Archive, Rem automatic applicator - maintenance – Ransburg REM Automatic Applicator 73499 User Manual
Page 24
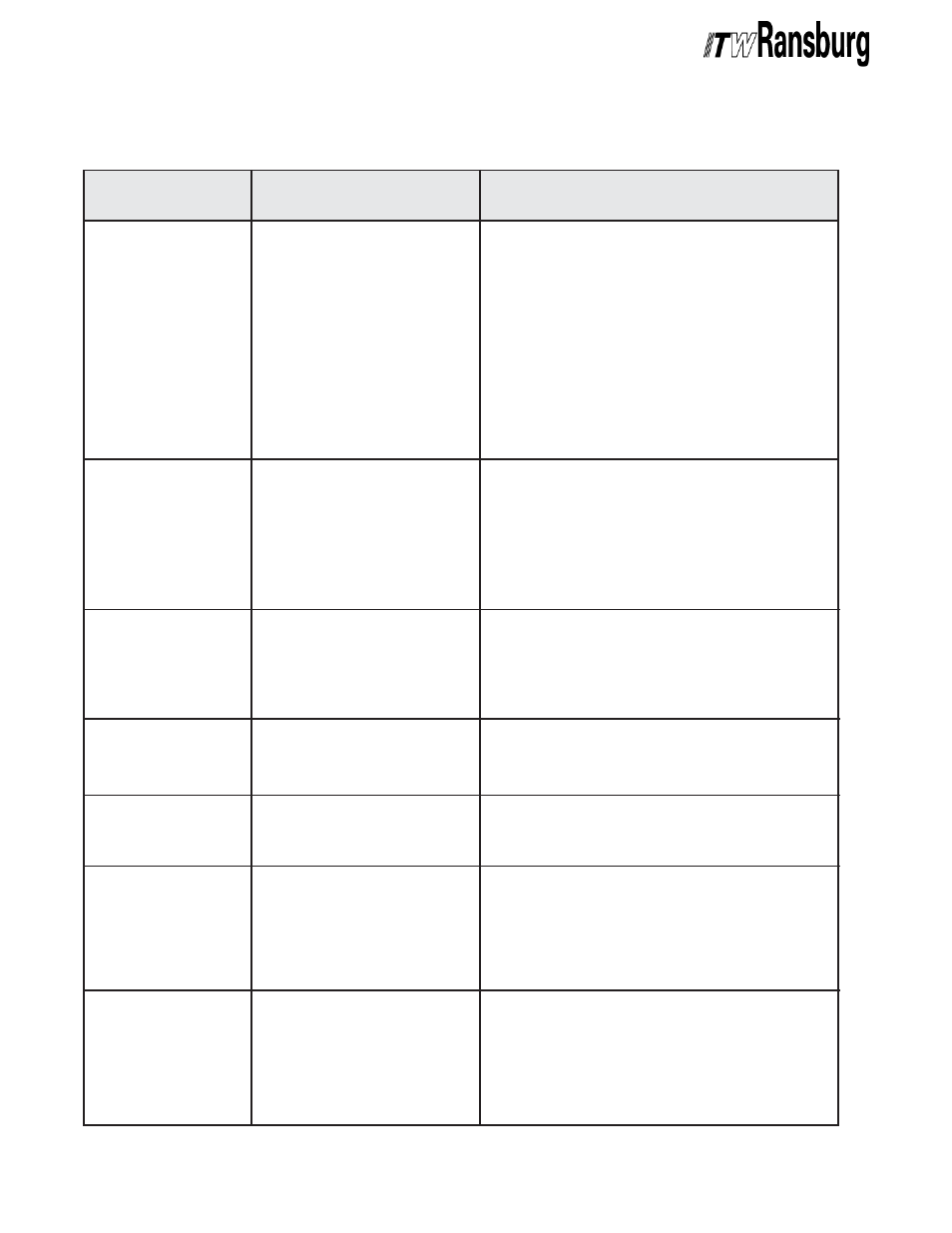
AA-87-02.3
1 9
1 9
1 9
1 9
1 9
REM Automatic Applicator - Maintenance
T
T
T
T
Troubleshooting Guide (Cont.)
roubleshooting Guide (Cont.)
roubleshooting Guide (Cont.)
roubleshooting Guide (Cont.)
roubleshooting Guide (Cont.)
General Problem
General Problem
General Problem
General Problem
General Problem
Possible Causes
Possible Causes
Possible Causes
Possible Causes
Possible Causes
Corrective Action
Corrective Action
Corrective Action
Corrective Action
Corrective Action
Excessive
Excessive
Excessive
Excessive
Excessive
Surging
Surging
Surging
Surging
Surging
Persistent Nozzle
Persistent Nozzle
Persistent Nozzle
Persistent Nozzle
Persistent Nozzle
Clogging
Clogging
Clogging
Clogging
Clogging
Paint Leaks
Paint Leaks
Paint Leaks
Paint Leaks
Paint Leaks
through Center of
through Center of
through Center of
through Center of
through Center of
Nozzle (Failure to
Nozzle (Failure to
Nozzle (Failure to
Nozzle (Failure to
Nozzle (Failure to
Shut Off)
Shut Off)
Shut Off)
Shut Off)
Shut Off)
Paint leaks
Paint leaks
Paint leaks
Paint leaks
Paint leaks
Arount the Nozzle
Arount the Nozzle
Arount the Nozzle
Arount the Nozzle
Arount the Nozzle
Cap
Cap
Cap
Cap
Cap
Paint Leaks at
Paint Leaks at
Paint Leaks at
Paint Leaks at
Paint Leaks at
Applicator Fluid
Applicator Fluid
Applicator Fluid
Applicator Fluid
Applicator Fluid
Inlet
Inlet
Inlet
Inlet
Inlet
Orange Peel or
Orange Peel or
Orange Peel or
Orange Peel or
Orange Peel or
Rough Finish
Rough Finish
Rough Finish
Rough Finish
Rough Finish
Paint Runs or has
Paint Runs or has
Paint Runs or has
Paint Runs or has
Paint Runs or has
Poor Hiding
Poor Hiding
Poor Hiding
Poor Hiding
Poor Hiding
Qualities
Qualities
Qualities
Qualities
Qualities
1. Restriction in pump air line
2. Insufficient pump capacity
3. Clogged paint filter
4. Low air volume capacity
5. Nozzle too large
6. Discharge lines too short to
dampen surging
1. Paint allowed to dry in
nozzle or line
2. Paint applicator filter too
coarse or damaged
3. Paint pigments too coarse
1. Packing too tight
2. Improper trigger adjustment
3. Defective or dirty valve seat
1. Loose nut
2. Seals worn
1. Thread leaks at high pres-
sure
1. Evaporation rate too fast
2. Poor atomization
3. Viscosity too high
1. Low solids paint
2. Low viscosity
3. Excessive delivery
1. Remove restriction.
2. Secure larger pump or reduce output.
3. Service or replace.
4. Check factory air capacity.
5. Replace with correct nozzle.
6. Install surge suppressor.
1. Flush lines with solvent after each use.
2. Replace or change to finer screen paint filter.
3. Pre-filter paint and/or use larger nozzle orifice.
1. Back off on packing nut.
2. Readjust.
3. Flush out or replace as necessary.
1. Clean paint from needle shat and tighten nut.
2. Replace seals.
1. Tighten nut.
1. Use slower evaporating solvent.
2. See “Poor Atomization”.
3. Add solvent or heat.
1. Use less solvent.
2. Use less solvent.
3. Use smaller nozzle, wider fan angle, lower
pump pressure.
ARCHIVE