Liquid Controls Precision Turbine Flowmeters User Manual
Page 4
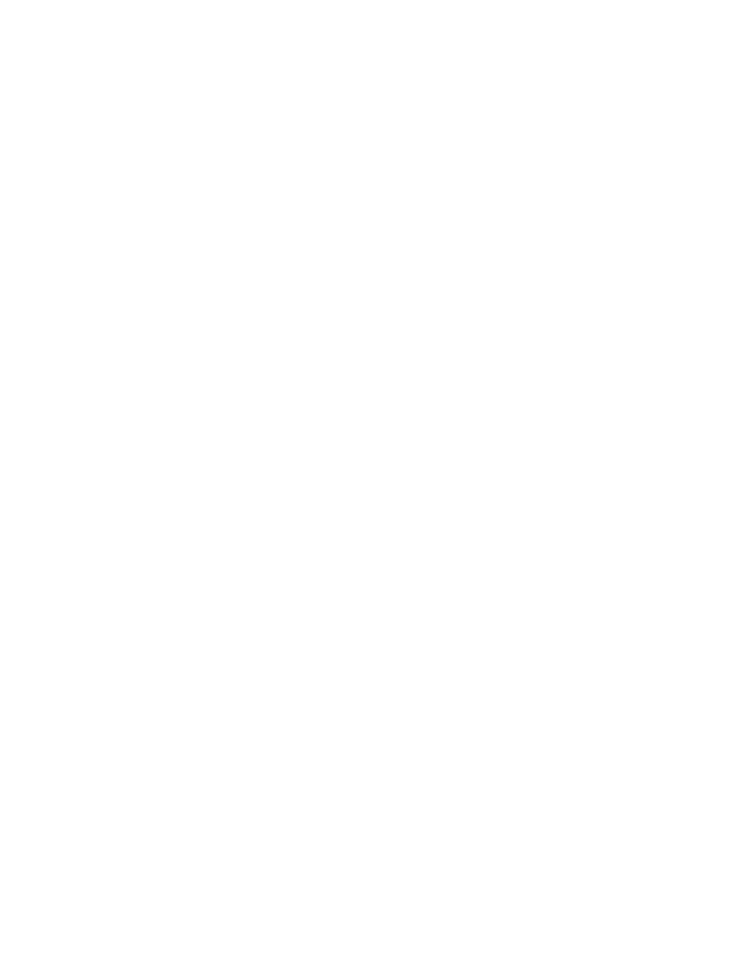
PRE-INSTALLATION INSPECTION
Your SPONSLER PRECISION TURBINE FLOWMETER is a measuring instrument capable of providing you with
high precision performance over a long period. It should be treated with care and not subjected to rough handling.
1. Unpack carefully and verify the information contained on the packing slip for proper MODEL Number, SERIAL
Number, and CALIBRATION Data.
2. Remove the instrument from the plastic packaging and remove the endfitting protectors from the flowmeter
housing.
3. Visually inspect the entire unit. Any visible damage should be reported to the manufacturer immediately.
4. Replace the endfitting protectors and return the Flowmeter to its plastic packaging. The unit may thus be stored
indefinitely until installation.
INSTALLATION
A. GENERAL PROCEDURE
1. Meter Position- FLOWMETERS are normally calibrated in a horizontal attitude. Best correlation of calibration,
therefore, occurs when installed and operated in this position. Meters may, however, be operated satisfactorily in
any position.
2. Flow Direction- ALL SPONSLER PRECISION TURBINE FLOWMETERS are marked “IN” and “OUT” and have
an arrow to indicate the proper direction of the flow. (Bi-Directional flowmeters excluded)
3. Meter Location-
A. Relative- When it is expected that flow will be intermittent, the meter should not be mounted at a low point in
the piping system. Solids that settle or congeal in the meter may affect the meter’s performance.
B. Tolerance to Mechanical Vibration- Although the SPONSLER PRECISION TURBINE FLOWMETER is
designed for rugged service, the meter life may be increased by location in a minimum vibration area.
C. Tolerance to Electrical Interference- In order to achieve optimum electrical signal output from the
flowmeter, consideration must be given to its isolation from ambient electrical interference such as nearby
motors, transformers, and solenoids. (Section IV Maintenance Electrical)
4. System Pressure-
A. Minimum Operation Pressure- A minimum operating pressure should be maintained to preclude a change in
the calibration factor due to various types of two phase phenomena. The minimum operating pressure is a
function of the vapor pressure of the fluid and the presence of other dissolved gases. Maintenance of the
system back pressure serves to avoid cavitation or fluid separation.
Calculation of the back pressure is by the following formula:
BP = (meter ∆P x 2) + (VP x 1.25)
Where:
BP = Back pressure required
∆P = Flowmeter pressure drop @ maximum flow
VP = Product vapor pressure at maximum temperature (psig)
B
. Maximum Meter Pressure- Safe working pressure for the flowmeter is determined by the size and type of
connecting fittings used and the materials of construction. Consult the factory for specifications for your
particular model.
Pg.2