Cashco P7 User Manual
Page 5
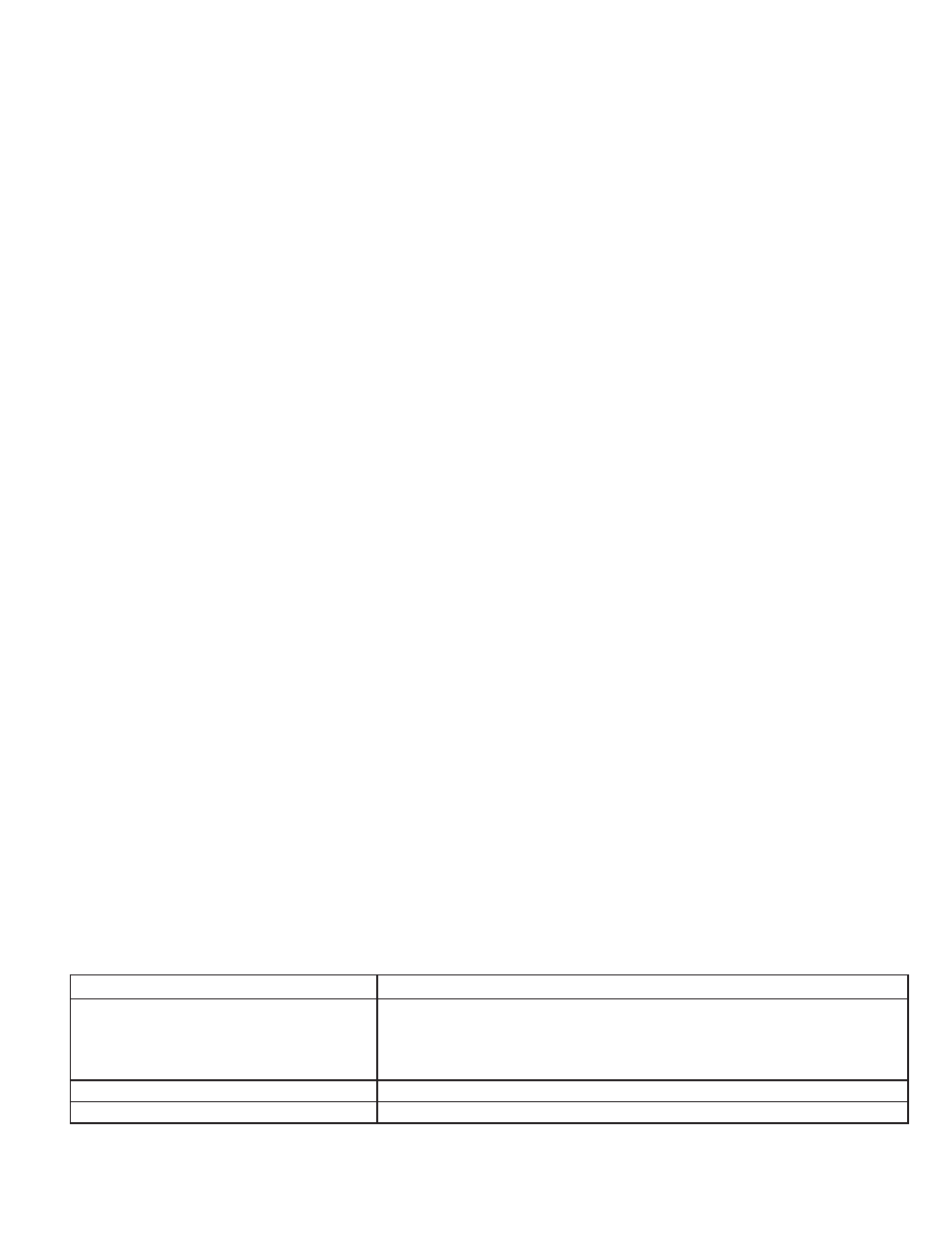
IOM-P7
5
9. Clean body (1) and all reusable parts according
to owner's procedures. NOTE: On regulators
originally supplied as “oxygen clean”, Option-M,
maintenance must include a level of cleanliness
equal to Cashco's cleaning standard #S-1134.
Contact factory for details.
10. Inspect and replace any necessary parts.
NOTE: Use only parts manufactured and sup-
plied by Cashco, Inc. for these products.
11. Insert plug (12) and spring (15) into body (1).
12. Place backup ring (18) into body cap (16), fol-
lowed by o-ring (19) and guide bushing (20) - fl at
side up.
13. Insert spiral retaining ring (21) into groove be-
hind guide busing (20) to lock parts in place.
14. Thread body cap (16) into the body (1) metal
to metal, compressing o-ring (17) into chamfer
of body.
15. Remove body from vise and rotate end to end
180 degrees to reclamp body in vise with body
cap (16) downwards.
16. Thread seat (11) with 0-ring (27) (CW) into body
(1) tighten metal to metal.
17. Position baffl e plate assembly (7) pin side down
into body (1); align spring pin (9) in proper hole
in body so pitot (8) is visible in center of outlet
treaded connection.
18. Install pin (10) through center of baffl e plate (7).
19. Refer to Section VI to re-assemble piston and
top works to a specifi c design.
G. Diaphragm Replacement - Ratio Loaded Design:
1. Securely install the body (1) in a vise with
upper & lower case assembly (43) (44)
directed upwards.
2. Remove all bolts (48) and nuts (49) from
upper & lower case assembly.
3. Remove upper case (44).
4. Remove & replace diaphragm (45).
NOTE: Ensure that pressure plate (46) is
aligned correctly on post (42),
5. Align bolt holes in upper case (44) with
holes in diaphragm (45) & lower case (43).
Insert bolts (48) through holes and thread nuts
(49) on bolts. Torque boling and nusts to 35 ft.
lbs.
SECTION VIII
VIII. TROUBLE SHOOTING GUIDE
1. Erratic operation; chattering.
Possible Causes
Remedies
A. Oversized regulator; inadequate rangeability.
A1. Check actual fl ow conditions, re-size regulator for minimum and maximum fl ow.
A2. Increase fl ow rate.
A3. Decrease regulator pressure drop; decrease inlet pressure by placing a throttling orifi ce in
inlet piping union.
A5. Before replacing regulator, contact factory.
B. Worn poppet; inadequate guiding. Vented Design
B. Replace trim (possible body replacement).
C. Weakened/broken poppet spring. Vented Design
C. Replace poppet spring. Determine if corrosion is causing the failure.
SECTION VII
VII.
CALIBARTION OF POPPET VENT - SPRING LOADED MODEL
Refer to Section IV - Startup - to establish system regulating pressure and fl ow conditions. Pop knob cover off of the
knob (38). Rotate vent adjustment screw (36) CW, until a hissing sound is heard - then stop. Then slowly turn the vent
adjustment screw CCW until the hissing sound stops. From this point, rotate the vent adjustment screw CCW one more
revolution and stop. The vent relieving function of this model is calibrated.