1 <2 quick start> 2 qucik start – Yokogawa In-Situ Gas Analyzer TDLS200 User Manual
Page 11
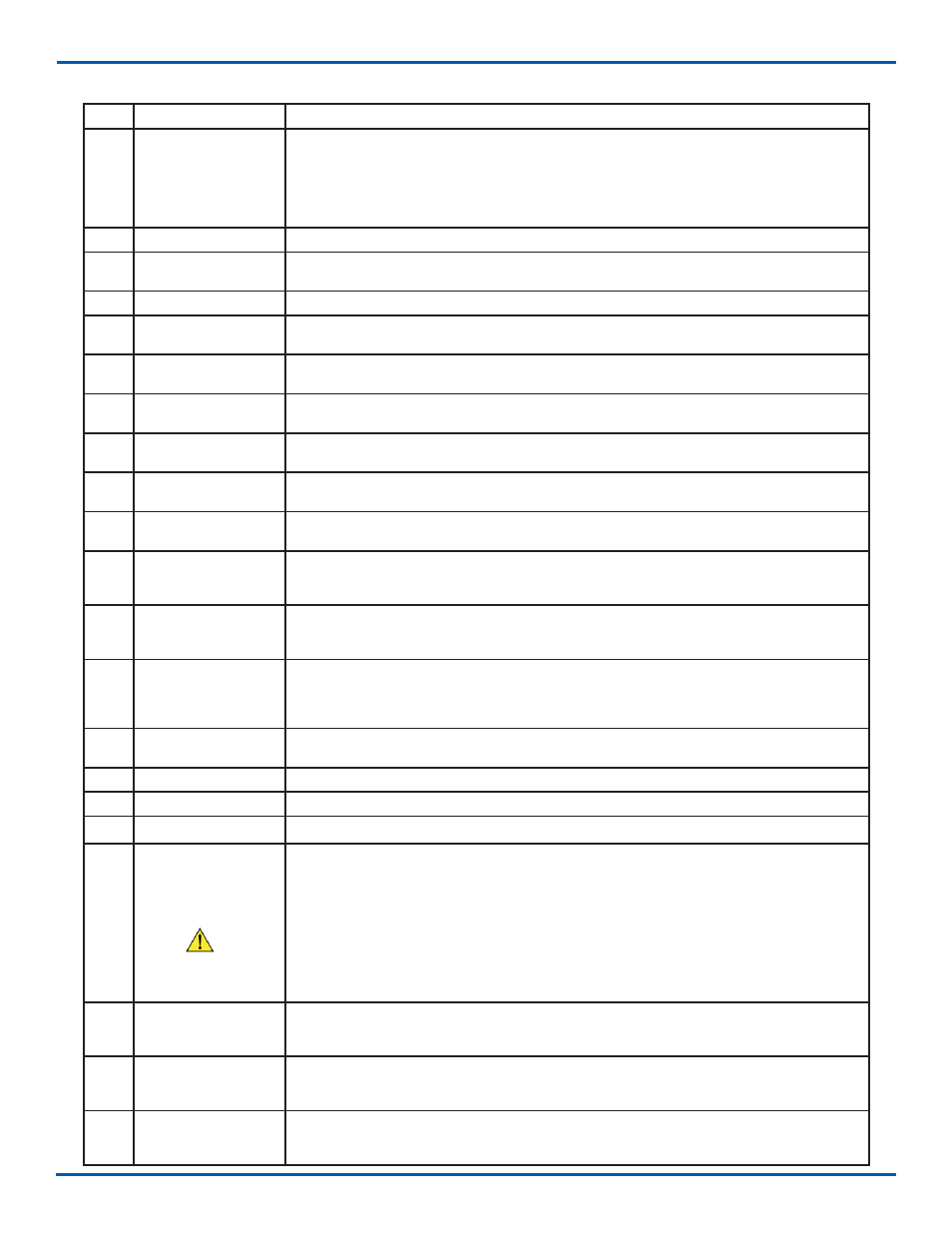
2-1
<2 QUICK START>
2 QUCIK START
Step
Title
Description
1.0
Preparation
Carefully un-pack and check equipment for any obvious damage. This includes fl anges, Cables, Power
Supplies, manuals and any other supplied options.
NOTES: There are 14 ferrules in the accessory bag for tubing-piping. The number of ferrule that are
required for actual tubing-piping are different by application. Please see tubing-piping fi gure
specifi c to project for exact detail.
1.1
Ensure the process connections match the supplied process interface.
1.2
Ensure the appropriate utilities are available and ready for connection. These may include electrical
power, nitrogen purge gas, instrument air, validation gas, etc.
1.3
Ensure you comply with any local and/or site specifi c safety requirements.
1.4
Read the appropriate sections of the Instruction Manual BEFORE starting any installation work –
Contact Yokogawa Laser Analysis Division or Local Agent if any doubts!
2.0
Installation
If separate process isolation fl anges have been provided for corrosive service, then install to the
process/stack fl ange/isolation valves.
2.1
Attach the process interface (alignment fl anges) to the site installed fl anges (or isolation valves as
appropriate).
If installing Large Aperture Optics, ensure the detect system is correctly mounted and purged to
prevent damage to the large optical element.
2.2
Carefully mount the Launch and Detect Units to their alignment fl anges using the quick connect
coupling.
2.3
Mount optional equipment such as Universal Power Supply (UPS), Universal Remote Display (URD),
Remote Interface Unit (RIU), etc.
2.4
Ambient
Temperature
The analyzer and some accessories (such as LAO, RIU, UPS, URD, alignment fl anges, etc.) are
suitable for -20 to +50oC ambient operating temperature. Accessories and Options are available to
increase these the operating conditions – please consult Yokogawa for further details.
3.0
Wiring
Ensure that all wiring will enable the analyzer launch and detect units to be freely moved from their
process location to an adjacent off-line calibration cell. This will entail the use of tray rated cables and/
or fl exible conduit and/or other suitable armored cable. Rigid conduit systems are not recommended.
3.1
Connect the appropriate electrical power supply.
• 24 VDC to TB1 on the analyzer (launch Unit) backplane. Check that the actual voltage
is >23.5VDC otherwise the SBC and other devices will not function!
• 110/240 50/60 Hz to UPS or URD, then take 24 VDC to analyzer
3.2
Connect the Launch to Detect interconnect cable (supplied with analyzer) according to the supplied
wiring detail (TB7 on the Launch and TB 13 on the Detect Unit).
3.3
Connect any analog I/O signals to the analog I/O Board. Outputs land on TB8 and Inputs land on TB9.
3.4
Connect any other equipment such as URD, Ethernet, solenoid valves, digital I/O, etc.
3.5
Check terminations and ensure all cable shields are landed per supplied wiring details.
4.0
Utilities
NOTE! – All purge, Validation Gas and other gas utility lines should be thoroughly cleaned, dried
and purged prior to connecting to the analyzer
– Failure to do so can result in serious damage to the TDLS200 or contamination to the
internal optical elements.
Connect the appropriate analyzer purge gas (nitrogen for oxygen analyzers) and make site connections
per the supplied purge gas sequence details (including any Hazardous area purge system). Start the
purge gas fl ow accordingly.
ATEX purge requires dual regulators at the inlet purge gas supply to prevent overpressure damage in
the event of a single regulator failure!
4.1
Connect the appropriate process window purge gas (nitrogen for oxygen analyzers) and make site
connections per the supplied purge gas sequence details. Start the window purge gas fl ow
accordingly – ensuring that any isolation valves are open.
4.2
Connect the appropriate analyzer on-line check gas fl ow cell gas (nitrogen for oxygen analyzers) and
make site connections per the supplied purge gas sequence details. Start the purge gas fl ow
accordingly.
4.3
Connect and check any other required utility connections (such as steam trace for heated isolation
fl anges or fl ow cells) or secondary window purges for lethal service gases. Start other utilities
accordingly.
IM 11Y01B02-11E-A 5th Edition :June 5, 2012-00