Untitled – Dings Dynamics Group 90 Series End Mount NEMA 2 User Manual
Page 2
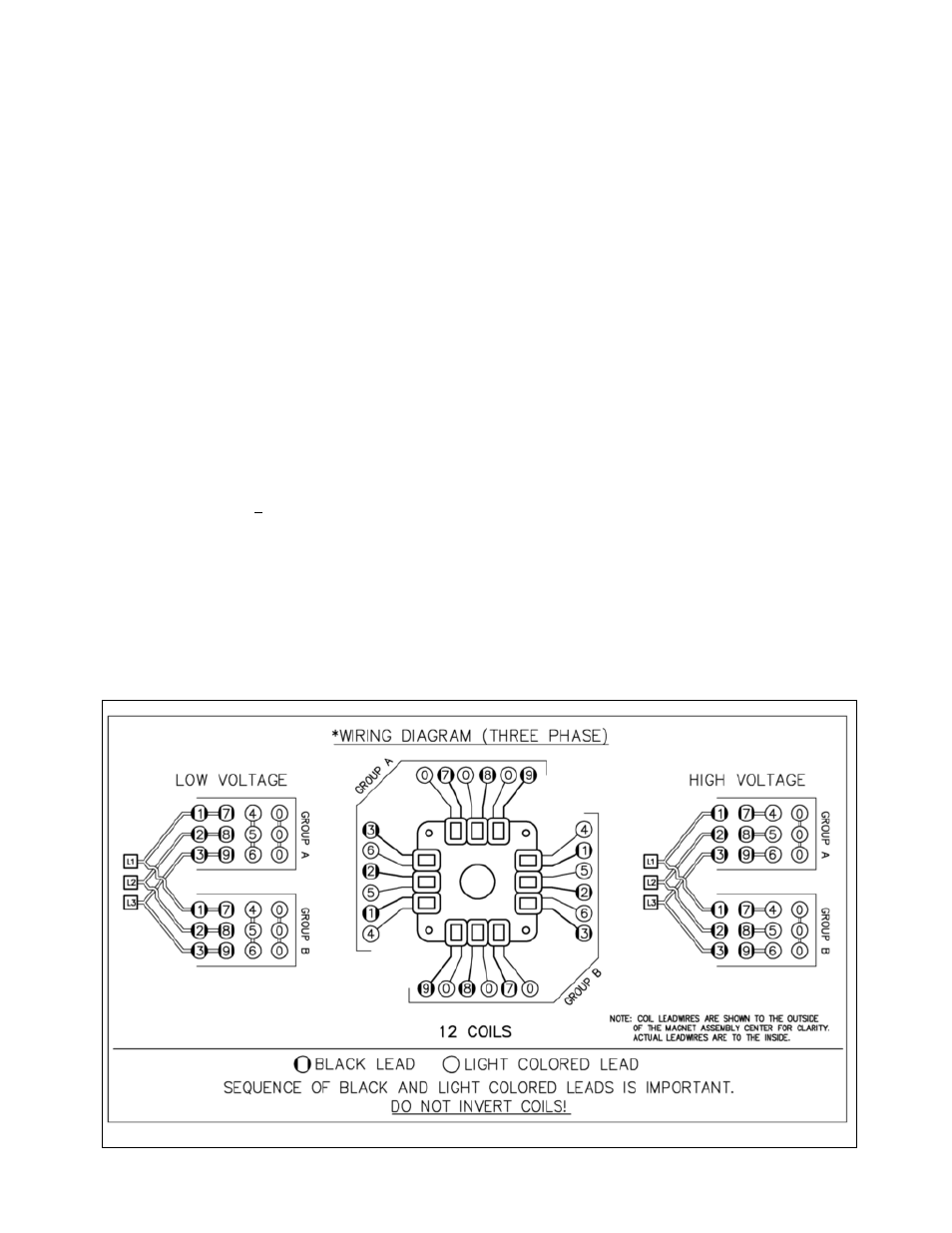
INSTALLATION
(See Figures 3 & 4 and Tables 1, & 2)
1. Remove hub (29) from brake and position on motor shaft with key
according to dimension “N”. Stamped part number on hub should
face away from motor. Tighten hub set screws with 60 lb. ft. torque.
2. Remove cover nuts (19) and cover (18).
3. Place brake on motor, guiding discs on hub.
4. Bolt brake to motor “C” face with four 5/8 inch socket head cap
screws. See Figure 5 for screw length through bracket.
5. Connect coil leads per appropriate wiring diagram in Figure 2 and
replace cover.
MANUAL RELEASE
(See Figure 3)
To operate release, rotate two rods (5) clockwise until stop screw
(17) hits pin. Brake will remain in released position until rods are
manually returned to original position, or until electrical power is
restored which automatically returns the release rods to the set
position.
TORQUE ADJUSTMENT
(See Figures 3 & 4 and Table 2)
Brake is factory set for rated torque per spring length “H”. To increase
stopping time and lower torque, turn four locknuts (9) counterclockwise,
increasing dimension “H”. All four springs must be set to the same length.
Do not decrease spring length “H” as this may cause coil to burn out.
WEAR ADJUSTMENT
(See Figures 3 & 4, Table 2)
Magnet gap “D” increases as friction discs wear. When gap approaches
“D” max., adjust gap to “D” min. dimension by turning nuts (11 and 13).
Magnet gap can vary from nominal + .005” between corners. After setting
gap, readjust torque spring length “H”. Apply 55 lb-ft torque to bottom
jam nuts (11). NOTE: Nut should be black in color.
CAUTION: MAGNET GAP MUST NOT EXCEED “D” MAXIMUM.
FRICTION DISC REPLACEMENT
(See Figures 3 & 4, Table 2)
*When the rotating friction disc (3) wears down to a thickness of 1/4”,
replace disc.
1. Remove cover nuts (19) and cover (18).
2. Unhook loop of torsion springs (10) from pins at rear of magnet
plate (12). Remove release stop screws (17) and shim washers
(14 & 15).
3. Remove adjusting lock nuts (11), magnet assembly (12), adjusting
nuts (13), torque nuts (9), washers (8), torque spring (7) and
pressure plate (6).
4. Remove friction disc (3) and stationary disc (4). Replace worn
friction discs.
5. Reassemble all parts in reverse order. Set spring length “H”
and magnet gap “D”. Apply 40 lb-ft torque to bottom jam nuts (11).
Assemble manual release. See following paragraph.
MANUAL RELEASE ASSEMBLY
(See Figure 3)
When assembling a standard manual release mechanism (Figure 3),
add only enough shim washers (14 & 15) to obtain proper release
action. Too many shim washers will prevent automatic reset when elec-
trical power is applied. Too few washers will prevent the motor shaft
from turning freely. Replace stop screws (17). Wind each torsion spring
(10) approximately 1/4 turn and hook spring loop over pin.
MAGNET COIL REPLACEMENT
(See Figures 2 & 3)
Remove magnet assembly (12) as outlined under FRICTION DISC
REPLACEMENT.
Coils are held in place with epoxy cement. Force coil off magnet mount-
ing plate and remove excess epoxy from all surfaces.
Replacement coils should be held in place with new epoxy cement. The
epoxy cement should be heat resistant and shock resistant.
When installing coils, it is very important to follow EXACTLY the
sequence of black and light colored leads as shown in wiring diagram
(Figure 2). The brake will not operate properly unless coils are all in the
correct position.
Figure 2. Wiring Diagram
2