Installation and maintenance instructions, Service notice, Description – Cla-Val 136-03/636-03 Technical Manual User Manual
Page 21
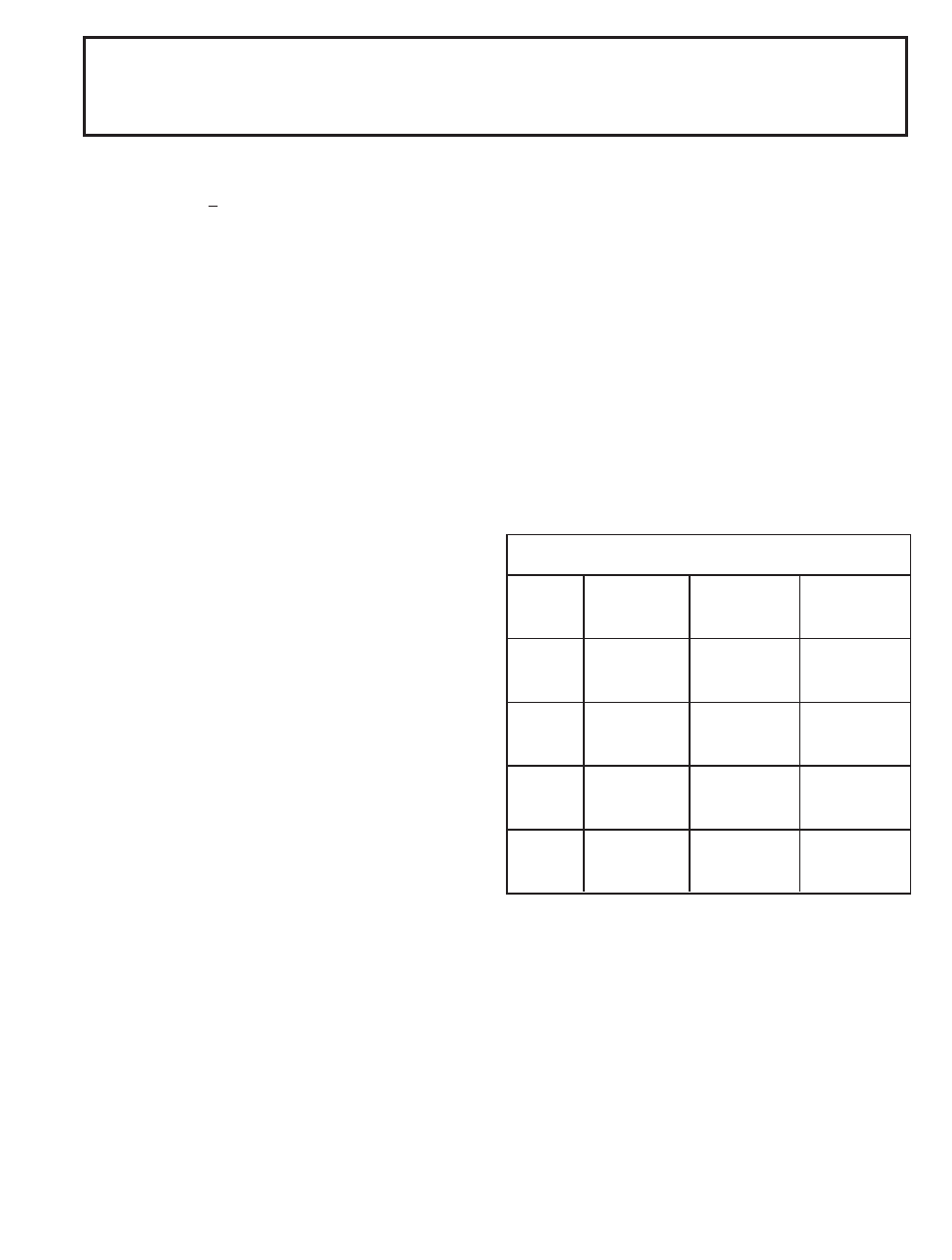
INSTALLATION AND
MAINTENANCE INSTRUCTIONS
OPEN-FLAME, GENERAL PURPOSE,
WATERTIGHT/EXPLOSIONPROOF SOLENOIDS
BULLETIN
8016G
ASCO
FORM NO. V6583R5
-SERVICE NOTICE-
ASCO
®
solenoid valves with design change letter "G" in the catalog
number (example: 8210G 1) have an epoxy encapsulated ASCO
®
Red
Hat II. solenoid. This solenoid replaces some of the solenoids with metal
enclosures and open-frame constructions. Follow these installation and
maintenance instructions if your valve or operator uses this solenoid.
DESCRIPTION
Catalog numbers 8016G1 and 8016G2 are epoxy encapsulated pull-type
solenoids. The green solenoid with lead wires and 1/2 " conduit connec-
tion is designed to meet Enclosure Type 1 -General Purpose,Type 2-
Dripproof,Types 3 and 3S-Raintight, and Types 4 and 4X-Watertight. The
black solenoid on catalog numbers prefixed "EF" is designed to meet
Enclosure Types 3 and 3S-Raintight, Types 4 and 4X-Watertight, Types 6
and 6P-Submersible, type 7 (A, B, C, & D) Explosionproof Class 1,
Division 1, Groups A, B, C, & D and Type 9 (E, F, & G)-Dust-lgnitionproof
Class 11, Division 1, Groups E, F, & G. The Class 11, Groups F & G Dust
Locations designation is not applicable for solenoids or solenoid valves
used for steam service or when a class "H" solenoid is used. See
Temperature Limitations section for solenoid identification and name-
plate/retainer for service. When installed just as a solenoid and not
attached to an ASCO valve, the core has a 0.250-28 UNF-2B tapped hole,
0.38 minimum full thread.
Series 8016G solenoids are available in:
• Open-Frame Construction
The green solenoid may be supplied with 1/4 spade, screw, or
DIN terminals (Refer to Figure 4).
• Panel Mounted Construction
These solenoids are specifically designed to be panel mounted by the
customer through a panel having a .062 to .093 maximum wall thickness.
(Refer to Figure 3 and section on Installation of Panel Mounted
Solenoid).
Optional Features For Type 1—General Purpose
Construction Only
• Junction
Box
This junction box construction meets Enclosure Types 2,3,3S,4, and
4X. Only solenoids with 1/4" spade or screw terminals may have a
junction box. The junction box provides a 1/2 conduit connection,
grounding and spade or screw terminal Connections within the junction
box (See Figure 5).
• DIN Plug Connector Kit No. K236 - 034
Use this kit only for solenoids with DIN terminals. The DIN plug connector kit
provides a two pole with grounding contact DIN Type 43650 construction
(See Figure 6).
OPERATION
When the solenoid is energized, the core is drawn into the solenoid base sub-
assembly. IMPORTANT: When the solenoid is de-energized, the initial
return force for the core, Whether developed by spring, pressure, or
weight, must exert a minimum force to overcome residual magnetism cre-
ated by the solenoid. Minimum return force for AC construction is 11 ounces,
and 4 ounces for DC construction.
INSTALLATION
Check nameplate for correct catalog number, service, and wattage. Check front
of solenoid for voltage and frequency.
WARNING: To prevent the possibility of electrical shock from
the accessibility of live parts, install the open-frame solenoid
in an enclosure.
FOR BLACK ENCLOSURE TYPES 7 AND 9 ONLY
CAUTION: To prevent fire or explosion, do not install solenoid and/or valve
where ignition temperature is less than 165˚ C. On valves used for steam
service or when a class "H" solenoid is used, do not install in hazardous atmos-
phere where ignition temperature is less than 180˚ C. See nameplate/retainer for service.
NOTE: These solenoids have an internal non-resetable thermal fuse to limit
solenoid temperature in the event that extraordinary conditions occur which could
cause excessive temperatures. These conditions include high input voltage,
a jammed core, excessive ambient temperature or shorted solenoid, etc.
This unique feature is a standard feature is a standard feature only in
solenoids with black explosionproof/dust-ignitionproof enclosures
(types 7&9).
IMPORTANT: To protect the solenoid valve or operator, install a strain-
er or filter, suitable for the service involved in the inlet side as close to the
valve or operator as possible. Clean periodically depending on service con-
dition & See ASCO Series 8600, 8601, and 8602 for strainers.
Temperature Limitations
For maximum valve ambient temperatures, refer to chart. The temperature limi-
tations listed, only indicate maximum application temperatures for field wiring
rated at 90°C. Check catalog number prefix and watt rating on nameplate to
determine maximum ambient temperature. See valve installation and mainte-
nance instructions for maximum fluid temperature. NOTE: For steam service,
refer to Wiring section, Junction Box for temperature rating of supply wires.
Minimum ambient temperature -40° F (-40° C). Positioning
Positioning
This solenoid is designed to perform properly when mounted in any position.
However, for optimum life and performance, the solenoid should be mounted ver-
tically and upright to reduce the possibility of foreign matter accumulating in the
solenoid base sub-assembly area.
Wiring
Wiring must comply with local codes and the National Electrical Code. All sole-
noids supplied with lead wires are provided with a grounding wire which is green
or green with yellow stripes and a 1/2" conduit connection. To facilitate wiring, the
solenoid may be rotated 360˚. For the watertight and explosionproof solenoid,
electrical fittings must be approved for use in the approved hazardous locations.
Additional Wiring Instructions For Optional Features:
• Open-Frame solenoid with 1/4" spade terminals
For solenoids supplied with screw terminal connections use #12-18 AWG strand-
ed copper wire rated at 90°C or greater. Torque terminal block screws to 10 ± 2
in-lbs (1,0 + 1,2 Nm). A tapped hole is provided in the solenoid for grounding, use
a #Y10-32 machine screw. Torque grounding screw to 15 -20
Temperature Limitations For Series 8016G Solenoids for use
Valves Rated at 6.1, 8.1,9.1,10.6 or 11.1 Watts
Watts
Rating
Catalog
Number Coil
prefix
Class of
Insulation
Maximum
ambient Temp.
˚F
6.1, 8.1, 9.1,
& 11.1
None, FB, KF, KP,
SF, SP, SC, & SD
F
125
6.1, 8.1, 9.1,
& 11.1
HB, HT, KB, KH,
SS, ST, SU, & ST
H
140
10.6
None, KF,
SF, & SC
F
104
10.6
HT, KH,
SU, & ST
H
104