Robot manifold – Ransburg EFM & EFMD Solvent Applicator 76480, 76482, 76485, 76488 User Manual
Page 16
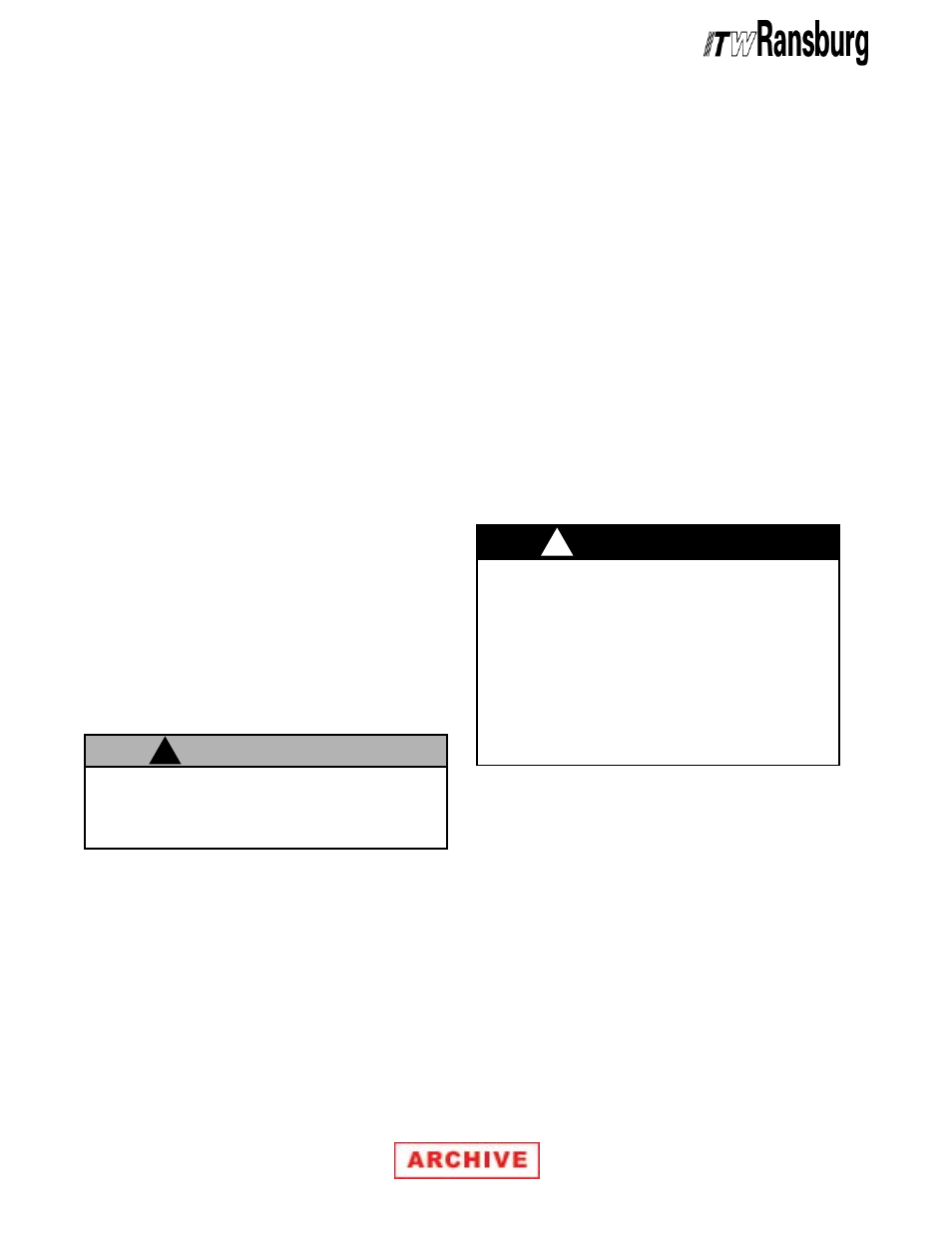
AA-99-01.1
1 1
1 1
1 1
1 1
1 1
EFM(D) Solventborne Robotic Atomizers - Installation
(See Figure 3)
(See Figure 3)
(See Figure 3)
(See Figure 3)
(See Figure 3)
Bundle the seven lengths of tubing along with the
two low voltage power cables [6 & 7] and route
them through the center of the robot face plate past
the horizontal arm to the bulkhead bracket. Use
the six 5mm x 20mm socket head cap screws [2]
included with the robot manifold assembly to attach
the manifold assembly to the face plate of the
robot.
Connect the tubes to the appropriate fittings on the
bulkhead bracket. Connect low voltage power
cables [6 & 7] of the robot manifold assembly to the
MicroPak Controller. Shown is the version used
with the P-150 series robots which connects to a
terminal strip.
If a terminal strip or connectors are used at the
bulkhead plates, you must run the exact same
cable from the terminal strip back to the MicroPak
controller. Intrinsic safety rules must be followed
when running these cables. See "Intrinisic Safe
Wiring" in the "Operation" section of this manual.
(See Figure 3)
(See Figure 3)
(See Figure 3)
(See Figure 3)
(See Figure 3)
Attach EFM spray applicator [1])to robot manifold
plate [4] with six (6) 5/16-18 x 1 inch hex socket
screws [5] included with each applicator.
Nylon guide pins (A10004-00) and nylon hex
socket screws (EMF-204-1) are offered as an
option. These nylon parts may be used in place of
the metal hex socket screws and metal guide pins.
The plastic parts are designed to break quickly if
aa applicator crash occurs. Possible applicator
or robot damage may be avoided if the spray
applicator breaks away from the robot wrist during
contact with the workpiece.
ROBOT MANIFOLD
ROBOT MANIFOLD
ROBOT MANIFOLD
ROBOT MANIFOLD
ROBOT MANIFOLD
ASSEMBL
ASSEMBL
ASSEMBL
ASSEMBL
ASSEMBLY
Y
Y
Y
Y
EFM SPRA
EFM SPRA
EFM SPRA
EFM SPRA
EFM SPRAY
Y
Y
Y
Y
APPLICA
APPLICA
APPLICA
APPLICA
APPLICAT
T
T
T
TOR
OR
OR
OR
OR
>
Leave 12-24 inches of extra length on all
lines to prevent extreme tension being applied
to these lines during robot movement.
C A U T I O N
C A U T I O N
C A U T I O N
C A U T I O N
C A U T I O N
!!!!!
>
Install and route the hoses and cable so
that they are NOT
NOT
NOT
NOT
NOT exposed to temperatures in
excess of 120
°
F. Ensure that all hose and
cable bends are NOT LESS THAN
NOT LESS THAN
NOT LESS THAN
NOT LESS THAN
NOT LESS THAN a 6 inch
(15cm) radius and are not subjected to more
than 360
°
of torsional twist. Failure to comply
with these parameters could cause equipment
malfunctions that might create HAZARDOUS
HAZARDOUS
HAZARDOUS
HAZARDOUS
HAZARDOUS
CONDITIONS!
CONDITIONS!
CONDITIONS!
CONDITIONS!
CONDITIONS!
W A R N I N G
W A R N I N G
W A R N I N G
W A R N I N G
W A R N I N G
!!!!!