Bearing air, Shaping air, Brake air – Ransburg Aerobell M Rotary Atomizer 78101 User Manual
Page 22
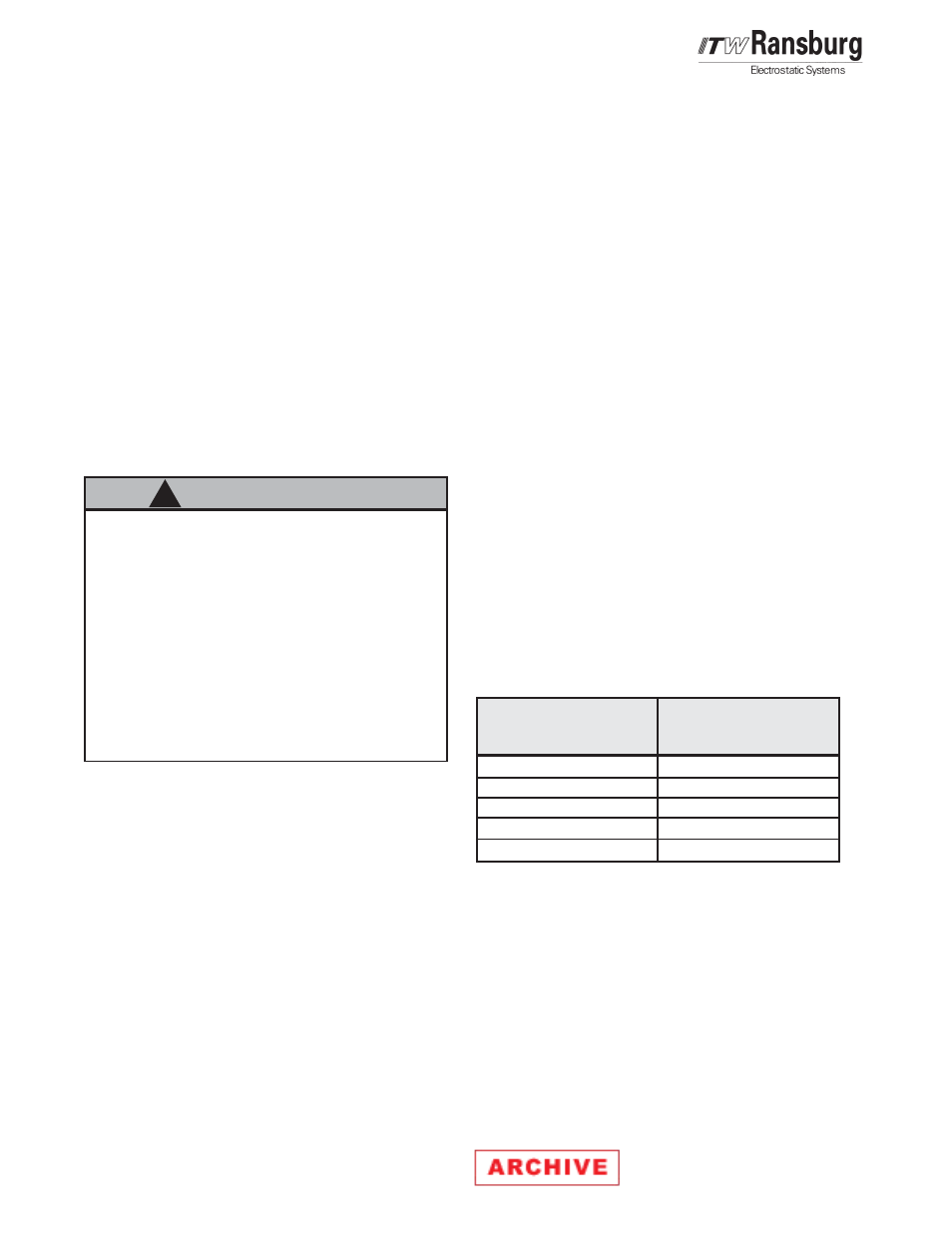
LN-9237-00.1
BEARING AIR
BEARING AIR
BEARING AIR
BEARING AIR
BEARING AIR
ADJUSTMENT
ADJUSTMENT
ADJUSTMENT
ADJUSTMENT
ADJUSTMENT
The nominal bearing air pressure is 90 psi,
measured at the rear of the atomizer. Minimum
pressure is 70 psi and maximum pressure is
100 psi. The turbine should never be operated
with less than 70 psi bearing air pressure.
Bearing air must be present when turning the
turbine on. Bearing air must remain on when
the turbine air is turned off until the turbine stops
spinning. Never turn off bearing air to cause the
turbine to stop spinning. If connected, brake air
can be used to slow the turbine.
The Aerobell M is equipped with a bearing air
return line to monitor bearing air pressure at the
turbine manifold. When connected to the re-
mote Atomizer speed controller, operation of the
turbine will automatically be shut down when-
ever the bearing air pressure falls below 60 psi.
SHAPING AIR
SHAPING AIR
SHAPING AIR
SHAPING AIR
SHAPING AIR
Shaping air is used to shape the spray pattern.
Lower input pressure results in wider pattern
size, while higher input pressure reduces the
pattern size. Shaping air does not help atomize
the material, but will assist in the penetration of
atomized particles into cavity areas. Ideally,
shaping air should be kept at the minimum pres-
BRAKE AIR
BRAKE AIR
BRAKE AIR
BRAKE AIR
BRAKE AIR
Brake air is used to slow the turbine speed in a
minimum length of time. It is advantageous for
short cycle times during color change, or may
be used to reduce speed or stop the turbine.
Never operate brake air with the turbine air on.
Approximate brake times to reduce the turbine
speed are shown in Figure 13. These times are
based on 60 psi air pressure at the brake air
connector.
The use of brake air is optional, and may not be
required for many installations. The Atomizer
Module control system provides the circuitry for
automatic use of the brake air.
sure which will provide a proper finish for the
fluid being sprayed. Excessive shaping air will
cause some atomized particles to blow by the
target, reducing the wrap around effect at edges
and corners. Excessive shaping air may also
cause some paint particles to bounce back onto
the atomizer, causing the atomizer surface to
become contaminated.
Aerobell M Rotary Atomizer - Operation
18
18
18
18
18
Figure 13: Braking Time
Figure 13: Braking Time
Figure 13: Braking Time
Figure 13: Braking Time
Figure 13: Braking Time
To Brake From (RPM)
To Brake From (RPM)
To Brake From (RPM)
To Brake From (RPM)
To Brake From (RPM)
50,000 to 40,000
50,000 to 20,000
50,000 to 0
40,000 to 20,000
40,000 to 0
Seconds
Seconds
Seconds
Seconds
Seconds
(Approx.)
(Approx.)
(Approx.)
(Approx.)
(Approx.)
3.7
7.5
10.0
4.0
9.0
>
Bearing air must be on whenever the
turbine is operated. If not, severe bearing
damage will occur. It is recommended
that bearing air be left turned on at all
times, except during maintenance or
disassembly.
Bearing damage (and subsequent turbine
failure) caused by running the turbine
without bearing air will not be covered
under the ITW Ransburg warranty.
C A U T I O N
C A U T I O N
C A U T I O N
C A U T I O N
C A U T I O N
!!!!!