Warner Electric Electrically Released Permanent Magnet Clutch Compatible Modules User Manual
Page 2
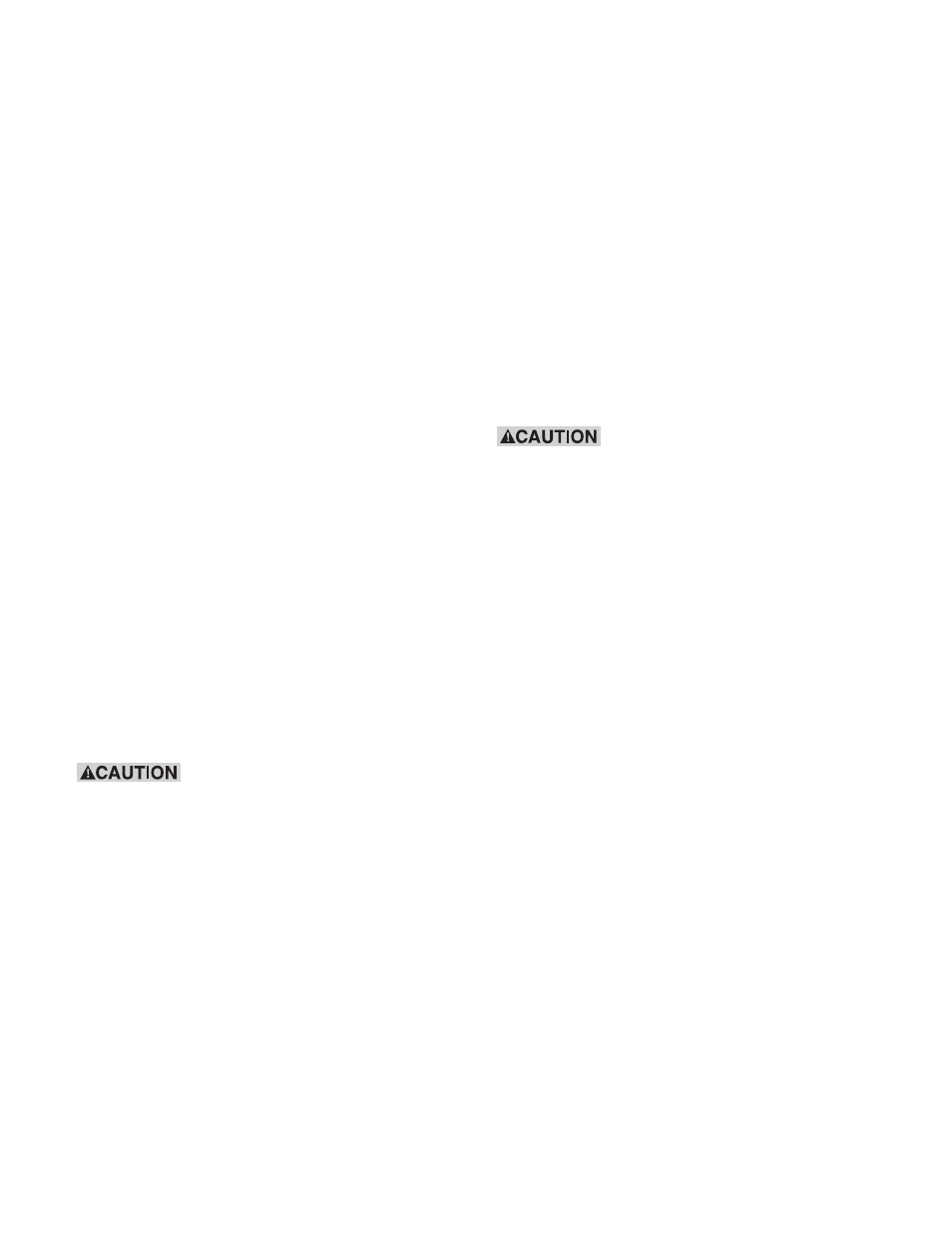
2
Warner Electric • 800-825-9050
819-0318
B. Secure the base to the modules with the four
(4) bolts provided.
Control Requirement
Electrically Released Permanent Magnet Brakes
must use one of Warner’s adjustable power
supplies. See the Service Installation sheet
included with the power supply for connection
information.
Note: All Electrically Released Permanent
magnet modules are polarity sensitive.
Therefore, the (+) wire must be connected to
the positive terminal and the (-) wire to the
negative terminal. Potentiometer control will
then provide adjustment for the proper brake
release point.
Switching of clutch and brake with this type of
module should allow both clutch and brake to
be engaged and disengaged simultaneously for
proper operation.
Brake Release Adjustment
Instructions for setting the optimum release
voltage of permanent magnet applied/
electrically released brakes.
The following procedure will
result in the brake releasing and allowing the
load to be free to move. Be sure the load is in
a safe condition before proceeding with this
process.
In a permanent magnet applied/electrically
released brake, the attractive force between the
brake surfaces is created by permanent
magnets. The brake is electrically released by
applying DC power to the electro-magnetic coil
in the brake that opposes the permanent
magnets. Electrically released brakes are
polarity sensitive: the positive lead of the power
supply must be connected to the positive lead
of the brake, and the negative lead of the power
supply must be connected to the negative lead
of the brake. The power supply applied to the
brake must also be adjustable so that the
optimum release voltage for each individual
brake can be determined and set.
The following procedure describes how to set
the adjustable power supply to the optimum
release point of the brake. A volt-meter is
required to perform the procedure.
No power is applied to motor
during this procedure. Power normally
supplied by motor to brake control should be
supplied by alternate method.
After control is adjusted per steps below,
brake control may need to be fine tuned
(adjusted) with motor running to compensate
for any changes in supply voltage used.
1. With power off, connect the positive lead of
the power supply to the positive lead of the
brake and the negative lead of the power
supply to the negative lead of the brake.
2. Connect a volt-meter to measure the voltage
applied across the brake.
3. Adjust the power supply to its lowest
possible output, then energize the power
supply only, to apply power to the brake.
4. Starting from the low point, slowly increase
the applied voltage until the brake armature
disengages from the magnet. Note and
record the applied voltage at this point.