Step 7 – electrical connections, Electrical coil data, Mechanical data – Warner Electric Performance Plus Preassembled Clutch_Brake Module User Manual
Page 5: Overhung load data
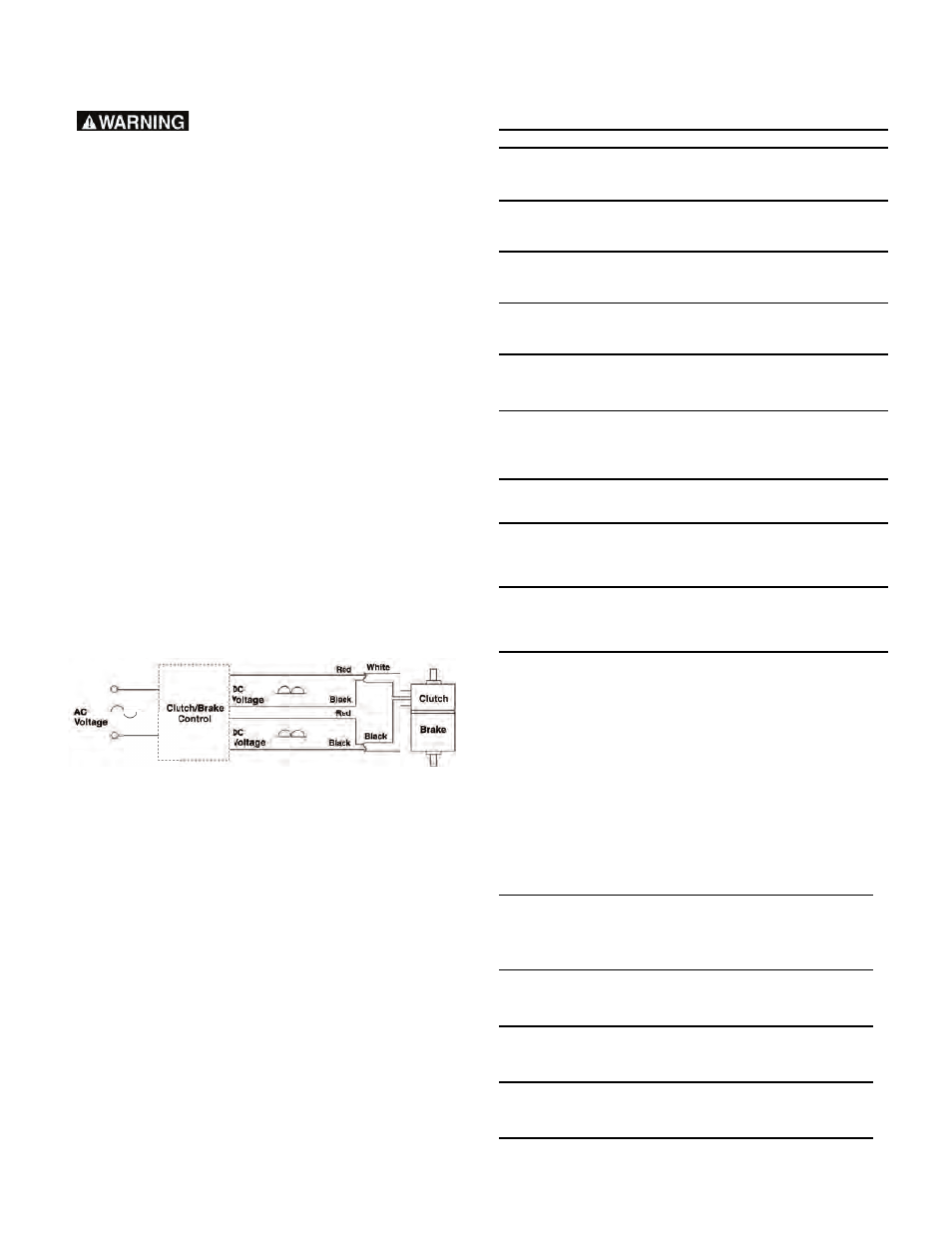
Step 7 – Electrical Connections
To avoid injury (or even death),
always make certain all power is off before at
tempting to install or service this control or
any electrical equipment.
The Unimodule is provided with one conduit
connection hole, threaded for standard 1/2"
conduit connectors. Both the clutch and the
brake lead wires are brought out through this
opening. The conduit box accessory kit, P/N
5370-101-042, provides two conduit connection
holes for standard 1/2" conduit connectors.
The clutch and brake coils operate on DC volt-
age. Warner Electric offers a full line of AC volt-
age powered controls to meet the needs of
almost every clutch/brake application. The serv-
ice and installation instructions included with
each Warner Electric control show the proper
electrical connections.
Please refer to Figure 7 for the proper
Unimodule electrical connections. Clutch leads
are identified with a white insulator sleeve.
Brake leads have a black insulator sleeve.
Figure 7
After wiring, your Performance Plus Unimodule
is now ready to operate. If your clutch/brake
control has torque control, the torque adjust
potentiometer(s) should be set for rapid and
complete load take up. Excessive slippage of
the brake or clutch can cause overheating and
premature wear. See the following pages for
technical, operating and service information.
5
Warner Electric • 800-234-3369
P-273-3 • 819-0358
Warner Electric • 800-234-3369
P-273-3 • 819-0358
Electrical Coil Data
Clutch Brake
Clutch Brake
Clutch Brake
Voltage–D.C.
90
90
24
24
6
6
Resistance
UM-50-C
452
452
31.8
26.8
1.86
1.77
(OHMS)
UM-180-C
392
309
26.7
22.8
1.80
1.54
UM-210-C
248
222
17.9
15.4
1.22
1.04
Amperes
UM-50-C
.199
.233
.755
.894
3.23
3.39
UM-180-C
.230
.291
.896
1.05
3.30
3.90
UM-210-C
.363
.405
1.34
1.56
4.90
5.78
WATTS
UM-50-C
18
21
18
21
19
20
UM-180-C
21
26
21.5
25
20
23
UM-210-C
33
36
32
37
30
35
Build Up
UM-50-C
52
53
52
53
52
53
(Milli.)
UM-180-C
72
75
72
75
72
70
UM-210-C
120
100
120
100
110
100
Decay
UM-50-C
6.2
5.0
6.2
5.0
6.5
5.0
(Milli.)
UM-180-C
12
10
12
10
12
10
UM-210-C
20
10
20
10
20
10
Mechanical Data
UM-50
UM-180
UM-210
Static Torque - lb. ft.
16
30
95
Maximum Speed - rpm
3600
3600
3600
Average Weight-lbs.
1020
10
13.2
30.6/31
2030
13
16.5
41.3/42
Inertia – WR (lb. ft.
2
)
Output
.017
.041
.231
Input
.020
.046
.188
Note: All Data Nominal
Overhung Load Data
Overhung load data is provided in this manual
for the design engineer concerned with specific
requirements in this area. The maximum allow-
able overhung load which can be applied to the
shaft of an Electro-Module may be determined
from the accompanying chart.
Overhung Load*
Distance Load is
Applied from
Maximum
Electro-Module
Housing Face
Load Rating
Size
"A" Inches
"R" Lbs.
1" - Center of Shaft
177
UM-50-C
2" - End of Shaft
123
3"
95
1" - Center of Shaft
192
UM-180-C
2" - End of Shaft
134
3"
104
1-3/8" - Center of Shaft
386
UM-210-C
2-3/4" - End of Shaft
271
4-1/8"
208
* Based on 10,000 Hour Life at 3600 RPM.