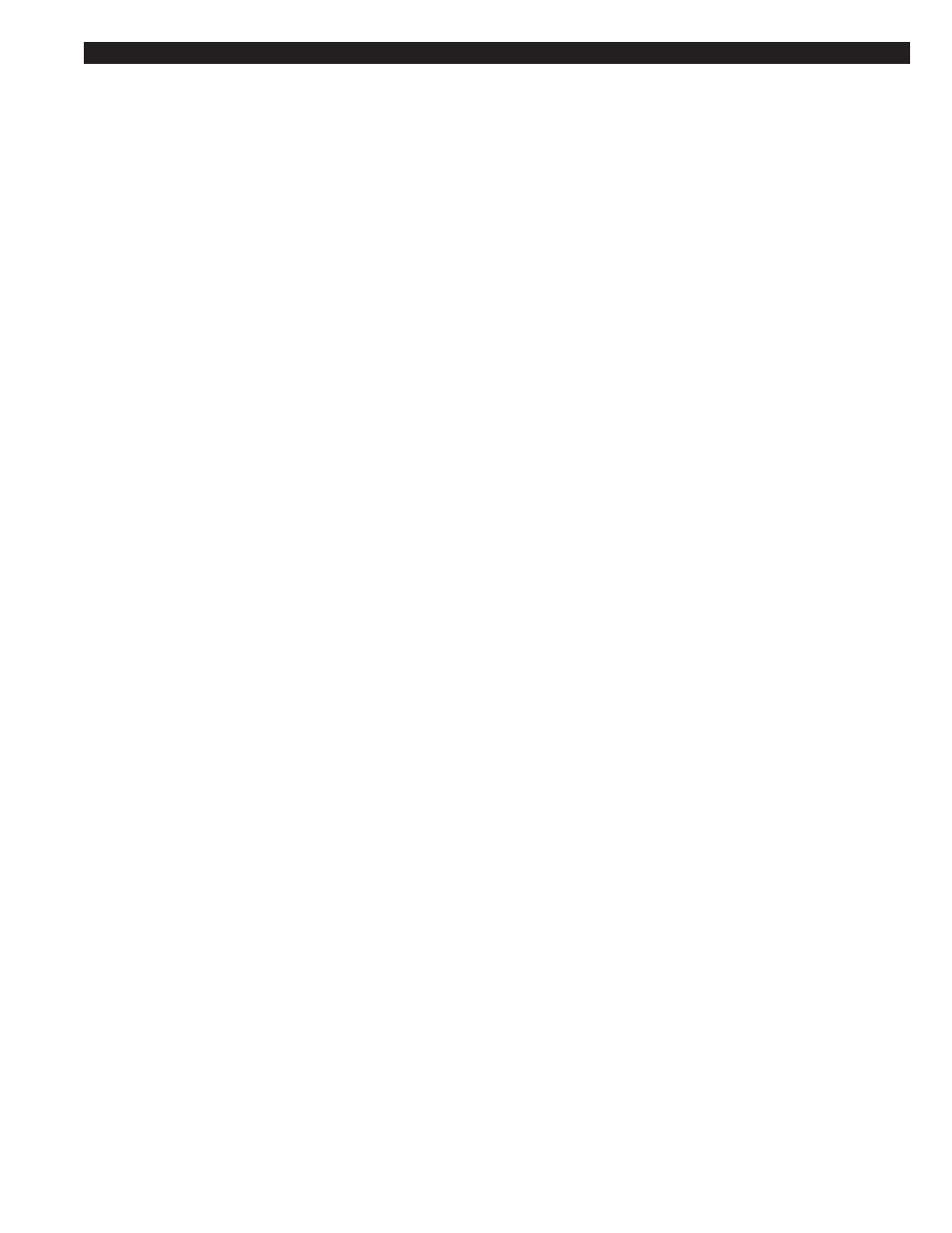
PAGE 13
10.1 TROUBLESHOOTING
The following check list should be used as a guideline for troubleshooting problems. Each of the topics will reference other sections in this
manual for further information.
IS THE POWER ON?
Check the main power source. Make sure the Power switch is in
the
ON position.
IS THE SYSTEM PRESSURIZED?
The dryer system is designed to operate at 60 to 175 psig.
Check to make sure the air supply was connected to the dryer
system inlet.
Check the Differential Pressure indicator on the prefilter. If the
needle is in the RED zone, replace the element.
IS THE DRYER CYCLING?
• IS THE FAILURE TO SWITCH ALARM ACTIVATED?
If the dryer system is not cycling the FAILURE TO SWITCH
ALARM should be activated. The dryer system should be
checked to determine the cause of switching failure.
• IS THERE CONTROL AIR PRESSURE, 60 PSIG MINIMUM?
Make sure that the dryer system inlet pressure is above 60 PSIG.
Replace control air filter element. Reference
SECTION 9.4 for
element replacement instructions.
• IS THE Y-STRAINER PLUGGED?
If the Y-strainer is clogged, their may not be enough control air
pressure to operate the dryer system. Disassemble and clean the
Y-strainer per
SECTION 9.8.
• DO THE SEPARATOR/PREFILTER, PREFILTER, &
AFTERFILTER ELEMENTS NEED CHANGED?
Check the differential pressure gauge on the prefilter and
afterfilter. If the needle on either gauge is in the red zone, replace
the element in that filter. Reference
SECTION 9.7 for details.
• ARE THE PILOT VALVES FAULTY? (SV1 & SV2)
Reference
SECTION 10.3 for procedures to check the operation
of the 3-way valves.
Replace any faulty 3-way valves.
• IS THE INLET VALVE FAULTY?
Reference
SECTION 10.4 for procedures to check the operation
of the inlet transfer valve.
Rebuild or replace the inlet valve as necessary. Reference
SECTION 11.3 for valve repair kit details.
• IS A PURGE EXHAUST VALVE FAULTY?
Reference
SECTION 10.6 for procedures to check the operation
of the purge exhaust valves.
Rebuild or replace the faulty purge exhaust valve. Reference
SECTION 11.3 for valve repair kit details.
• IS AN OUTLET CHECK VALVE FAULTY?
Reference
SECTION 10.7 for procedures to check the operation
of the outlet check valves.
If a valve is faulty, replace it.
• IS THE PURGE METERING VALVE SET PROPERLY?
Reference
SECTION 5.2 for purge metering valve settings and
procedures.
If the purge metering valve requires adjustment, follow the
procedures in
SECTION 5.2.
• IS THE SMARTRELAY FUNCTIONING?
See
SECTION 10.2 for explanation of Smart Relay operation.
IS THE VISIBLE MOISTURE INDICATOR BLUE?
Reference
SECTION 6.3 for an explanation of operation for the
moisture indicator.
• IS THE BLEED ORIFICE FITTING OR SINTERED MUFFLER ON
THE MOISTURE INDICATOR CLOGGED?
Inspect the bleed orifice fitting and the sintered filter on the back
of the moisture indicator. They can be cleaned or replaced.
• ARE THE INLET CONDITIONS WITHIN THE SPECIFICATIONS?
Reference
SECTION 3.1 for the inlet conditions of the dryer
system.
Correct the inlet conditions if necessary. Excessive inlet flow will
greatly reduce the performance of the dryer system.
• IS THE PURGE METERING VALVE SET PROPERLY? Reference
SECTION 5.2 for purge metering valve settings and procedures.
Adjust purge metering valve as required.
• WAS THE DESICCANT INSTALLED?
Is there desiccant in the towers. Reference
SECTION 9.3 for
desiccant replacement procedures.
• IS THE DESICCANT CONTAMINATED WITH LUBRICANTS?
Check the condition of the desiccant bed. If the bed is
contaminated with lubricants, replace the desiccant following the
procedures in
SECTION 9.3.
• IS THE DESICCANT CONTAMINATED WITH MOISTURE?
If the dryer system was operated under excessive inlet conditions,
the desiccant bed may be saturated with liquid moisture. Check
upstream equipment such as aftercoolers. Check the actual
inlet conditions, correct them and condition the bed following the
procedures in
SECTION 5.5.
• IS THE SEPARATOR/PREFILTER DRAINING PROPERLY?
Manually override the drain on the separator/prefilter to ensure it
is not flooded.
• IS THE PREFILTER DRAINING PROPERLY?
Manually override the drain on the prefilter to ensure it is not
flooded.
• IS THE FAN MOTOR ON THE PRECOOLER OPERATING?
Check the regulator setting for the air supply to the motor. See
SECTION 5.4 for details. Check the air motor and repair or
replace as necessary.
• ARE THE PURGE MUFFLERS CLOGGED?
Check the tower pressure gauge during the regeneration cycle. If
the tower pressure is above 5 PSIG, replace the purge mufflers.
See
SECTION 11.3 for part number.
• IS THE PRECOOLER DIRTY?
Inspect the outside of the core for dirt and /or oil deposits. If the
core is dirty, clean it per
SECTION 9.5. If the outside of the core
is clean, the inside may be coated with oil. If the inside is coated
with oil the precooler will have to be cleaned per
SECTION 9.6.
IS THE DEW POINT ACCEPTABLE?
TROUBLESHOOTING
SECTION 10