Maintenance preventative maintenance, Disassembly, Valve stem thread size – Cla-Val 136-03/636-03 Technical Manual User Manual
Page 12
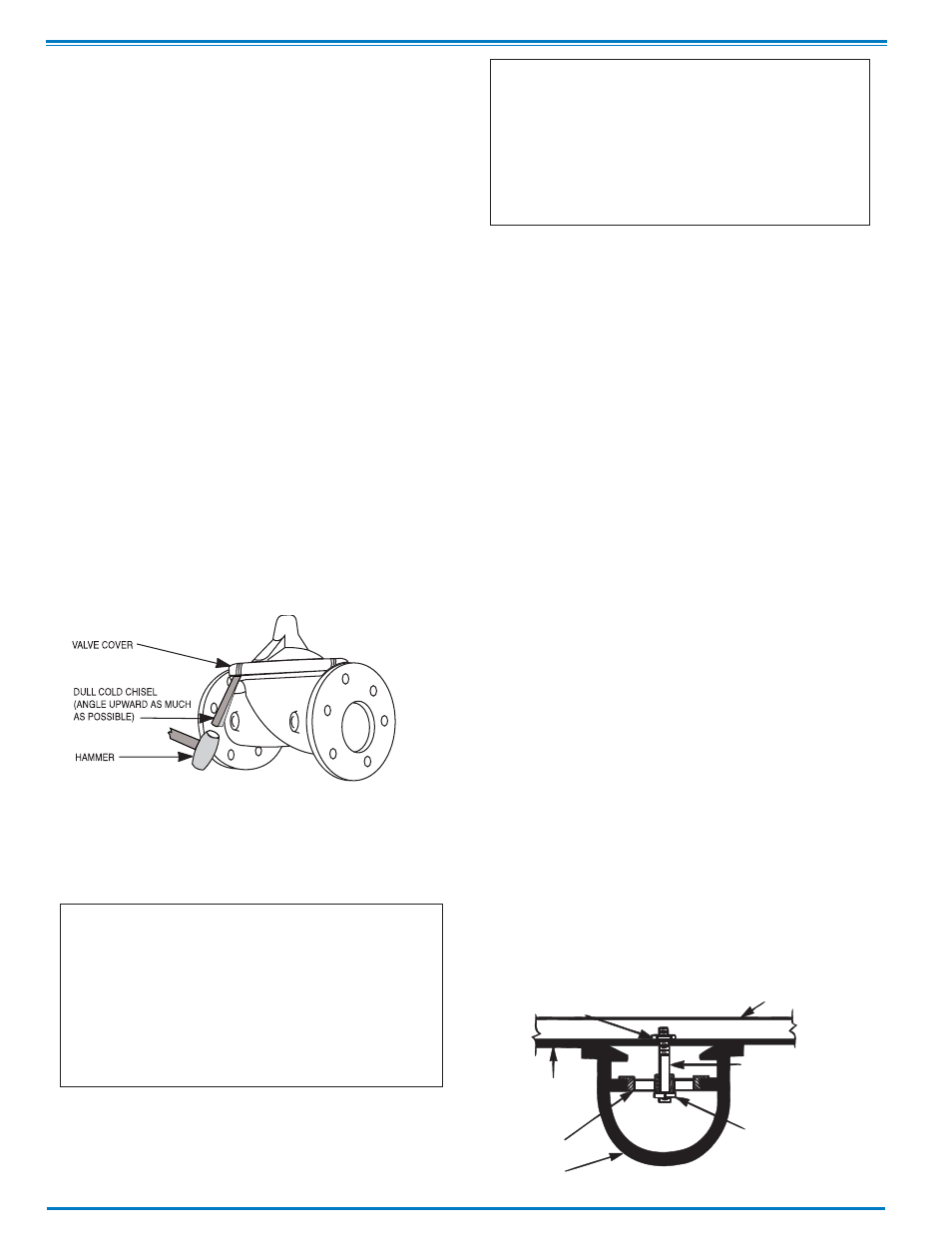
Maintenance
Preventative Maintenance
The Cla-Val Co. Model 100-01 Hytrol Valve requires no lubrication or
packing and a minimum of maintenance. However, a periodic inspec-
tion schedule should be established to determine how the operating
conditions of the system are affecting the valve. The effect of these
actions must be determined by inspection.
Disassembly
Inspection or maintenance can be accomplished without removing
the valve from the line. Repair kits with new diaphragm and disc are
recommended to be on hand before work begins.
WARNING: Maintenance personnel can be injured and equipment
damaged if disassembly is attempted with pressure in the valve. SEE
CAUTION.
1. Close upstream and downstream isolation valves and independ-
ent operating pressure when used to shut off all pressure to the
valve.
2. Loosen tube fittings in the pilot system to remove pressure from
valve body and cover chamber. After pressure has been released
from the valve, use care to remove the controls and tubing. Note and
sketch position of tubing and controls for re-assembly. The schemat-
ic in front of the Technical Manual can be used as a guide when
reassembling pilot system.
3. Remove cover nuts and remove cover. If the valve has been in
service for any length of time, chances are the cover will have to be
loosened by driving upward along the edge of the cover with a dull
cold chisel.
On 6” and smaller valves block and tackle or a power hoist can be
used to lift valve cover by inserting proper size eye bolt in place of
the center cover plug. on 8” and larger valves there are 4 holes (5/8”
— 11 size) where jacking screws and/or eye bolts may be inserted
for lifting purposes. Pull cover straight up to keep from damaging
the integral seat bearing and stem.
4. Remove the diaphragm and disc assembly from the valve body.
With smaller valves this can be accomplished by hand by pulling
straight up on the stem so as not to damage the seat bearing.
On large valves, an eye bolt of proper size can be installed in the
stem and the diaphragm assembly can be then lifted with a block and
tackle or power hoist. Take care not to damage the stem or bearings.
The valve won't work if these are damaged.
5. The next item to remove is the stem nut. Examine the stem
threads above the nut for signs of mineral deposits or corrosion.
If the threads are not clean, use a wire brush to remove as much
of the residue as possible. Attach a good fitting wrench to the nut
and give it a sharp “rap” rather than a steady pull. Usually
several blows are sufficient to loosen the nut for further removal.
On the smaller valves, the entire diaphragm assembly can be held
by the stem in a vise equipped with soft brass jaws before
removing the stem nut.
The use of a pipe wrench or a vise without soft brass jaws scars
the fine finish on the stem. No amount of careful dressing can
restore the stem to its original condition. Damage to the finish of
the stem can cause the stem to bind in the bearings and the valve
will not open or close.
6. After the stem nut has been removed, the diaphragm assembly
breaks down into its component parts. Removal of the disc from
the disc retainer can be a problem if the valve has been in serv-
ice for a long time. Using two screwdrivers inserted along the out-
side edge of the disc usually will accomplish its removal. Care
should be taken to preserve the spacer washers in water, partic-
ularly if no new ones are available for re-assembly.
7. The only part left in the valve body is the seat which ordinarily
does not require removal. Careful cleaning and polishing of inside
and outside surfaces with 400 wet/dry sandpaper will usually
restore the seat’s sharp edge. If, however, it is badly worn and
replacement is necessary, it can be easily removed.
Seats in valve sizes 1 1/4” through 6” are threaded into the valve
body. They can be removed with accessory X109 Seat Removing
Tool available from the factory. On 8” and larger valves, the seat
is held in place by flat head machine screws. Use a tight-fitting,
long shank screwdriver to prevent damage to seat screws. If upon
removal of the screws the seat cannot be lifted out, it will be nec-
essary to use a piece of angle or channel iron with a hole drilled
in the center. Place it across the body so a long stud can be insert-
ed through the center hole in the seat and the hole in the angle
iron. By tightening the nut a uniform upward force is exerted on
the seat for removal.
NOTE: Do not lift up on the end of the angle iron as this may force
the integral bearing out of alignment, causing the stem to bind.
VALVE STEM THREAD SIZE
Valve Size
Thread Size (UNF Internal)
1 1/4"—2 1/2"
10—32
3"—4"
1/4—28
6"—14"
3/8—24
16"
1/2—20
20
3/4-16
24"
3/4-16
30”
3/4-16
36”
3/4-16
COVER CENTER PLUG SIZE
Valve Size
Thread Size (NPT)
1 1/4"—1 1/2"
1/4"
2"—3"
1/2"
4"—6"
3/4"
8"—10"
1"
12"
1 1/4"
14"
1 1/2"
16"
2"
20” & 24"
2"
30” & 36”
2”
NUT
ANGLE OR CHANNEL IRON
LONG STUD OR BOLT
NUT OR BOLT HEAD
DO NOT
LIFT
VALVE SEAT
VALVE BODY
4