Harrington Hoists and Cranes MCR Trolley User Manual
Page 36
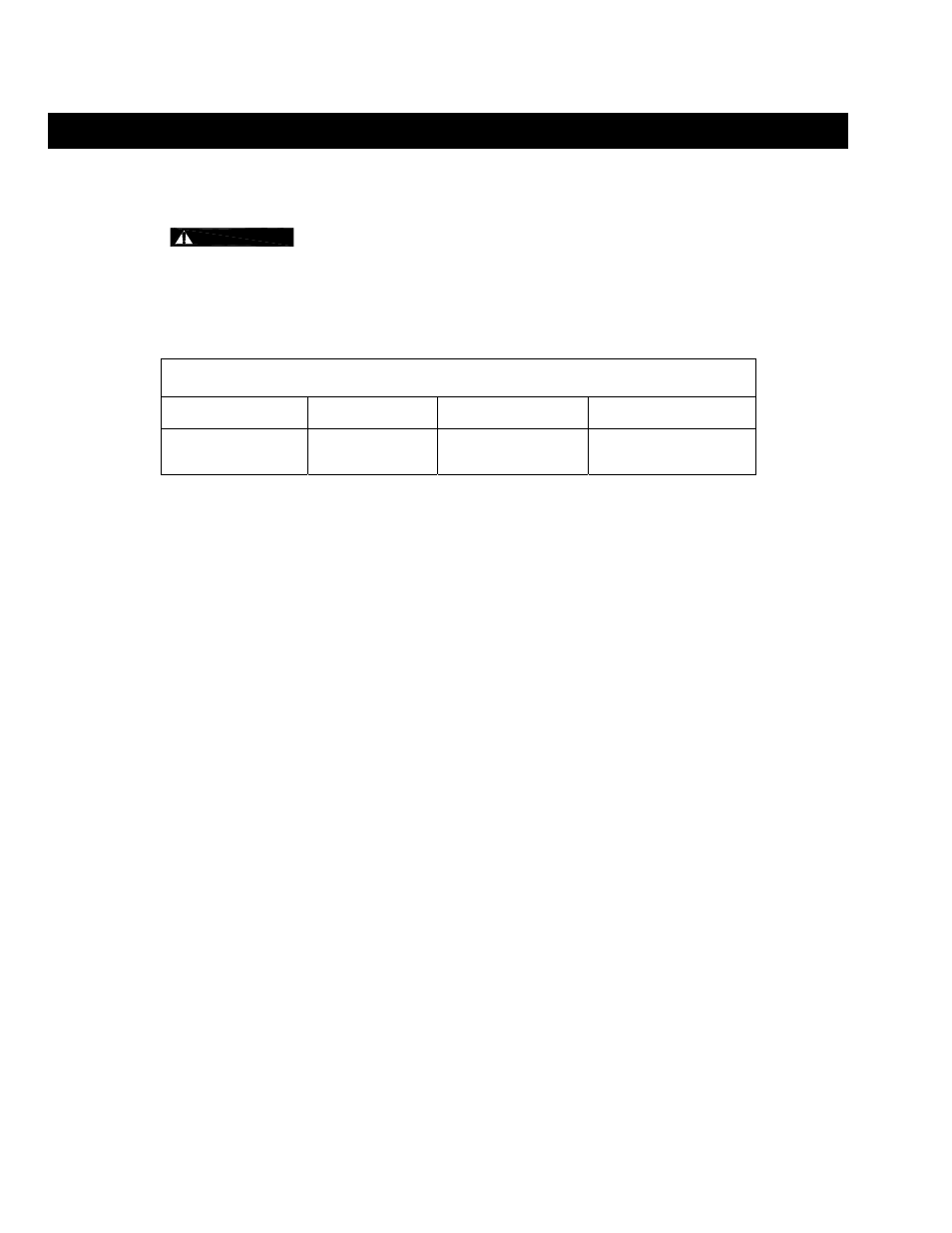
36
6.0 Maintenance & Handling
6.1
Air Trolley Motor Lubrication
6.1.1
See Section 3.7 for lubrication requirements.
6.1.2
CAUTION
Lubrication to the motor will be provided primarily by the air supply lubricator. The
recommended amount is 10-15 drops/minute (2-3cc/min.). Refer to
Table 6-1
below for the approved
lubricant for use with your air hoist.
6.1.3
Additional lubrication to the reduction gears is not necessary. When disassembling the hoist for service
or repair, apply new grease to the gears before reassembling the hoist.
Table 6-1
Table of Approved Lubricants
Lubrication Grade Application Part
Location
Turbine Oil
ISO VG 32-56 or
equivalent
Air motor
Lubricator
6.2 Air
Trolley
Lubrication
6.1.1
Lubricate the following trolley components with NLGI (National Lubricating Grease Institute) #2 or
equivalent grease.
6.1.2
Track Wheel Gear – Clean and re-grease the Track Wheel gears and motor output pinion every three
months (more frequently for heavier usage or severe conditions). Do not use an excessive amount of
grease and avoid getting any grease on the running surfaces of the Track Wheels or the beam.
6.1.3
Gear Box – The reduction gearing in the motor should be cleaned and lubricated at least once per year
for normal usage. Clean and lubricate the reduction gear assembly more frequently for heavier usage
or severe conditions. Gain access to the gears by removing the four bolts that mount the motor
assembly to the trolley Side Plate. Make sure to properly orient and reuse the neoprene gasket
between the motor and Side Plate.
6.1.4
Suspension Pins, Bolts and Shafts – Grease at least twice per year for normal usage (more frequently
for heavier usage or severe conditions).
6.3 Brake
6.1.5
The trolley motor brake is NOT adjustable.
6.1.6
Motor Brake Removal – Evenly remove the four Bolts that attach the Brake Cover to the Case to
release the brake spring. Carefully remove the Cover and brake components.
6.1.7
Brake Inspection – The brake is designed for a long life and should provide years of trouble-free
service. If the brake is being inspected due to excessive trolley drift during operation (see
Section 5.7
),
disassemble the motor brake and inspect all motor brake parts. Braking surfaces should be clean and
smooth. Replace the Brake Drum and/or Brake Piston if necessary. For normal inspections, the Brake
Drum and Brake Piston wear should be measured as follows.
1)
Refer to Table 5-6.
2)
Measure the distance "A" using calipers. Make sure the Brake Piston is square against the Brake
Drum.
3)
Compare the measurement with the values listed in Table 5-6. Replace the Brake Drum and/or
Brake Piston if the "A" measurement exceeds the discard limit.