Ransburg EFM & EFMD Solvent Applicator 76480, 76482, 76485, 76488 User Manual
Page 21
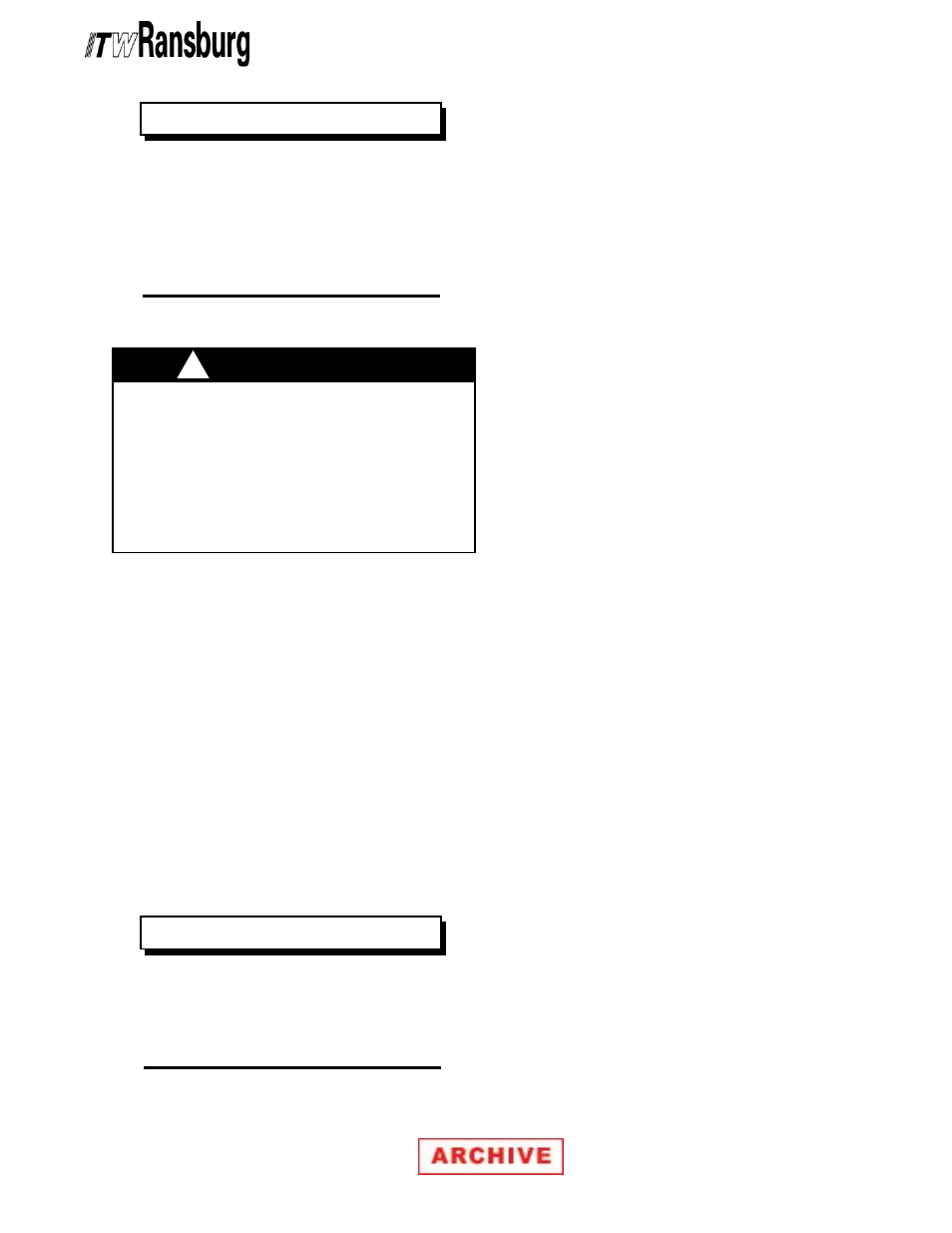
AA-99-01.1
1 6
1 6
1 6
1 6
1 6
EFM(D) Solventborne Robotic Atomizers - Operation
Fluid Flow Rate
Fluid Flow Rate
Fluid Flow Rate
Fluid Flow Rate
Fluid Flow Rate
Fluid flow is adjusted through the robot PLC by
varying the pilot pressure to the fluid regulator
within the EFM or EFMD spray applicator. Fluid
pressures from the circulating system may be as
high as 300 psig.
Atomizing Air
Atomizing Air
Atomizing Air
Atomizing Air
Atomizing Air
Adjustments are made through the robot PLC or a
manually adjustable air regulator. The lowest air
pressure required to break up the paint should be
used. Lower atomizing air pressures result in less
overspray and increased transfer efficiency.
>
If alignment occurs, turning off the
power supply will not usually break the
aligned metal particles. The paint located
between the applicator and the point of
first ground must be purged from the fluid
passages before normal spray can re-
sume.
N O T E
N O T E
N O T E
N O T E
N O T E
>
Most paints and solvents, including those
listed in "Polar and Non-Polar Solvents Chart"
in the "Maintenance" section, are toxic to a
certain degree and flammable or combustible.
Use them only in a well ventilated atmosphere.
Use protective equipment as required in the
Material Safety Data Sheet supplied with the
substance.
W A R N I N G
W A R N I N G
W A R N I N G
W A R N I N G
W A R N I N G
!!!!!
>
It has been observed when spraying
metallic paints that mottling (marble ef-
fect) can be reduced by increasing the
fan air pressure slightly higher than the
atomizing air.
N O T E
N O T E
N O T E
N O T E
N O T E
Fan Air
Fan Air
Fan Air
Fan Air
Fan Air
Adjusting the fan air increases or decreases the
size of the spray pattern. Increasing pressure
decreases pattern size. Pattern adjustment should
be made to suit the size and shape of the object
being painted. This adjustment is made through
the robot PLC or a manually adjustable air regula-
tor.
T
T
T
T
Trigger Control Air
rigger Control Air
rigger Control Air
rigger Control Air
rigger Control Air
The EFM and EFMD applicators require a minimum
of 70 psig trigger control air pressure to ensure
proper operation of the applicator piston and air
shuttle valves.
T
T
T
T
Trigger T
rigger T
rigger T
rigger T
rigger Timing
iming
iming
iming
iming
The LECU5004 MicroPak Control Unit provides a
means for the adjustment of the timing interval
between air, fluid, and high voltage. When the
applicator receives a trigger on signal from the
robot PLC, the air solenoid valve actuates. At the
same time the fluid solenoid valve timer is activated.
After the timer times out, the fluid solenoid and the
high voltage timer are activated. This timer delays
the start of the high voltage until after both the air
and fluid are activated.
Timing can be set in nine different timing
sequences, from a minimum of zero to a maximum
of 450 milliseconds. When the electrical signal
from the robot PLC is removed, the timing operates
in reverse. High voltage is shut off, fluid shuts off,
and, finally, the air solenoid valve shuts off. See
ITW Ransburg Service Manual
, MicroPak
, MicroPak
, MicroPak
, MicroPak
, MicroPak
Control Unit
Control Unit
Control Unit
Control Unit
Control Unit, for additional information on power
supply operation and control features.