Dsc4, Instruction manual model – EBARA DSC4 User Manual
Page 15
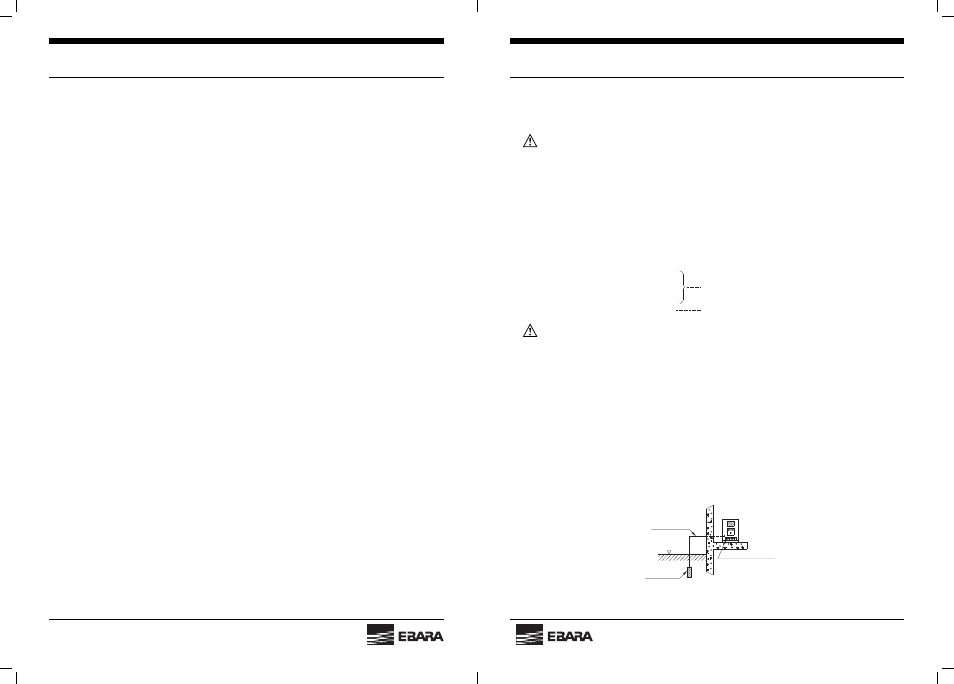
18
INSTRUCTION MANUAL
Model
DSC4
5. Operation
5.1 Operational Limitations
This pump is designed to operate under the following conditions:
(1) Liquid temperature : max. 40ºC (105° F)
(2) Liquid : This pump must not be used with sea water and corrosive chemicals or
combustible liquids.
(3) Lowest liquid level : Refer to lowest liquid level shown in the technical document.
(4) Voltage variations : The motor is designed to supply its rated output at variations of up
to±10% of the rated voltage at the rated frequency.
(5) Voltage balance : Balance among the supply phases should not exceed deviations in
excess of±1%.
(6) Frequency variations : The motor is designed do supply its rated output at variations of
up to +3% / -5% of the rated frequency at the rated voltage.
(7) Frequency of starts : The pump should not be started in excess of 10 times per hour.
5.2 Checking Rotation Direction (Figs. 18 and 19)
Check the motor for rotation direction by the following procedure after the pump has been
installed in the pump pit.
A reversing pump is no problem if operation is not prolonged.
(1) If the pump performance curve is available.
Open the sluice valve on the discharge side approximately half a turn (so that air is
released and a small quantity of liquid is discharged), and turn the main switch ON. With
all air released from the discharge pipe, fully close the sluice valve.
As this time, if the value of shut-off head (H1 + H2) (m),
where
H1 (m) Compound pressure gauge reading
H2 (m) Vertical distance from gauge to liquid surface
is generally in agreement with the pump performance at hand, the pump is operating
normally.
If the pump is reversed, a performance curve as denoted by dashed lines in Fig. 18 is
usually obtained, where the pump’s discharge pressure is lower than normal or specifi ed,
and a sudden rise electric current occurs with gradual opening of sluice valve.
In this event, change connections as shown in Fig. 19.
15
INSTRUCTION MANUAL
Model
DSC4
4. Electric Wiring
4.1 Power Cable Connection
WARNING:
CHECK THAT THE POWER IS LOCKED OFF AND DISCONNECTED BEFORE
WORKING ON PUMP.
The electric wiring for a submersible motor is no different from that of an ordinary motor, except
that the direction of rotation cannot be easily verifi ed.
Wiring to wrong terminals results in a reversed motor, and to prevent this and to achieve best
results, the following wiring procedure is recommended.
Connect terminals L1, L2 and L3 to the secondary terminals L1, L2 and L3 of the electromagnetic
switch or breaker respectively. Connect the remaining terminal G to ground.
WARNING: WHEN PREPARING POWER CABLE LEADS FOR CONNECTION TO CONTROL,
IT IS ESSENTIAL THAT THE GROUND LEAD BE LONGER THAN THE POWER LEADS. THE GROUND
LEAD MUST HAVE AT LEAST 2” (50 MM) SLACK REMAINING AFTER CONNECTION, WHEN
SPACE PERMITS. THIS IS DONE FOR ELECTRICAL SAFETY. IF THE CABLES IS MISTAKENLY
PULLED OUT, THE GROUND LEAD WILL BE THE LAST WIRE BROKEN.
4.2 Grounding (Fig. 14 and Table 2)
Be sure to connect the ground line (labeled “G”) to ground. Prior to grounding, ensure that the
wire is the specifi ed one (labeled “G”).
Also, verify that grounding continuity has been established inside the motor by checking that
ground wire (labeled “G”) is electrically conductive with the bolt on the top of the motor (to be
stripped of paint).
Ground the motor according to local codes.
Ground
Power source
G
L3
L2
L1
Ground terminal
Ground wire
Ground
plate
G.L
Fig. 14