Installation – Lincoln Electric IM10090 ARC TRACKER User Manual
Page 12
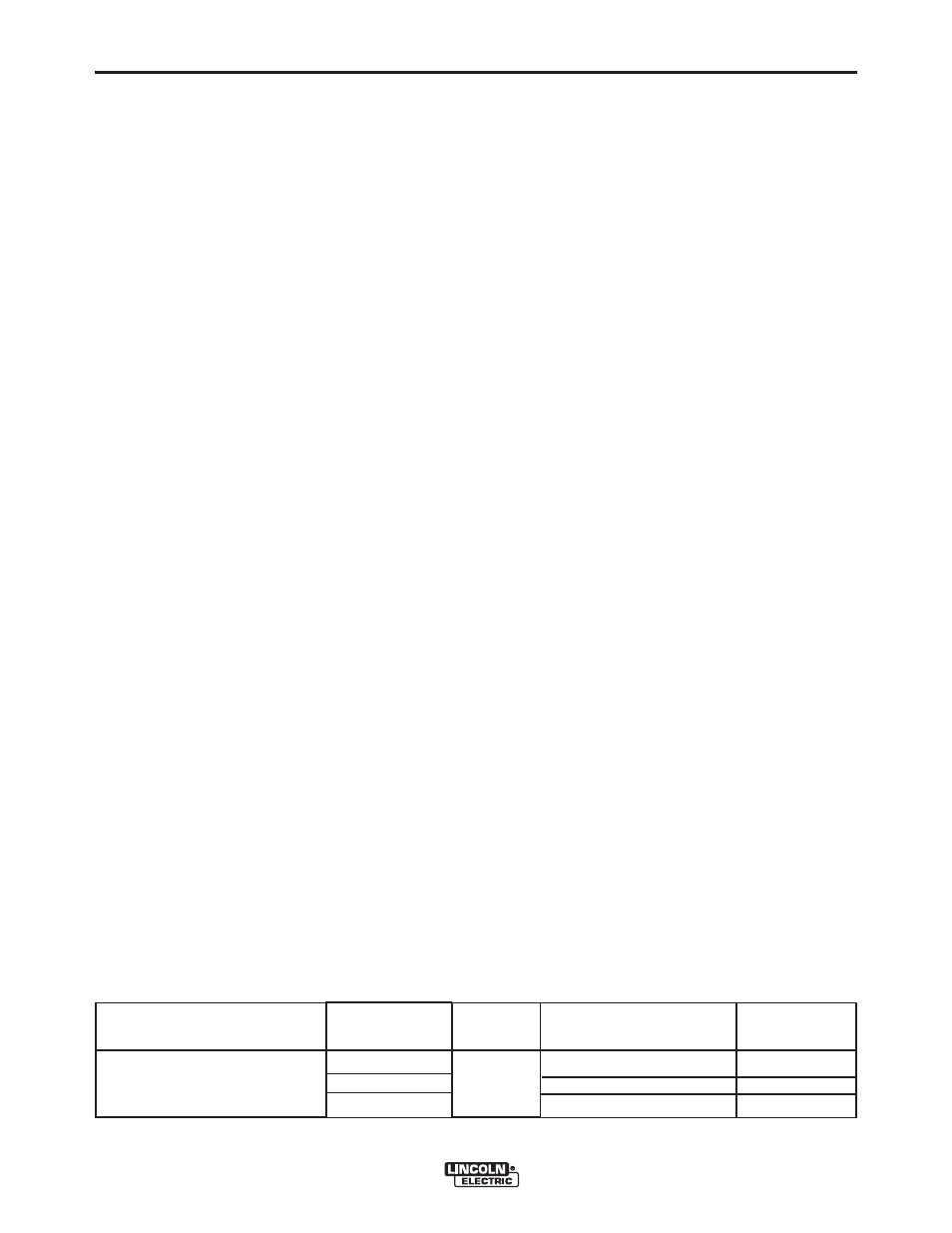
A-3
INSTALLATION
A-3
REMOTE SENSE LEAD SPECIFICATIONS
(See Figure A.1)
In order to get an accurate measurement of the true
energy going in to the weld, it is critical to get an
accurate measurement of the arc voltage. The arc
voltage sense leads are polarity specific – RED must
be connected to the positive side of the arc and
BLACK to the negative. The sense leads should be
connected as close as possible to the arc, e.g. at the
contact tip, wire feeder, etc and to the work.
PRODUCT SPECIFIC INSTRUCTIONS
Best Practices
:
Place the ARC TRACKER™ in the work circuit. This
will keep the ARC TRACKER™ at the same potential
as the work piece.
The welding current MUST flow into the left side weld
terminals (when viewing the ARC TRACKER™ from
the rear) and out of the right side weld terminals. If the
welding current does not flow through the ARC
TRACKER™ in the right direction, the unit will not
properly sense the welding current and nothing will be
displayed on the unit during welding.
See the specific power source instruction manual for
additional general guidelines on output cable connec-
tions.
SOFTWARE TOOLS
ARC TRACKER™ software tools and other docu-
ments related to the integration, configuration, and
operation of the system are available at,
www.powerwavesoftware.com
An Ethernet connection gives the ARC TRACKER™
the ability to run Power Wave Manager and
Production Monitoring™.
Power Wave Manager
• Ethernet setup and verification
• Calibration
• Production Monitoring Configuration
• User Interface Lockout
ELECTRODE CONNECTIONS
Electrode Positive (See Figure A.1)
Connect cable(s) of sufficient size and length (Per
Table A.1) to the "ELECTRODE" terminals on the
power source. Connect the other end of the electrode
cable(s) to the contact tip, wire feeder, etc. Be sure
the connection makes tight metal-to-metal electrical
contact.
WORK CONNECTIONS
Electrode Positive (See Figure A.1)
Connect cable(s) of sufficient size and length (Per
Table A.1) between the "WORK" terminals on the
power source and the ARC TRACKER™ right side
weld terminals (when viewed from the rear). Connect
cable(s) of sufficient size and length from the ARC
TRACKER™ left weld terminals to the work. Be sure
the connection to the work makes tight metal-to-metal
electrical contact.
ARC TRACKER™
Total Cable Length ft (m)
Electrode and Work Combined
0 (0) to 250 (76.2)
Number of Cables
(parallel if more than one)
1
2
3
Current in Weld
Circuit
0-500 Amps
500-750 Amps
750-1000 Amps
Cable Size
(copper) AWG
4/0 (120 mm
2
)
4/0 (120 mm
2
)
3/0 (95 mm
2
)
Duty Cycle
100%
TABLE A.1 Output Cable Guidelines
• Select the appropriate size cables per the "Output
Cable Guidelines" Table A.1. Excessive voltage
drops caused by undersized welding cables and
poor connections often result in unsatisfactory weld-
ing performance. Always use the largest welding
cables (electrode and work) that are practical, and
be sure all connections are clean and tight.
Note: Excessive heat in the weld circuit indicates
undersized cables and/or bad connections.
• Route all cables directly to the work and electrode,
avoid excessive lengths and do not coil excess
cable. Route the electrode and work cables in close
proximity to one another to minimize the loop area
and therefore the inductance of the weld circuit.
• Always weld in a direction away from the work con-
nection.