Atec Agilent-53132A-53131A-53181A User Manual
Page 8
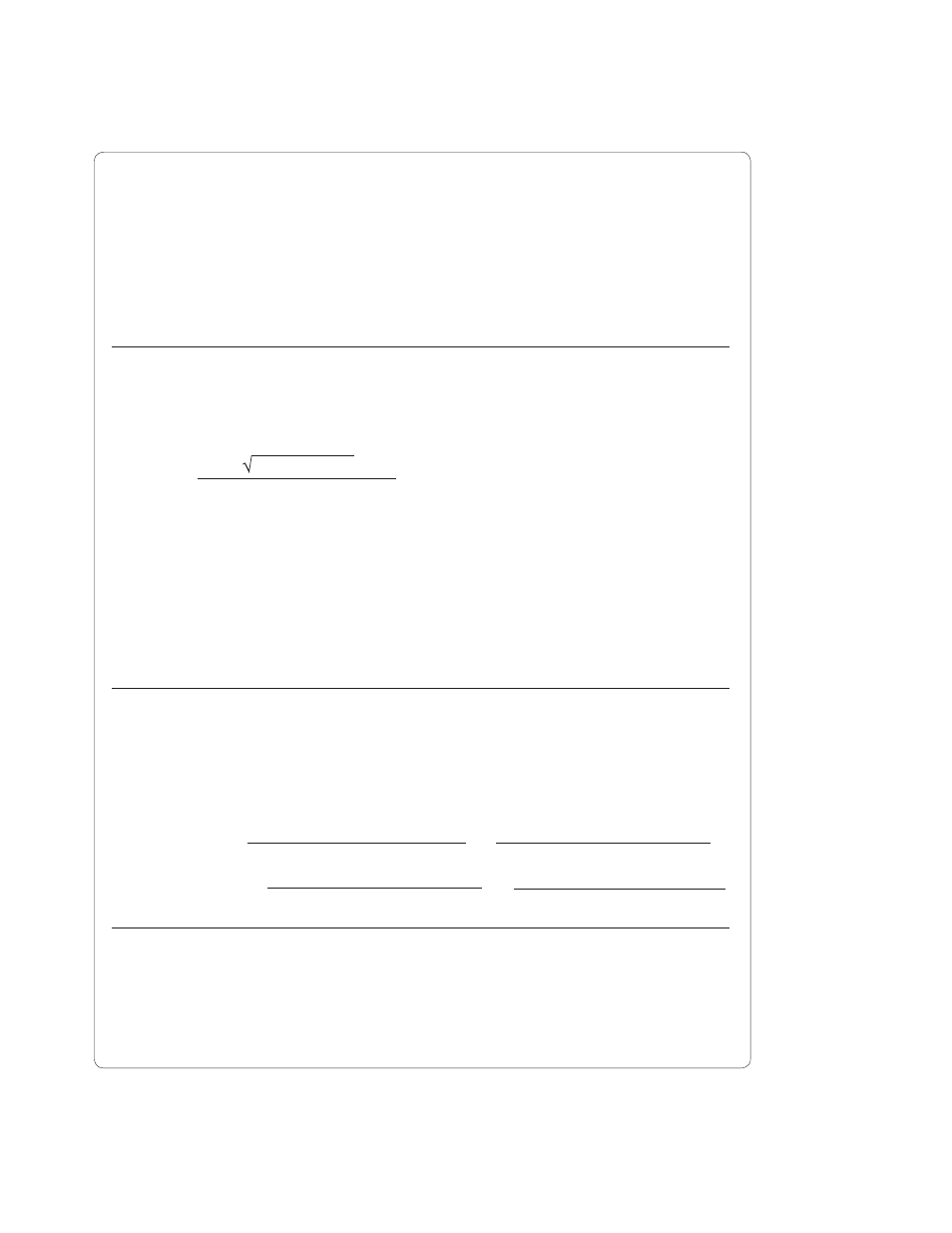
8
Fractional time base error (see graph 3)
Time base error is the maximum fractional frequency variation of the time base due to aging or
fluctuations in ambient temperature or line voltage:
∆f
∆f
∆f
Time base error =
(
— Aging rate + — Temperature + — Line voltage
)
f
f
f
Multiply this quantity by the measurement result to yield the absolute error for that measurement.
Averaging measurements will not reduce (fractional) time base error. The counters exhibit negligible
sensitivity to line voltage; consequently the line voltage term may be ignored.
Trigger error
External source and input amplifier noise may advance or delay the trigger points that define the
beginning and end of a measurement. The resulting timing uncertainty is a function of the slew rate
of the signal and the amplitude of spurious noise spikes (relative to the input hysteresis band).
The (rms) trigger error associated with a single trigger point is:
Trigger error =
Input signal slew rate at trigger point
(in seconds)
+
(E )
input
2
(E )
signal
2
where
E
input
= RMS noise of the input amplifier: 1 mVrms (350 µVrms typical). Note that the internal
measurement algorithms significantly reduce the contribution of this term.
E
signal
= RMS noise of the input signal over a 225 MHz bandwidth (100 kHz bandwidth when the
low-pass filter is enabled). Note that the filter may substantially degrade the signal’s slew rate at
the input of the trigger comparator.
For two-trigger-point measurements (e.g. rise time, pulse width), the trigger errors will be referred
to independently as start trigger error and stop trigger error.
Trigger level timing error (see graph 6)
Trigger level timing error results from a deviation of the actual trigger level from the specified level.
The magnitude of this error depends on resolution and accuracy of the trigger level circuit, input
amplifier fidelity, input signal slew rate, and width of the input hysteresis band.
The following equations should be summed together to obtain the overall trigger level timing error.
At the “High” sensitivity input setting, the hysteresis band can be assumed to be the sensitivity of
the counter input (see page 2). Reduction of input sensitivity or use of the attenuator will increase the size of this band.
Input hysteresis error:
–
Trigger level setting error: ±
±
Differential channel error
The differential channel error term stated in several systematic uncertainty equations accounts for
channel-to-channel mismatch and internal noise. This error can be substantially reduced by performing
a TI calibration (accessible via the utility menu) in the temperature environment in which future
measurements will be made.
0.5 x hysteresis band
Input signal slew rate at start trigger point
15 mV ± (1% x start trigger level setting)
Input signal slew rate at start trigger point
15 mV ± (1% x stop trigger level setting)
Input signal slew rate at stop trigger point
0.5 x hysteresis band
Input signal slew rate at stop trigger point