Cashco DA2 - Positive Differential User Manual
Page 12
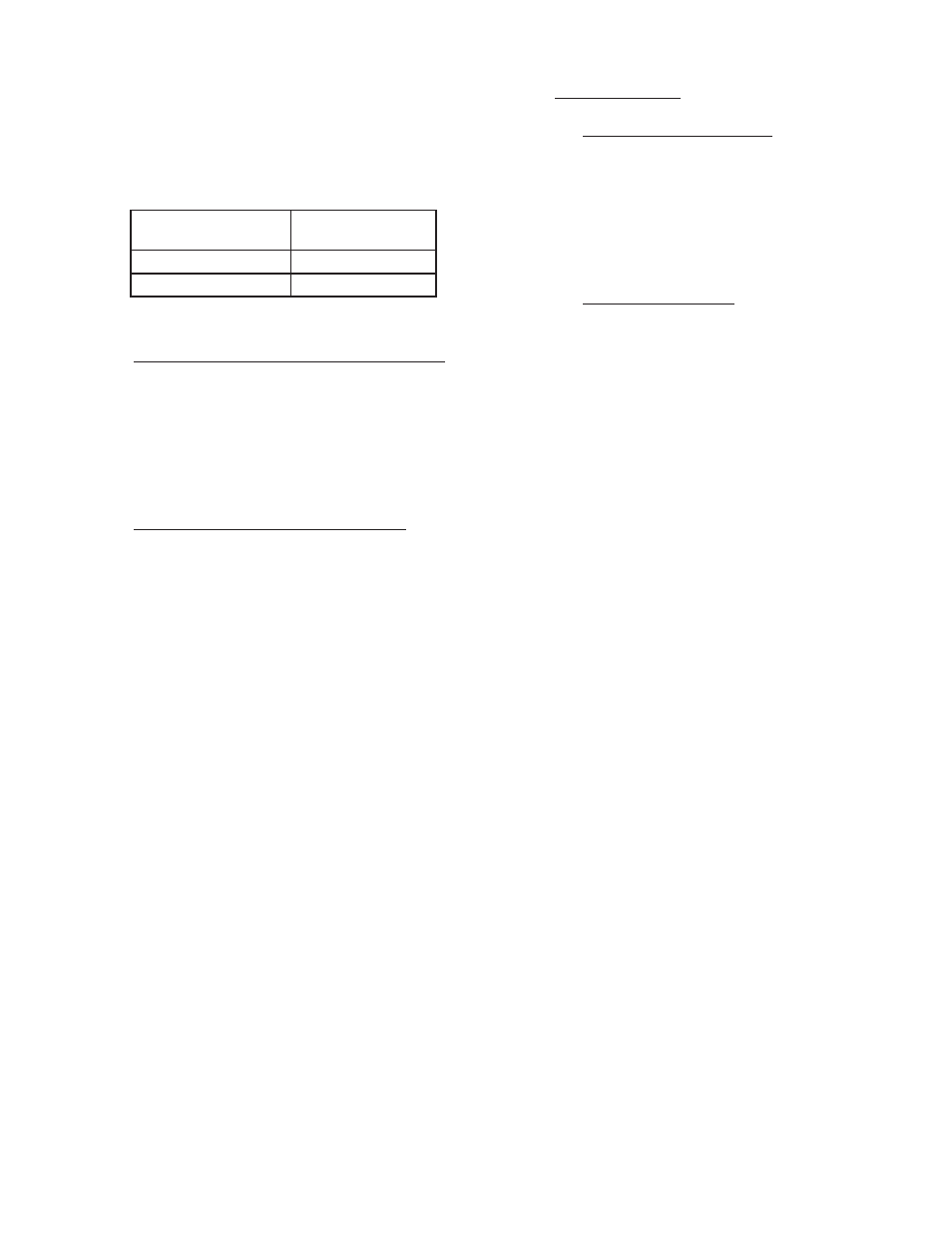
IOM-DA2
12
Body Size
in (DN)
Torque
ft-lb (N-m)
1/2" - 2" (15-50)
30-35 (41-47)
2 1/2" - 4" (65-100)
45-50 (61-69)
c. Leave pressure on through tightening
of bolt ing (11,12).
13. Evenly tighten the body bolting (11,12) in an
alternating cross pattern in one revolution
increments to the following torque value:
If supplied, remove pressure of previous Step 12.
G. Units with Supported Diaphragm Designs:
1. A supported diaphragm (9) construction is
designated as Opt-81.
2. For a Model DA2 the only “special” part to be
supplied is the support plate (35) fi tted into
a counter bore cut into the body (23).
H. Converting Internal/External Sensing:
1. Disassemble the regulator and remove the
diaphragm(s) (9) according to Steps 1-12 in
Part B – Main Regulator Disassembly.
2. To convert from internal to external sensing,
remove the drilled pipe plug (32) and install
a solid pipe plug. Reverse this step for con-
vert ing from external to internal sensing.
3. Reassemble the regulator according to Part
F – Main Regulator Reassembly.
I. Pressure
Testing:
1. Pressure Containment Test
(External Leak Test.).
a. See Section III, last paragraph and Table
1 for restrictions.
b. Spray leak detection solution over the
bolting, diaphragm edge, body, spring
chamber and all other pressure boundry
areas, during external leak test.
2. Inboard Leakage Test.
a. Release all range spring force by turning
adjusting screw CCW.
b. Pressurize inlet to 50 psig (3.5 Barg) with
air, GN
2
.
c. Tube outlet to a beaker of water to ob-
serve number of escaping gas bubbles.
3. Excessive leakage will require disassembly,
examination of sealing elements, correction
of problem, reassembly and retesting. Leak-
age path may be via plug/seat or dynamic
side seal. Before disassemblying the regu-
lator check the DAG-TB Table DAG-10 to
determine the acceptable inboard leak rates
of the seat and dynamic seal combination of
the regulator.